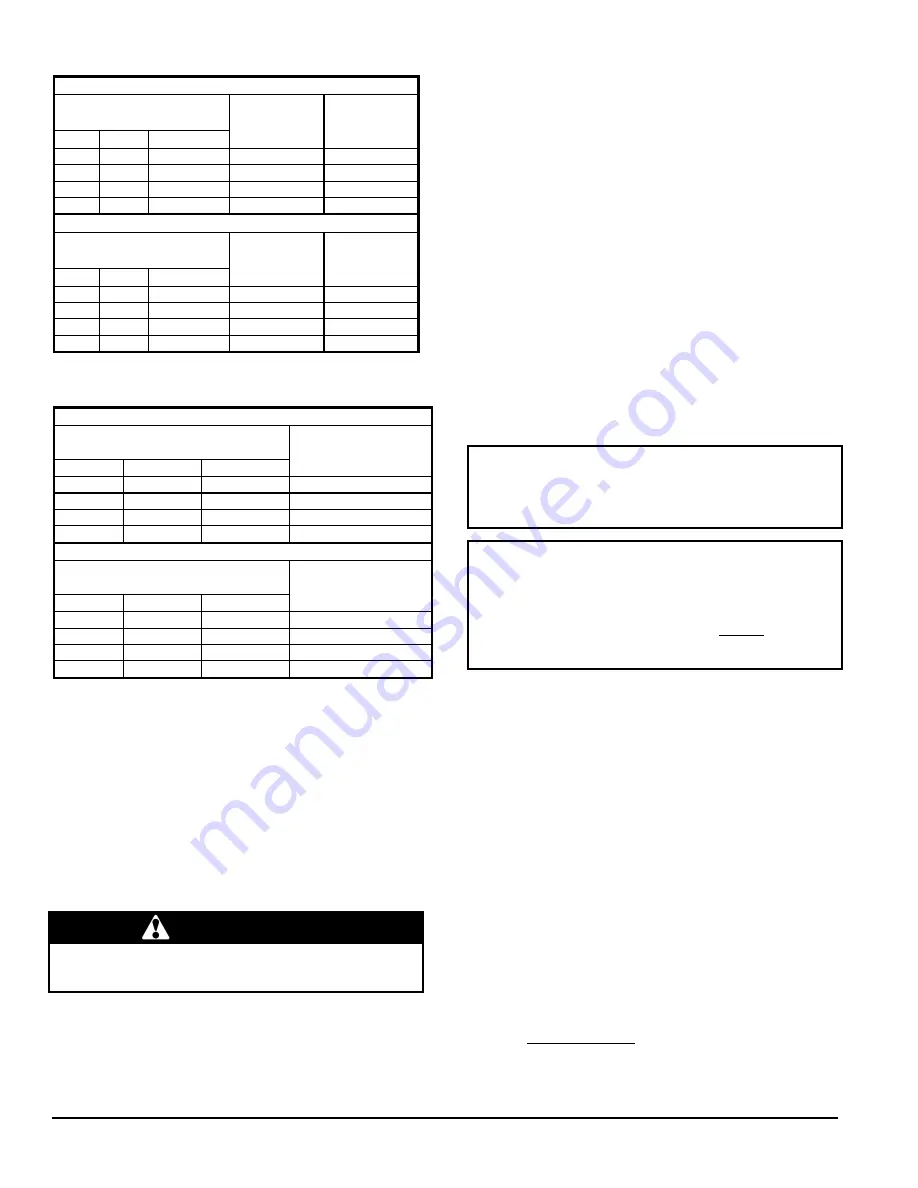
12
Table 5 : CFM adjustments, all modes
CVM 105
SW3 – ADJ (Adjustment)
DIP Switch Positions
1
2
POSITION
CFM HTG.
% increase
or decrease
CFM A/C
% increase
or decrease
OFF
OFF
A
0%
0%
ON
OFF
B
+10%
+10%
OFF
ON
C
-10%
-10%
ON
ON
D
N/A
0%
CVM 120
SW3 – ADJ (Adjustment)
DIP Switch Positions
1
2
POSITION
CFM HTG.
% increase
or decrease
CFM A/C
% increase
or decrease
OFF
OFF
A
0%
0%
ON
OFF
B
+10%
+10%
OFF
ON
C
-10%
-10%
ON
ON
D
N/A
0%
Table 6 : Delay adjustments, heating mode
CVM 105
SW4 – Delay
DIP Switch Positions
1
2
POSITION
Output
USGPH
OFF
OFF
A
0.75
ON
OFF
B
0.65
OFF
ON
C
0.50
ON
ON
D
ALL
CVM 120
SW4 – Delay
DIP Switch Positions
1
2
POSITION
Output
USGPH
OFF
OFF
A
0.85
ON
OFF
B
1.00
OFF
ON
C
1.10
ON
ON
D
N/A
5. The flame observation door and the two clean-out
access doors (located at the front of the unit) or well
closed;
6. The burner ‘’Reset’’ button is well pushed in or re-
armed;
7. The preliminary air adjustments on the burner comply
with the technical specifications in this manual;
8. The blower adjustments are appropriate and according
to the specifications in this manual;
9. The thermostat of the room is in the heating mode and
is set higher than the ambient temperature.
To start the unit, turn the main electrical switch on.
CAUTION
Do not tamper with the unit or its controls. Call a
qualified service technician.
3.3
PURGING THE OIL LINE
1. A 10-micron (or less) oil filter should be installed as
closely to the burner as possible with all oil burners, but
it is essential for burners with a low firing rate. We
recommend the use of a low pressure drop oil filter with
a capacity greater than that of the fuel pump;
2. On a new installation, the air trapped in the oil line
leading from the tank to the nozzle must be thoroughly
purged in order to prevent excessive after drip. The oil
pump is equipped with a special fitting that facilitates
the purging of any air between it and the tank. The
proper procedure for performing this operation is as
follows:
a. Place a piece of 1/4” diameter clear plastic tubing
over the purge fitting on the oil pump;
b. Start the oil burner, then open the purge fitting and
allow the burner to run until the purge tube is
completely free of air bubbles;
c.
At this point tighten the purge fitting, which will
allow the oil to run to the nozzle and fire the burner.
If the purging takes longer than 15 seconds and no
flame has been established the burner will stop.
Push the reset button on top of the Primary Control
to restart the burner.
For detailed information on the operation of the Primary
Control please refer to the instructions included with the
furnace or the burner.
3.4
COMBUSTION CHECK
IMPORTANT: The combustion check verification MUST be
performed after the nozzle replacement or the burner
cleaning. After these manipulations, the combustion
parameters are necessarily modified. Refer also to the
burner instruction manual.
IMPORTANT: The heat exchanger metal surfaces may
have oil and the baffle insulation also contains binders.
These products will burn or evaporate when the unit
operates for the first time. Because of this, the smoke
reading may be inexact during the first minutes of operation.
Therefore, the unit must operate during at least 60 minutes
before taking any readings to adjust the combustion quality.
Let the unit cool down before making any adjustments.
In order to obtain optimum performance from the oil burner,
the following set-up procedures must be followed by
referring to the Technical Specifications, Table 5 in this
manual:
1. A test kit to measure the smoke, flue draft and over-fire
pressure should be used in order to obtain the proper
air
band
setting. Although all of the above
measurements are required for optimum set up and
efficiency, the most important reading that must be
taken is the smoke number in the flue pipe, downstream
from the regulator;
2. The proper smoke number, as established by way of
engineering tests, is between 0 and 1. This degree of
smoke emission is commonly referred to as a “trace”. It
is recommended that a Bacharach True Spot Smoke
Test kit or equivalent be used;
3. Follow the next steps to do the combustion check
verification:
a. Drill a minimum proper diameter (about 9/32”) test
hole in the flue pipe, approximately 18 inches from
the furnace breech;
b. From a cold start, let the unit operate for about 5
minutes;
c.
Set the burner air setting until you have between 0
and 1 on the Bacharach Scale (or a “trace”);
Содержание CBMAAA060120
Страница 21: ...21 Figure 13 Wiring diagram CVM ...
Страница 22: ...22 Figure 14 Parts list CVMAAR036105 B50003 Rev D ...
Страница 24: ...24 Figure 15 Parts list CVMAAR060120 B50004 Rev F ...
Страница 48: ...23 Figure 13 Diagramme électrique CVM ...
Страница 49: ...24 Figure 14 Liste de pièces CVMAAR036105 B50003 Rev D ...
Страница 51: ...26 Figure 15 Liste de pièces CVMAAR060120 B50004 Rev F ...