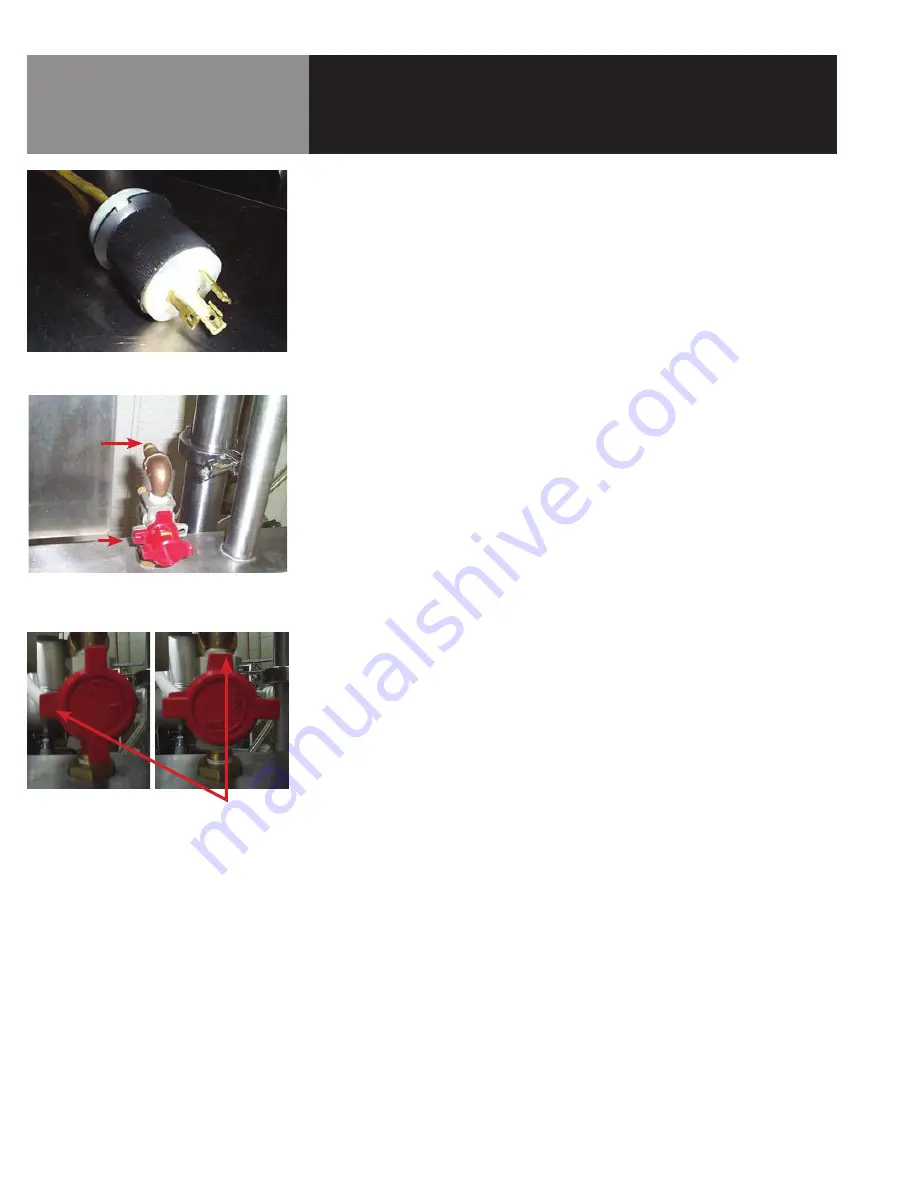
18 OM-CKPF/3
Pump Set-Up:
1. Connect the air hose on the CapKold CKPF/3 Mobile Pump/Fill Station to a compressed air
service point.
2. Connect the power cord on the Pump/Fill Station to the 208/220 Vac
GROUNDED
receptacle
on the left side pedestal on the kettle or to a 208/220 Vac, 30A
GROUNDED
receptacle on
the wall.
NOTE
: The power cord is terminated with a three-prong twist-lock plug.
3. Connect the 2-Section 3” food transfer hose to the elbow outlet on the kettle product valve
and the pump inlet elbow on the CapKold CKPF/3 Mobile Pump/Fill Station.
4. Load the Tipper Tie casing clipper magazine with clips; check the printer ink and label paper
supplies, if applicable.
5. Turn the air valve to the
UP
position, making sure that the 4-position selector switch is in
the
OFF
position.
6. Set the batch size:
• Press the
NAV
button on the control panel and select the
TOTAL
display mode.
• Press the
AMOUNT
button on the
TOTAL
display.
• The
ADD
AMOUNT
pop-up will appear. Press the + or – buttons on the pop-up to
increase or decrease the gallons per bag (or litres per sac) amount. Recommended
amount is 1.5 gallons per bag (6 litres par sac).
NOTE
: The adjustment and
measurement process compensates for differences in viscosity between batches of
different food products and ensures consistent bagging volumes.
• Test the setting by selecting the
AUTO
button on the
MODE SELECT
display and placing
a graduated measuring container below the product output valve. Depress the foot
switch once and check the amount of product dispensed into the container. Return the
product in the measuring container to the kettle.
• Make incremental adjustments on the
ADD AMOUNT
pop-up until the correct volume is
dispensed.
7. Pump warm-up: [This section allows the pump body to warm up and the rotors to expand
so the station can pump product in uniform measured quantities.]
• Select the
MANUAL
mode on the control panel.
• Set a clean, empty container under the pump valve outlet spout.
• Depress and hold the foot switch pedal until the container is almost filled with product.
[To
STOP
the pump, simply take your foot off the switch pedal.]
• Pour the contents of the container back into the kettle and repeat the filling steps as
necessary until the pump is operating smoothly.
8. Pump product into bags:
• Select the
AUTO
mode on the control panel.
• Place a flexible packaging bag over the spout of the pump outlet valve.
• Depress the foot switch once.
• Withdraw the bag from the valve spout and squeeze the air out of the upper portion
of the bag with one hand while holding the bag steady with the other. Twist the upper
portion of the bag.
• Place the upper portion of the bag into the clipper slot and gently pull toward you. (The
clipper will clip the bag and cut off the top of the bag.)
NOTE
: The bagging process
should produce a tight seal but a “loose” fill of the bag contents. This allows the
contents to move around in the bag chiller, shortening the chill time. The bag should
not be clipped near the product like a sausage casing, as this will impede the product
chilling operation.
9. Place each bag of product into a water-bath chilling device and gently tumble or agitate for
the recommended time needed for the product to reach a temperature of 40 °F (or 4 °C) or
lower.
Power Cord Plug
Air Valve
Air
Connection
Selector
Switch Knob
Operation
Indicator
Turn knob clockwise
To turn air off
Turn knob counter
clockwise to turn air on
Содержание CKPF/3
Страница 23: ...OM CKPF 3 23 Maintenance PRODUCT VALVE OPERATOR FOOT SWITCH INVERTER PUMP MOTOR ...
Страница 27: ...OM CKPF 3 27 Suggested Spare Parts List ...
Страница 28: ...28 OM CKPF 3 Suggested Spare Parts List ...
Страница 29: ...OM CKPF 3 29 Suggested Spare Parts List ...
Страница 30: ...30 OM CKPF 3 Wiring Schematic ...