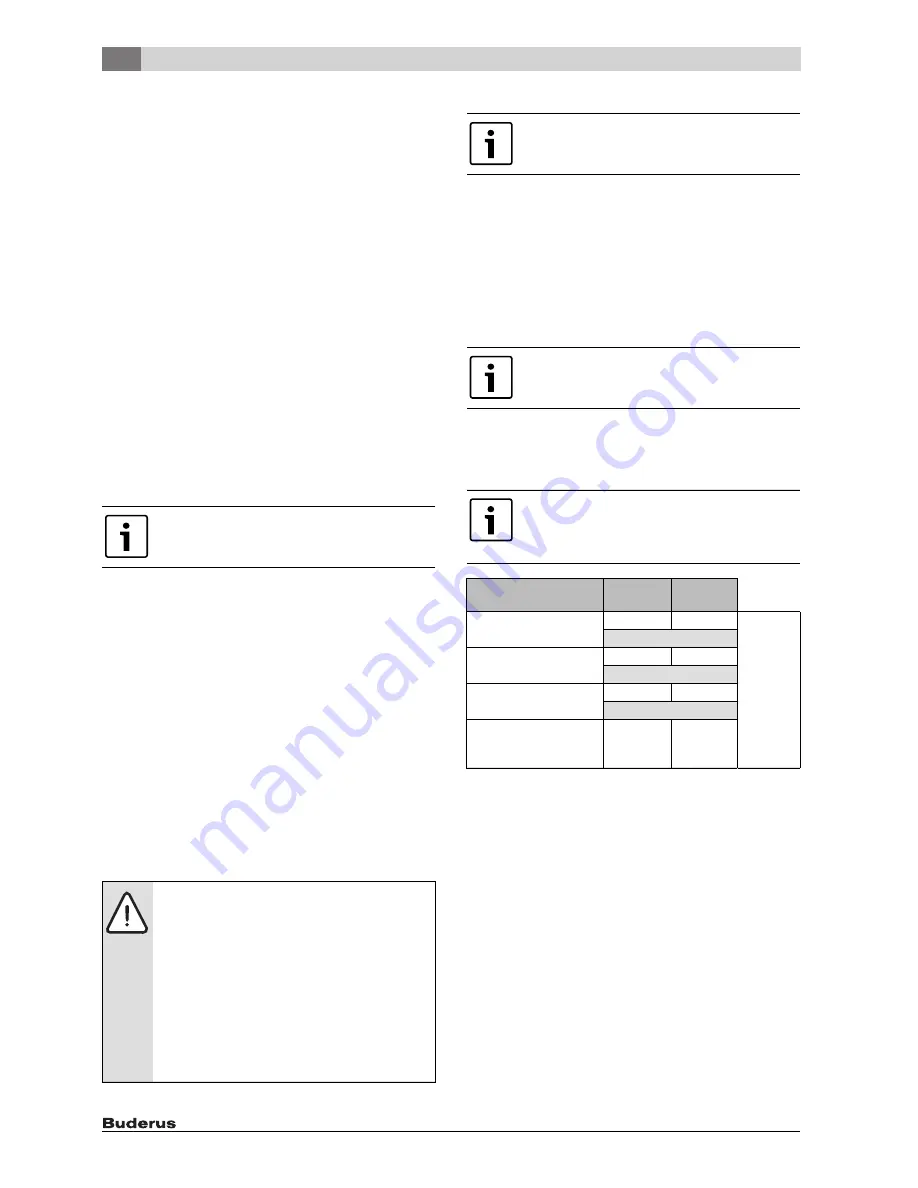
3
Information on installation and operation
Logano plus SB325 – 6 720 806 328 (2013/07)
12
3.8
Combustion air quality
▶ Keep the supply of combustion air free of corrosive substances
(e.g. halogenated hydrocarbons that contain chlorine or fluorine
compounds).
This will help prevent corrosion.
▶ Never use or store chlorinated cleaning agents or halogenated
hydrocarbons (as contained in spray cans, solvents or cleaning
agents, paints and adhesives, for example) in the boiler room.
▶ Keep the combustion air supply free of dust.
▶ If building work is taking place in the installation room and creating a
lot of dust, shut the boiler down. A burner contaminated during
building work must be cleaned before commissioning.
3.9
Heating water quality
The quality of the fill and top-up water is an essential factor for increased
efficiency, functional reliability, long service life and for maintaining the
constant operational condition of a heating system. If the system is filled
with water that has a high calcium hardness, this will be deposited on the
heat exchanger surfaces and will restrict the transfer of heat to the
heating water. As a result, the wall temperatures of the stainless steel
heat exchanger surfaces will rise and the thermal stresses (loads on the
boiler shell) will increase.
This is why the quality of the fill or top-up water must meet the conditions
stipulated in the operator's log provided and be recorded in this log.
3.10 Using antifreeze
Antifreeze based on glycol has been used in heating systems for many
years, for example Antifrogen N manufactured by Clariant.
The use of other types of antifreeze should not be a cause for concern if
the product is comparable with Antifrogen N.
Observe the antifreeze manufacturer's instructions. Follow the
manufacturer's details regarding mixing ratios.
The specific thermal capacity of Antifrogen N antifreeze is lower than the
specific thermal capacity of water. To enable the transfer of the required
heat output, increase the required flow rate accordingly. This should be
taken into account when sizing the system components (e.g. pumps)
and the pipework.
As the heat transfer medium has a higher viscosity and density than
water, take the higher pressure drop through the pipework and other
system components into account.
Check the resistance of all plastic or non-metallic components in the
system separately.
3.11 Electrical installation
3.12 Control unit settings
The purpose of optimum control unit settings is to achieve long burner
runtimes and avoid rapid temperature changes in the boiler. Gentle
temperature changes result in a longer service life of the heating system.
The control strategy of the control unit must therefore be prevented
from becoming ineffective, i.e. through the boiler water controller
switching the burner on and off.
▶ Maintain the minimum differential between the selected shutdown
temperature of the high limit safety cut-out, the temperature
controller, the maximum boiler water temperature and the maximum
temperature demand (
Tab. 10, page 12).
▶ Select set temperatures for the heating circuits that are as low as
possible.
▶ Start heating circuits (e.g. when starting up in the mornings) in
5-minute intervals.
Settings for boiler water controller and maximum boiler water
temperature
The boiler water controller is only designed to provide emergency
operation with an adjustable boiler water temperature if the control
electronics fail. In standard control mode, the function of the boiler
water controller is provided by the maximum boiler water temperature.
The maximum boiler water temperature can be selected in the control
unit in the "Boiler parameters" menu, under menu item "Max. shutdown
temperature".
Chemical additives that are not certified as harmless by
the manufacturer must not be used.
DANGER:
Risk to life and of system damage through
faulty connections.
▶ Only carry out electrical work if you are a qualified
electrician.
▶ Observe local installation regulations
(
chapter 3.1).
▶ The electrical installations must be suitable for damp
areas.
▶ The system installer must issue a wiring diagram
which records the interface between heating output
elements, burner, control unit (Logamatic) and
additional safety equipment.
We recommend using a Buderus Logamatic control unit
from the 4000 series.
The maximum boiler water temperature can be selected
on the control unit (MEC) in the "Boiler parameters"
menu, under menu item "Max. shutdown temperature".
If a control unit from the Buderus Logamatic 4000 series
is used, burner modulation in standard mode is not
enabled for 3 minutes. Never modulate upwards more
quickly than this.
Adjustable parameter
(max. temperature)
Logamatic
4321
Logamatic
4211
High limit safety cut-out
(STB)
1)
1) Set the high limit safety cut-out and temperature controller as high as possible,
but ensure the settings are at least 5 K apart.
110 °C
110 °C
at least 18 K
minimum 5 K
Temperature controller
(TR)
1)
105 °C
90 °C
minimum 6 K
Max. boiler water
temperature
99 °C
84 °C
minimum 7 K
Max. temperature
demand
2)
of HK
3)
and
DHW
4)
2) Both temperature demands must always be at least 7 K below the maximum boiler
temperature.
3) The temperature demand of heating circuits equipped with an actuator is
composed of the set flow temperature and parameter "Boiler rise" in the heating
circuit data menu.
4) The temperature demand of DHW heating is composed of the set DHW
temperature and parameter "Boiler rise" in the DHW menu.
92 °C
77 °C
Tab. 10 Adjustable parameters Logamatic 4321 and Logamatic 4211