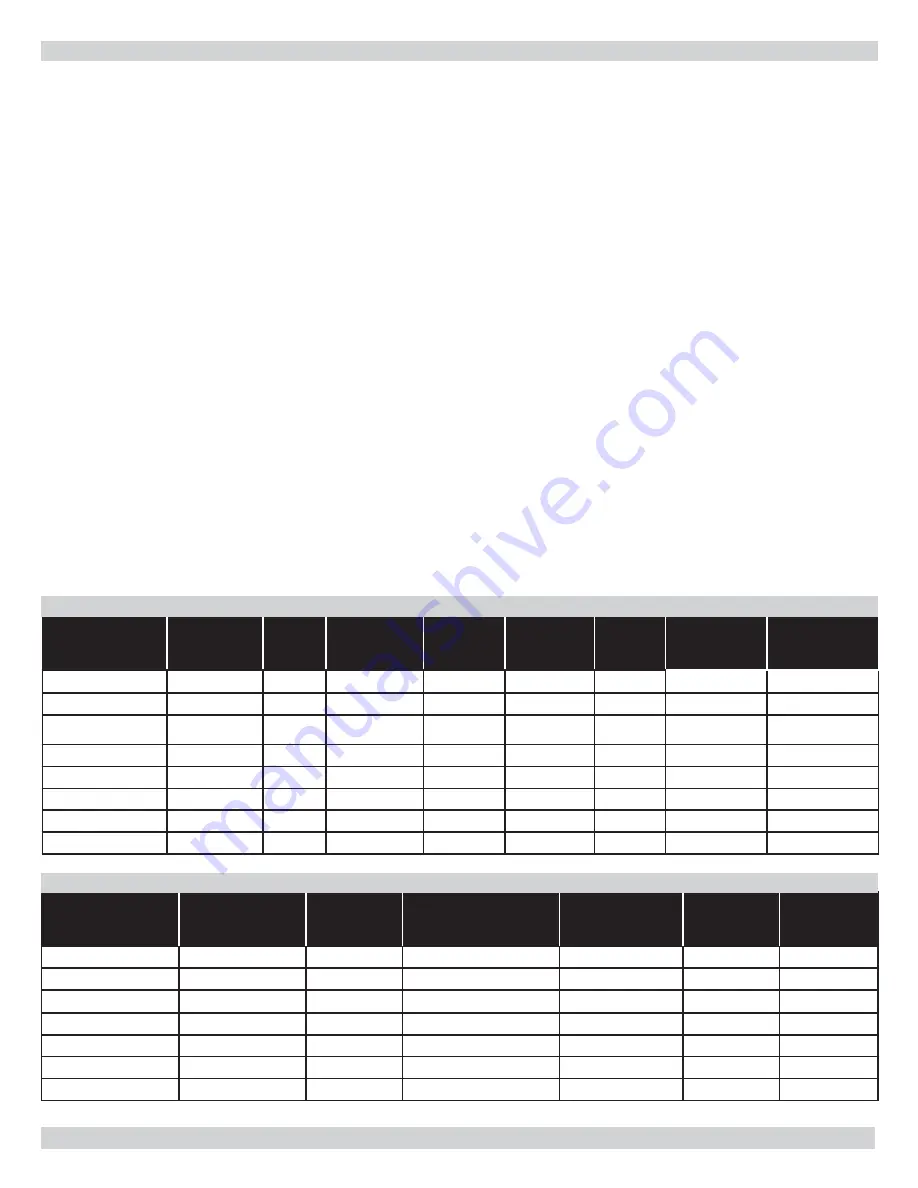
21
Final Burner Adjustments:
Final burner adjustments
must be made using combustion test instruments. Refer to
“Burner Settings”. Set burner accordingly.
• Check draft over
fi
re to verify it is between -0.01” WC
and -0.02” WC, adjust draft as necessary.
• After operating 10 minutes to warm up boiler, use
combustion test equipment to take smoke reading in
fl
ue pipe between boiler and draft regulator.
• Smoke reading should be zero to trace (Shell Bacharach
Scale).
• A new boiler requires more than 10 minutes to burn
clean due to oil
fi
lm on new heat exchanger.
• If smoke reading is zero, gradually close burner’s air
adjustment to obtain smoke reading showing trace
smoke reading. Once smoke reading is trace, measure
CO
2
and as insurance margin increase air to suf
fi
ciently
reduce CO
2
by ½% to 1%.
If clean
fi
re cannot be obtained, it is necessary to
verify burner head and electrode alignment. Proper
electrode alignment
fi
gures are presented on following pages.
If
fi
re continues to be smoky, replace nozzle with correct
replacement.
Once burner is completely adjusted, burner should be
started and stopped several times to assure good operation
with no
fl
uttering or rumbling. Verify there are no oil leaks
and record nozzle size, oil pressure, combustion readings,
and air settings on tag or label attached to burner or, boiler.
OPERATING THE BOILER
BOILER
MODEL
DELEVAN
OIL NOZZLE
INPUT
RATE
(gph)
HEAD-ADJ.
OR SETTING
LOW FIRE
BAFFLE
AIR
SHUTTER/
BAND
STATIC
PLATE
BURNER
MODEL
OIL PUMP
PRESSURE
(PSIG)
BW(4,5) BAH-91*
0.50-80º B
0.65
F0 - 1
⅛
YES
10/0
3
⅝
AFG F-HEAD
175
BW(4,5) BAH-105
0.65-70º B
0.75
F3 - 1
⅛
YES
10/0
3 ½
AFG F-HEAD
140
BW(4,5) BAH-140
0.85-70º B
1.00
F3 - 1
⅛
NO
10/2
3 ½
AFG F-HEAD
140
BW(4,5) BAH-126
0.75-80º A
0.90
F3 - 1
⅛
NO
8/0
3 ½
AFG F-HEAD
140
BW(4,5) BAH-175
1.00-80º A
1.25
F6 - 1
⅛
NO
10/0
3
⅜
AFG F-HEAD
140
BW(4,5) BAH-210
1.25-80º A
1.50
F6 - 1
⅛
NO
10/2
3
⅜
AFG F-HEAD
140
BW(4,5) BAH-168
1.00-60º B
1.20
0
NO
10/1.5
2 ¾
AFG 50 MD
140
BW(4,5) BAH-245
1.50-45º B
1.75
2
NO
10/4
2 ¾
AFG 50 MD
140
*To fi re the 3 section 91 on rate, the oil pressure must be increased to 175 psig. All Beckett oil burners for the BW boilers are factory preset at 140 psig.
BOILER
MODEL
DELEVAN
OIL NOZZLE
INPUT
RATE (gph)
TURBULATOR/AIR
SHUTTER SETTING
OIL PRESSURE
(PSIG)*
BURNER
MODEL
OIL PUMP
PRESSURE
(PSIG)
BW(4,5) RAH-91*
0.50-70° W
0.65
0.50/2.0
155
F5
155
BW(4,5) RAH-105
0.65-70° W
0.75
2.0/2.2
150
F5
150
BW(4,5) RAH-140
0.85-70° W
1.00
2.0/3.2
170
F5
150
BW(4,5) RAH-126
0.75-70° W
0.90
1.5/2.6
160
F5
150
BW(4,5) RAH-175
1.00-70° W
1.25
2.5/3.8
170
F5
170
BW(4,5) RAH-210
1.25-70° W
1.50
4.0/7.0
175
F5
175
BW(4,5) RAH-245
1.50-70° W
1.75
2.0/3.8
155
F10
155
*All Riello 40 F5 and F10 oil burner are factory preset at 145 psig.
BECKETT OIL BURNER SPECIFICATIONS
Oil Burner Maintenance
:
For Beckett AFG, and Riello
40 F5, or F10 perform following preventative maintenance
annually, preferably prior to heating season. Refer to
burner manual provided with boiler.
1.
Fuel Filter
Replace to prevent contaminated fuel from
reaching nozzle. Partially blocked fuel
fi
lter can cause
premature failure of fuel pump.
2.
Fuel Pump Unit
Replace pump screen and clean pump
unit to maintain fuel delivery to nozzle.
3.
Ignition Electrodes
Clean and adjust per
manufacturer’s recommendations, to maintain reliable
ignition of oil.
4.
Nozzle
Replace to maintain safe and reliable
combustion ef
fi
ciency. Replace with nozzle as required
in charts located in this manual.
5.
Fan and Blower Housing
Must be kept clean, free of
dirt, lint and oil to maintain proper amount of air fuel
requires to burn.
6.
Check Final Burner Adjustments.
If any component parts must be replaced, always use parts
recommended by burner manufacturer.
REILLO OIL BURNER SPECIFICATIONS
Содержание BW4BAH-91
Страница 22: ...22 OPERATING THE BOILER Figure 13 Burner Adjustments and Settings...
Страница 28: ...28 ELECTRICAL WIRING Figure 16 Honeywell L7248L Control With Beckett AFG Burner...
Страница 29: ...29 Figure 17 Honeywell L7248L Control With Riello F5 F10 Burner ELECTRICAL WIRING...
Страница 31: ...NOTES...
Страница 32: ...CAC BDP 7310 West Morris St Indianapolis IN 46231...