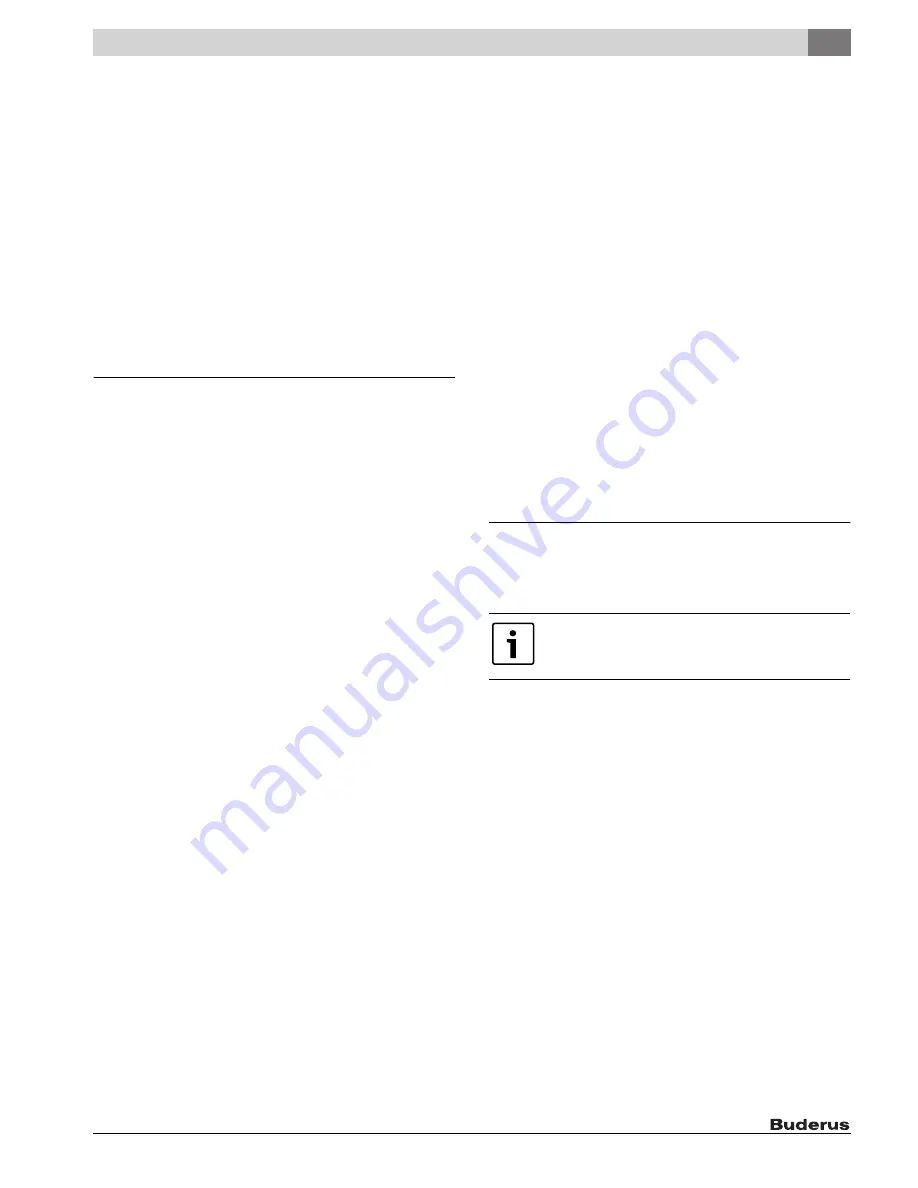
9
Requirements for connection to chimneys or venting systems
Logano GC 144 II – 6 720 808 893 (2017/02)
13
(crawl space or attic). The shortest dimension of all inlet and outlet
openings must not be less than three inches.
▶ If there is a direct connection to the outside, each opening must have
a minimum cross-section of one square inch per 4000 Btu/h of the
total combustion output of all gas-fired appliances inside the closed
room.
▶ If there is a connection to the outside through vertical ventilation
ducts, each opening must have a minimum cross-section of one
square inch per 4000 Btu/h of the total combustion output of all gas-
fired appliances inside the closed room.
▶ If there is a connection to the outside through horizontal ventilation
ducts, each opening must have a minimum cross-section of one
square inch per 2000 Btu/h of the total combustion output of all gas-
fired appliances inside the closed room.
▶ If the openings are connected to ventilation ducts, the ducts must
have the same cross-section area as the openings.
9
Requirements for connection to chimneys
or venting systems
The flue connection must comply with the regulations of the National
Fuel Gas Code, Part 7, Venting of Equipment, and the local construction
codes.
Flue connections of heating systems with natural venting must not be
connected with any component of a mechanically operated venting
system that operates with overpressure.
The cross-section of the flue connection must not be less than that
specified (
If the boiler is to be connected to a brick chimney, the chnimney must be
thoroughly inspected before use. The chimney must be clean, in
compliance with construction codes and of sufficient dimensions.
Chimneys with an internal liner are preferred and are only permitted if
the liner complies with all national, state and local construction codes.
Liners of fire-glazed brick with moisture-proof joints and liners of
corrosion-resistant material are recommended. Contact the local gas
supply company for advice and recommendations for flue connection
and chimney liners. A flue pipe of single-walled sheet metal is required
for flue connections for type II models.
An adequate chimney height in compliance with the tables of the
National Fuel Gas Code, ANSI Z 223.1, is required.
Separation of a boiler from a common flue system
If an existing boiler is separated from a common venting system, the
venting system will then be too large to guarantee correct venting for the
heating systems that remain connected to the system.
Test the venting system by the following procedure:
Carry out these steps with every heating system that remains connected
to the venting system when the boiler is separated from a common
venting system. Every heating system must be started in operation and
the other heating systems must remain turned off.
▶ All unused openings of the common system must be sealed.
▶ Inspect the venting system to ensure that it has the correct
dimensions and longitudinal inclination. Make sure that the system is
not blocked, leaking, corroded or has any other faults that cause it to
operate improperly.
▶ If necessary, close all doors and windows in the building and all doors
between the space in which the heating systems that remain
connected to the venting system are installed and the other rooms of
the building. Turn off washing machines and dryers and all
appliances that are not connected to the venting system. Run all
venting fans and bathroom exhaust fans at maximum speed. Fans in
use in summer must remain in operation and oven exhaust system
flaps must be closed.
▶ Now start the heating system that is to be tested. Follow the
instructions for starting. Set the thermostat for continuous
operation.
▶ After the main gas burner has been operating for five minutes, check
the opening at the back flow check for drafts with a match flame or a
candle, or with the smoke of a cigarette, cigar or pipe.
▶ Then all heating systems that remain connected to the venting
system have been checked as above to ensure that the venting
operates properly, return all doors, windows, exhaust fans, oven
exhaust flaps and all other gas-fired appliances to their original
position.
▶ Any incorrect status of the common venting system must be
corrected to ensure that the heating system complies with the
regulations of the National Fuel Gas Code, ANSI Z 223.1. If the size of
any component of the common venting system is changed, the
complete venting system must be resized to comply with the relevant
tables in Part 11 of the National Fuel Gas Code, ANSI Z 223.1.
10
Flue pipe installation
This section describes the connection of the flue pipe and venting
system. Note that the open draft hood cannot be modified under any
circumstances.
▶ The flue collar is factory installed on the flue connection of the open
draft hood and fastened with four (4) corrosion-resistant sheet metal
screws.
The vent damper supplied with the boiler must be used for venting the
boiler only.
The position of the vent damper position blade must be visible.
The open draft hood must be at least six inches from all combustible
surfaces.
The vent damper must be freely accessible for maintenance.
The vent damper must be open when the main burner of the boiler is
operating.
Installation of vent damper
▶ Install pins in the hole of the vent damper blade for the II models only.
▶ Fasten vent damper to the flue collar of the open draft hood with
three (3) corrosion-resistant sheet metal screws.
Connecting flue pipe
▶ Connect flue pipe to the chimney with the shortest possible length of
flue pipe.
Use only flue pipes with the proper diameter for the boiler.
Every horizontal section of the flue pipe must have a minimum rise of 1/
4 inch per foot towards the chimney. The flue pipe must be securely
The boiler can and may only be operated with the
electrical vent damper that is standard supplied with
every GC 144 II.
Содержание GC144/3
Страница 32: ......