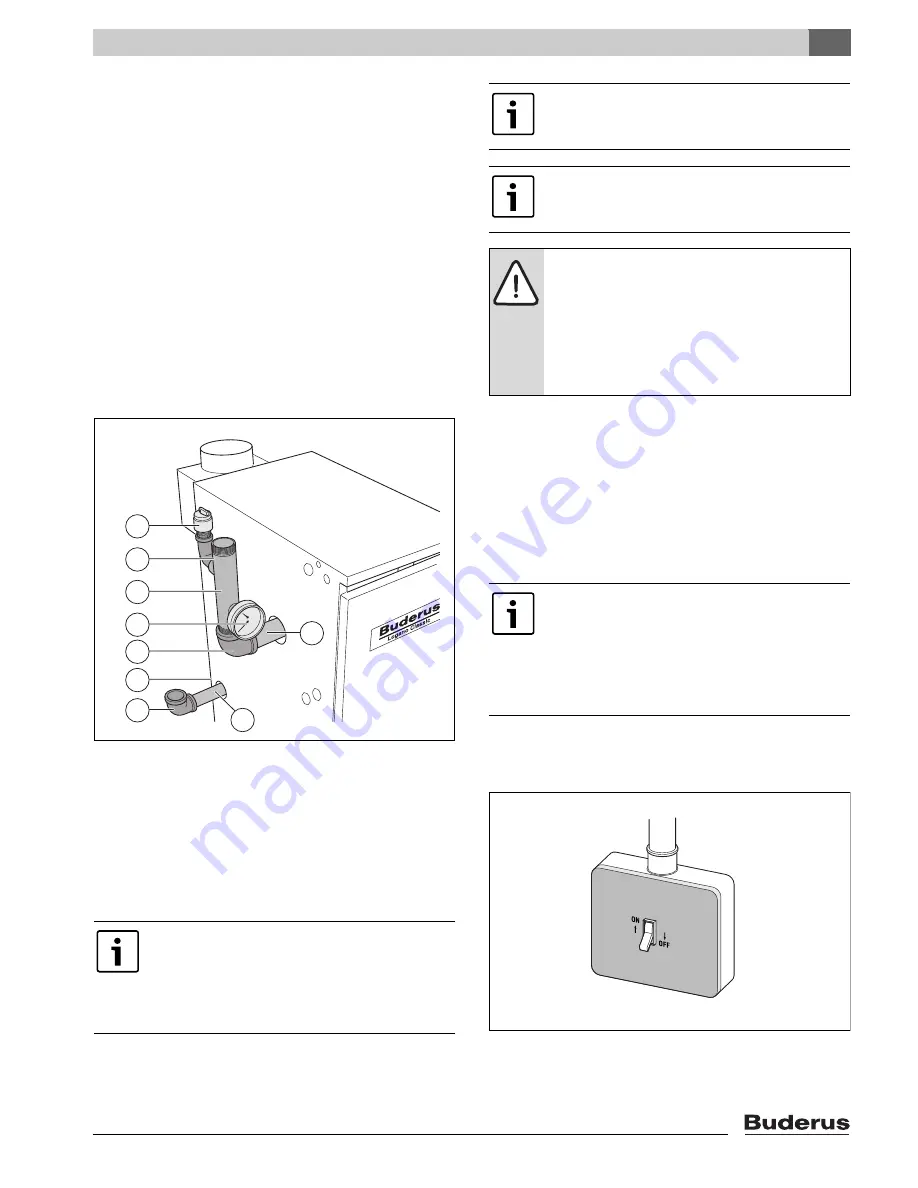
7
Boiler installation
Logano G
C
124 II – 6 720 804 440 (2012/11)
9
Installation of B-kit
The relief valve and the pressure/temperature gauge are mounted on the
boiler supply manifold which is attached to the VK (supply) connection
of the boiler (included in B-kit).
Installing boiler supply VK:
▶ Remove factory installed plastic inserts from boiler supply (VK), boiler
return (RK) and boiler drain (EL) connections.
▶ Install the 1¼"NPT nipple into boiler supply, the 1" NPT nipple into
boiler return and ¾" male NPT drain valve into boiler drain connection.
▶ Install 90° 1¼" x 1¼"NPT on 1¼" NPT supply nipple and face upward
and install 90° 1¼" x 1"NPT elbow on return nipple and face in desired
direction.
▶ Install G
C
124 1¼" x 1¼"NPT supply manifold into supply connection
(VK) of the boiler. Do NOT place on return connection of the boiler!
▶ Install first 90° ¾" street elbow in upper ¾" NPT tapping of G
C
124 1-
1/4" supply manifold and install pressure relief valve into this ¾"
tapping. Make sure to orient the discharge of the relief valve
horizontally. Install the temperature/pressure gauge in the lower 3/4"
tapping of the supply manifold.
Fig. 9
Installation of B-kit
[1]
Pressure relief valve ¾"
[2]
90° 3/4" street elbow
[3]
G
C
124 1-1/4" supply manifold
[4]
Pressure & temperature gauge
[5]
90° 1-1/4" NPT elbow
[6]
1-1/4" x 1" NPT nipple
[7]
Boiler drain ¾" NPT (backside of boiler)
[8]
90° 1-1/4" NPT elbow
[9]
1" NPT nipple
7.3
Electrical connections
The electrical connections of the boiler must be made as specified by the
local codes and the current regulations of the National Electrical
C
ode,
ANSI/NFPA–70.
The boiler must be grounded as specified by the regulations of the
relevant local authorities; otherwise follow the regulations of the
National Electrical
C
ode, ANSI/NFPA–70.
The boiler is fully functional with the factory installed aquastat and the
field installed vent damper and heating system circulation pump.
Power supply connection.
Install incoming power to the boiler per local and state codes.
▶ Install an ON/OFF switch near the boiler per local code requirements.
Fig. 10 ON/OFF switch (emergency shutoff switch)
Install the relief valve after the leak test. (
chapter 7.5,
page 11).
The relief valve must be installed in a vertical position.
The relief valve must also be installed in accordance with
the requirements of the ANSI/ASME Boiler and Pressure
Vessel
C
ode, Section IV.
1
2
3
4
5
7
8
6
VK
EL
RK
9
6 720 804 440-09.1T
We recommend installing a y-strainer (accessory) in the
boiler return connection to reduce build-up of debris on
the water side inside the boiler.
Ensure compliance with all state and local regulations
pertaining to the installation of boiler systems.
WARNING:
Fire danger due to exposure to hot water
pipes.
▶ Maintain a minimum clearance of two inches between
non-insulated pipes carrying hot water and
combustible walls and surfaces in the boiler room.
A minimum of 1" high quality pipe insulation is
required to permit direct contact with combustible
surfaces.
When making the electrical connections please observe
the following guidelines:
▶ Perform only electrical work, if you possess the
required certification for such work. When you do not
have the required certification, have the electrical
work performed by a certified electrician.
▶ Observe all local and state installation regulations.
6 720 804 440-10.1T
Содержание Logano GC 124 II
Страница 32: ......