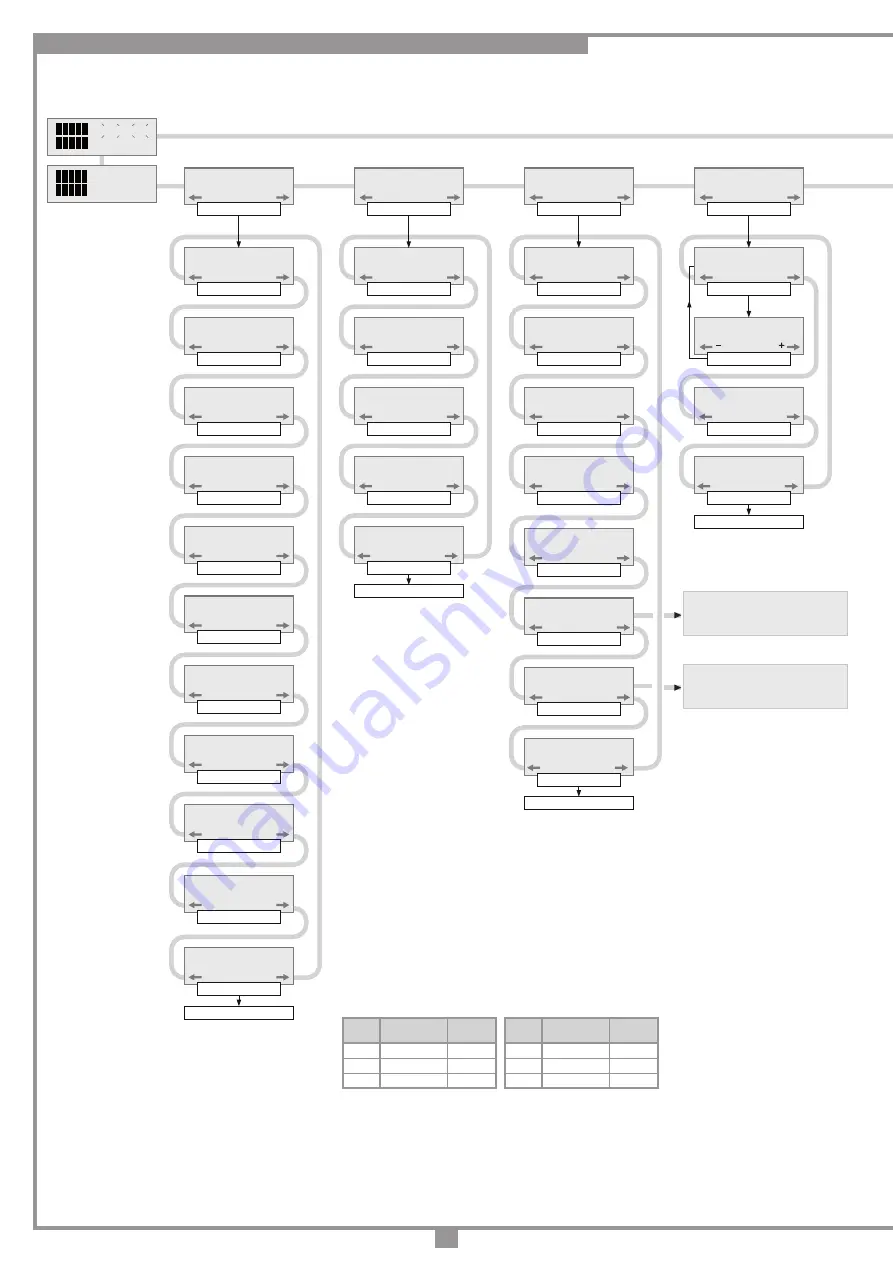
16
Value
Torque at
Torque at
slow speed top speed
1
25%
75%
2
25%
100%
3
36%
75%
Value
Torque at
Torque at
slow speed top speed
4
36%
100%
5
60%
75%
6
60%
100%
Press the arrows to increase or
reduce the value (max 240 seconds).
Keep the arrow keys pressed to scroll
the value rapidly.
Press OK to reset the parameters to the
factory default settings (excluding the
number of manouvres). Press EXIT
to quit without modifying the parameters
“PROG/OK” to confirm
BACK TO MOTION MENU
EXIT
OK
“PROG/OK” to set
RESET PARAMETERS
OK
“PROG/OK” to set
DIST. FROM OPEN
(6)
0...9 steps
“PROG/OK” to set
DIST. FROM CLOSE
(6)
0...9 steps
SEQUENTIAL COM.
OPEN-SHUT/
OPEN-STOP-SHUT
“PROG/OK” to set
AUTO-RECLOSING
ON/OFF
“PROG/OK” to set
“PROG/OK” to set
WARNING LIGHTS
FIXED/
INTERMITTENT
“PROG/OK” to set
INDICATOR LIGHT
(1)
FIXED/
INTERMITTENT
“PROG/OK” to set
PHOTOCELL INVERT
(2)
DURING CLOSING/
AND IN STOP
“PROG/OK” to set
“PROG/OK” to set
“PROG/OK” to set
INSTALLED MOTOR
LEFT/RIGHT
“PROG/OK” to set
“PROG/OK” to set
“PROG/OK” to confirm
BACK TO OPTIONS
PRE-FLASHING
ON/OFF
TEST FI
(3)
ON/OFF
TEST FS
(3)
ON/OFF
MEMO RADIO
ON/OFF
EXIT
OK
“PROG/OK” to set
FI CONTACT
NC/8K2
TB CONTACT
NC/8K2
“PROG/OK” to set
“PROG/OK” to set
“PROG/OK” to set
“PROG/OK” to confirm
BACK TO SAFETY DEVICES
FS CONTACT
NC/8K2
CP CONTACT
NC/8K2
EXIT
OK
“PROG/OK” to set
CURRENT SENSOR
(5)
LEVELS 1...5
“PROG/OK” to set
“PROG/OK” to set
LIMITED OPENING
1...9 meters
“PROG/OK” to set
ADJUST CONTRAST
0...63
CONTRAST
OK
“PROG/OK” to confirm
“PROG/OK” to confirm
SAFETY DEVICES
OK
“PROG/OK” to confirm
CANCELLATION
OK
MEMORISE
OK
“PROG/OK” to confirm
“PROG/OK” to confirm
“PROG/OK” to confirm
“PROG/OK” to confirm
BACK TO RADIO CODES MENU
CLEAR ALL MEMORY
OK
CHANNEL FUNCTION
OK
EXIT
OK
“PROG/OK” to confirm
REMOTE
OK
OPTIONS
OK
“PROG/OK” to confirm
MOTION
OK
PRESS ANY KEY
BACK TO TEST MENU
“PROG/OK” to confirm
TEST
OK
“PROG/OK” to confirm
DISPLAY
OK
“PROG/OK” to confirm
“PROG/OK” to set
“PROG/OK” to confirm
BACK TO DISPLAY MENU
EXIT
OK
REAR LIGHTING
ALWAYS ON/
60 SEC./30 SEC.
TORQUE SELECTION
(4)
LEVELS 1...6
PROGRAM
T B
F S
F I
CP
00.000.001
T B
F S
F I
CP
TEST
T B
F S
F I
CP
PRESS the
transmitter
channel to be
memorised
CANCELLING.....
MEMORISE [nr ...]
Activation 1
PRESS the
transmitter
channel to be
memorised
MEMORISE [nr ...]
Activation 2
MEMORISE [nr ...]
CODE MEMORISED
“PROG/OK” to confIrm
CLEAR ALL MEMORY?
OK
PRESS the
transmitter
channel to be
cancelled
CANCEL [nr ...]
Activation 1
PRESS the
transmitter
channel to be
cancelled
CANCEL [nr ...]
Activation 2
CANCEL [nr ...]
CODE CANCELLED
Exit
“PROG/OK” to set
CHANNEL A
COMMAND TD/TAL/TA/TC/
STOP/NO COMMAND
CHANNEL B
COMMAND TD/TAL/TA/TC/
STOP/ NO COMMAND
“PROG/OK” to set
“PROG/OK” to set
CHANNEL C
COMMAND TD/TAL/TA/TC/
STOP/ NO COMMAND
“PROG/OK” to set
CHANNEL D
COMMAND TD/TAL/TA/TC/
STOP/ NO COMMAND
“PROG/OK” to set
BACK TO CHANNEL FUNCTION MENU
EXIT
OK
OUT OF POS
T B
F S
F I
CP
STOP PROG
T B
F S
F I
CP
PROGRAM
T B
F S
F I
CP
Flashing on the display. You have to enter the programming mode to program the system.
During normal operation it indicates that the "automatic repositioning" procedure is about to take place. In
this case any commands received (TA, TC, TAL or TD) will automatically start this procedure.
This happens when an N.C. contact is activated (FI, FS, CP) during encoder programming or automatic
repositioning. Once the passive state of the security devices has been reset the gate will start moving
again automatically. It also happens if a blackout occurs during programming.
Safety device test error. Check the condition of the safety devices and make sure that the alarm cuts in
when an obstacle interferes with the beam (the relative LED will switch off). In case of anomalies replace
the damaged safety device or bridge the contact and deactivate the safety test (option menu).
This occurs when the programmer sends a command to the motor and nothing happens (the motor
doesn't move). Check the motor faston connections and the condition of the fuses "F2", "F3" and then
give another opening or closing command. If the motor still doesn't move you are faced with either a
mechanical problem or a problem with the programmer.
If this error occurs during normal motor operation it means that there is a problem with one of the encoder
signals. Check the relative connections and carry out automatic repositioning.
The gate movement direction is different from the encoder setting (eg. the gate moves in the closing
direction while the program is carrying out the opening stage). Check the motor power supply
connections.
Current sensor error. When the gate is not moving this symbol means there is a problem with the current
sensor.
When the safety edge intervenes the gate will automatically invert for 5 cm, both in the closing as well as
the opening direction, to free the obstacle it will then stop for 3 minutes and then continue moving in the
original direction after a 10 second preflashing period has elapsed.
When the sensor intervenes the gate will automatically invert for 5 cm, both in the closing as well as the
opening direction, to free the obstacle it will then stop for 3 minutes and then continue moving in the
original direction after a 10 second preflashing period has elapsed.
SAFETY ERR
T B
F S
F I
CP
ERROR MOT1
T B
F S
F I
CP
ERROR ENC1
T B
F S
F I
CP
ERROR DIR1
T B
F S
F I
CP
ERR. SENS1
T B
F S
I
CP
ACT. EDGE
T B
F S
I
CP
ACT. SENS
T B
F S
I
CP
Alarm indications
AUTO PROG
T B
F S
F I
CP
OPENING
T B
F S
F I
CP
PAUSE
T B
F S
F I
CP
Pause time programming or
pause for automatic reclosing
(if activated)
Automatic programming under
way
Opening stage
Block during opening
Closing stage
Block during closing
Current sensor updating (only
during programming)
Test mode
Battery mode with a fully
charged battery
Battery mode with a
discharged battery. The motor
and commands will be
blocked.
STOP OPEN
T B
F S
F I
CP
UPDAT.SNS1
T B
F S
F I
CP
TEST
T B
F S
I
CP
BATT.
[99%]
T B
F S
I
CP
Operational indications
CLOSING
T B
F S
F I
CP
STOP CLOSE
T B
F S
F I
CP
BATT.
[0%]
T B
F S
I
CP
AUTO PROG
F
F
F
F
F
F
“PROG/OK” to set
PAUSE TIME: 30
OK
FW_0.11
5) Current sensor settings:
-
Level 1
= motor electrical input +
2
amps
-
Level 2
= motor electrical input +
2.5
amps
-
Level 3
= motor electrical input +
3
amps
-
Level 4
= motor electrical input +
4
amps
-
Level 5
= motor electrical input +
5
amps
The programmer checks the electrical input to the motor, detecting any eventual increase in effort above the normal operating limits and intervenes as an
additional safety device.
6) Setting the distance from the closing/opening travel limit:
To increase or reduce this distance modify the parameter in steps from 0 to 9 (range fro 0 to 6 cm ~). By default the appliance is set to level 4 and in this
way the gate will not slam against the travel limits but will stop within a centimetre of them.
PROGRAMMING PROCEDURE (parameter setting)
• All the functions of the electronic programmer can be set in the Display menu "
LCD1
" using the three buttons contained therein:
- use the arrows to navigate through the menu and/or to adjust the display contrast;
- use
"PROG/OK"
to modify the parameter settings and/or to confirm.
Note
:
1) The indicator light flashes slowly during opening, rapidly during closing; remains lit when
the gate is blocked but not completely closed and is off when the gate is completely closed.
2)
FI
Mode:
-
FI
also active when the gate is blocked: If the photocells are in alarm and the gate is blocked, no
movement commands will be accepted (even opening commands);
-
FI
active only during closing
In both cases activating the
FI
safety device during the closing stage will force travel direction
inversion.
3) Photocell test (
FI/FS
)
If you enable the security test you will have to connect both the transmitter and the receiver to the
controlled load output (
CTRL 24 Vdc
). When the test is enabled one second will pass between
receiving a command and carrying it out.
4)
Содержание 105/SLi824
Страница 12: ...12 NOTES ...
Страница 20: ...20 NOTES ...
Страница 28: ...28 NOTES ...
Страница 36: ...36 NOTES ...