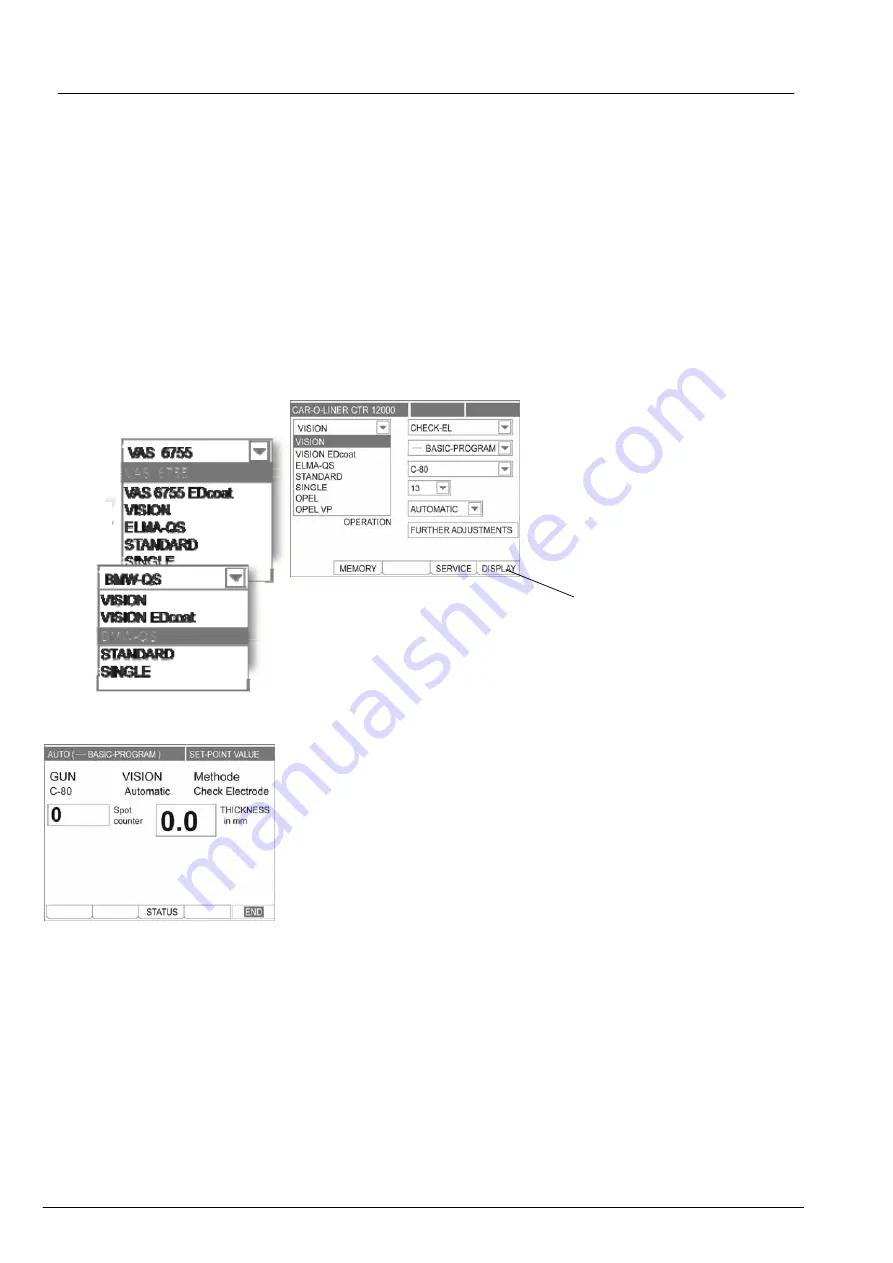
Car-O-Liner Group AB
CTR12000
10
41644, EN - rev. 2, 2012-09
2 Welding menus
2.1 General
Basic screen
Programs, selection menus and parameters are selected from and displayed
on the basic screen. Display button (F5) is used to indicate and display pro-
grams, set points and actual values.
Display screen
The example above shows the following setting:
Welding task: CHECK-EL, Welding process:VISION, welding program:
BASIC, C-gun: C 80 arm, electrode CAP: 13 mm and welding operation:
AUTOMATIC.
The integrated welding programs that are stored in the physical welding da-
tabase have write protection. They can however be used to create personal-
ized welding program (see 3.7) , while being in the EDIT mode.
Additionally, you may create personalized welding programs to be saved as
follows:
Up to 99 synergic user programs: X01 - X99
Up to 99 JOBS: J01 - J99 (see 2.10.2)
You may modify or overwrite synergic user programs (X01 - X99) as often
as you like.
Optional
program
VAS 6755.
Optional
program
BMW.
Choose with soft key F5.