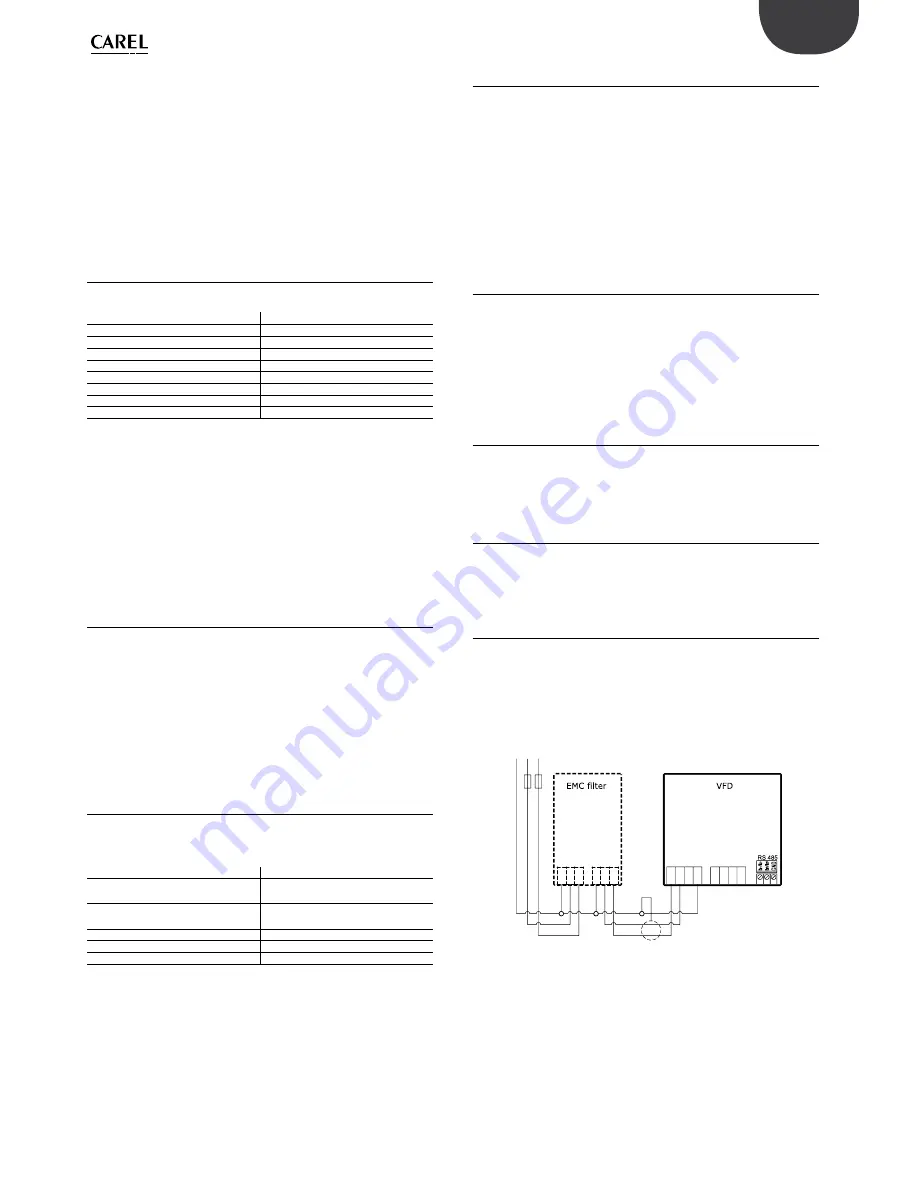
11
ENG
“
kit OEM KEC
” +030222160 - rel. 1.0 - 03/11/2015
•
The diameter of the feedwater inlet tubing must be greater than
or equal to the inlet connector on the unit. The material must be
compatible with the feedwater used (stainless steel for demineralised
water).
•
The water inlet lines must be flushed after installation and in any case
before starting the unit the first time.
•
Size the atomisation rack according to the minimum capacity of the
pumping unit used (see Tab.1.a).
•
Ambient operating temperature: 5...40 °C (41...104 °F)
•
Ambient operating humidity: <90% rH non-condensing
•
Index of protection: IP00
2.3 Feedwater characteristics
Feedwater requirements
Type/property
Requirement
Demineralised
ü
Mains
ü
1
Softened
ü
2
Temperature °C (°F)
1 to 40 (33.8 to 104)
4
Pressure MPa (bars)
0.3 to 0.7 (3 to 7)
3
pH
6.5 to 8.5
Total hardness (mg/l CaCO3)
< 160
Conductivity (μS/cm) a 20°C
< 400
Tab. 2.a
1
The use of mains water with a total hardness and conductivity over the
specified limits is allowed, however maintenance will need to be performed
more frequently on the atomisation rack nozzles, heat exchanger (if present)
and/or droplet separator (if present).
2
To reduce aggressiveness of softened water, the minimum total hardness
should be 20 mg/l CaCO
3
.
3
The range indicated in the table refers to the pump off. With the pump
operating, pressure must not fall below 1.8 bars.
4
A water temperature around 40°C does not improve absorption of the
droplets in the air.
2.4 Assembling the distribution rack
See technical l0500074ML.
The drain solenoid valves on the rack
•
should be fitted directly on the atomisation rack (P/N KEROUTV0*0,
purchased separately) if the pumping unit P/N is KEC*****00;
•
or are already fitted on the water circuit if the P/N is KEC*****10. In this
case, the connection tubing between rack and drain solenoid valves
on the pumping unit must meet the requirements for high pressure
tubing described in paragraph 2.2.
2.5 Fastening the electrical system
The KEC controller and inverter must be installed in the air handling unit’s
electrical panel. Table 2.b describes the limit conditions for storage and
operation.
Specification
Value
Ambient operating
temperature °C (°F)
5 to 40 (41 to 104)
Ambient operating
humidity %rH
< 90 non-condensing
Ambient storage temperature °C (°F) -20 to +60 (-4 to +140)
Ambient storage humidity %rH
< 90 non-condensing
Index of protection
IP20
Tab. 2.b
2.5.1
Fastening the KEC controller
This is installed on a DIN rail and occupies 13 modules. Once the controller
has been placed on the DIN rail, press it in lightly: the rear tabs will click
into place, signifying that the controller is correctly mounted. The tabs are
held in the locked position by return springs. To remove the controller,
simply use a screwdriver to release and lift the tabs.
The installation position in the electrical panel must guarantee good
physical separation between the controller and the power components
(solenoids, contactors, actuators, inverter, ...) and the corresponding
connection cables. The ideal situation would be to install the two circuits
in two separate cabinets. Proximity of the two circuits may cause random
failures that are not immediately evident. The structure of the electrical
panel must ensure correct cooling air flow.
2.5.2
Fastening the inverter
The inverter is secured to the EMC filter using M4 screws; the filter is in
turn screwed onto the electrical panel using M5 screws. Leave clearance
of at least 30 mm on the right and left, and at least 100 mm at the top and
bottom, so as to guarantee sufficient ventilation. The installation position
in the electrical panel must guarantee good physical separation between
the power cable and the serial cable running between the inverter and
KEC controller. Admissible pollution degree is ≤ 2 in accordance with UL
and EN 61439-1.
2.5.3
Fastening the bottom plate (if featured)
If the KEC controller and inverter are supplied already assembled on
the bottom plate, the complete plate then installed inside the electrical
panel.
2.6 Electrical connections
The electrical connections are the responsibility of the OEM, except for
the wiring from the terminal block to the electromechanical components
in the water circuit. The maximum length of the electrical connections
between the electrical components and the water circuit is 15 m.
2.6.1
Inverter power supply
The power supply, to be provided by the user, is:
•
230 Vac single-phase 50/60 Hz + earth for pumps P/Ns KEC***D***;
•
230 Vac single-phase 50/60 Hz + earth for pumps P/Ns KEC***U***.
This is connected to the inverter filter (L, N, PE) and then from there to the
inverter (L1, L2, PE), as shown in Fig. 2.e.
Inverter 230 Vac wiring
L3
L
N
PE
L
N
PE
F1
PE
PE
W
V
U
L2
L1
F2
PE N L
Fig. 2.e