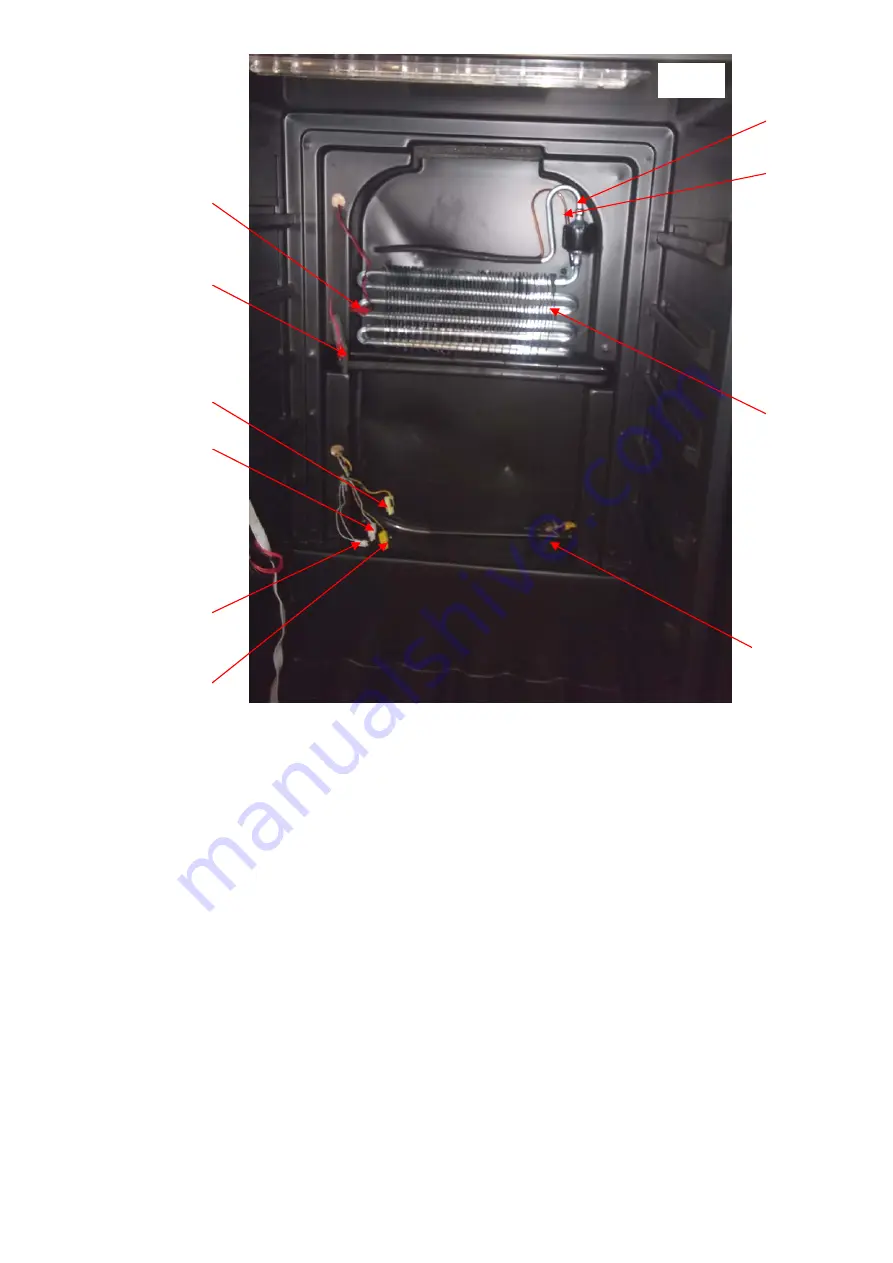
19/33
6.1.3.How to remove the evaporator
The process: Remove the shelves→Remove the control panel film→Remove the screws→
Remove the display supporter →Remove the middle electrical box→ Remove the screws
→Remove the upper and lower air-duct board.→ Remove the inner air-duct board
→ separate the evaporator from the compressor and dry filter on the joints.
You can see the evaporator is joint to suction pipe and capillary.
(Fig.7 )
Heat the joint E,G
(Fig.17 )
in the compressor room, and disconnect the pipe from compressor by using the
plier. Then remove the evaporator and capillary and suction pipe upward.
Fig.7
C
D
E
F
G
H
I
J
B
A
Содержание WC6216
Страница 1: ...WC6216 Caple 60cm in column wine cabinet Technical information ...
Страница 2: ......
Страница 5: ......
Страница 12: ...7 33 3 Cooling system diagram ...
Страница 30: ...25 33 Diagram of main PCB connection Fig 16 Fig 15 Main PCB Four barbs fixing PCB ...