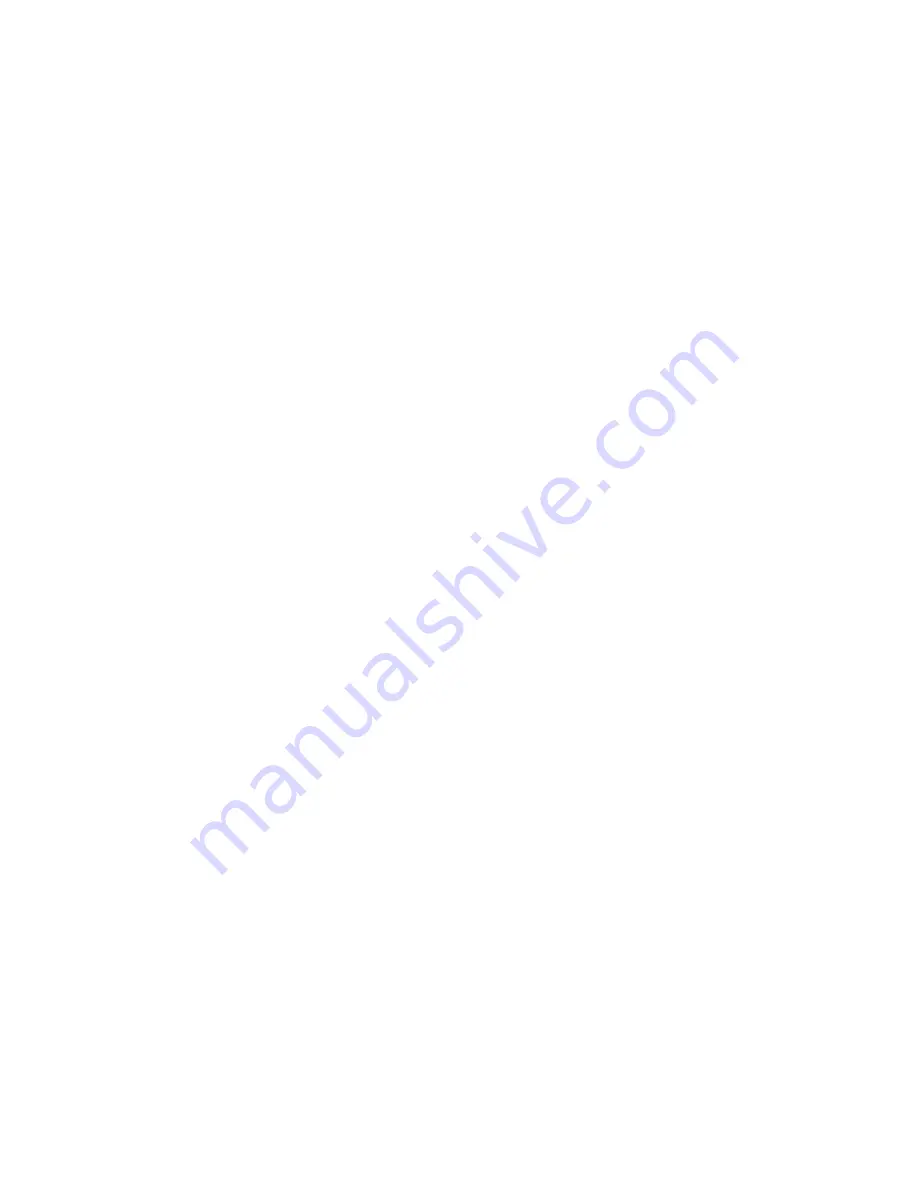
61
f. Fin stock coating shall pass 2000 hours of the
following: one week exposure in the prohesion
chamber followed by one week of accelerated
ultraviolet light testing. Prohesion chamber: the
solution shall contain 3.5% sodium chloride and
0.35% ammonium sulfate. The exposure cycle
is one hour of salt fog application at ambient
followed by one hour drying at 95°F (35°C).
3. Optional Copper-fin evaporator and condenser
coils:
a. Shall be constructed of copper fins mechani-
cally bonded to copper tubes and copper tube
sheets.
b. Galvanized steel tube sheets shall not be accept-
able.
c. A polymer strip shall prevent coil assembly
from contacting the sheet metal coil pan to min-
imize potential for galvanic corrosion between
coil and pan.
4. Optional E-coated aluminum-fin evaporator and
condenser coils:
a. Shall have a flexible epoxy polymer coating
uniformly applied to all coil surface areas with-
out material bridging between fins.
b. Coating process shall ensure complete coil
encapsulation of tubes, fins and headers.
c. Color shall be high gloss black with gloss per
ASTM D523-89.
d. Uniform dry film thickness from 0.8 to 1.2 mil
on all surface areas including fin edges.
e. Superior hardness characteristics of 2H per
ASTM D3363-92A and cross-hatch adhesion of
4B-5B per ASTM D3359-93.
f. Impact resistance shall be up to 160 in.-lb
(ASTM D2794-93).
g. Humidity and water immersion resistance shall
be up to minimum 1000 and 250 hours respec-
tively (ASTM D224-92 and ASTM D870-92).
h. Corrosion durability shall be confirmed through
testing to be no less than 6000 hours salt spray
per ASTM B117-90.
J. (23 81 19.13.J) Refrigerant components
1. Refrigerant circuit shall include the following con-
trol, safety, and maintenance features:
a. Thermostatic Expansion Valve (TXV) shall
help provide optimum performance across the
entire operating range. Shall contain removable
power element to allow change out of power
element and bulb without removing the valve
body.
b. Refrigerant filter drier - solid core design.
c. Service gauge connections on suction and dis-
charge lines.
d. Pressure gauge access through a specially
designed access screen on the side of the unit.
2. Compressors
a. Unit shall use fully hermetic, scroll compressor
for each independent refrigeration circuit.
b. Models shall be available with 2 compressor/2-
stage cooling.
c. Compressor motors shall be cooled by refriger-
ant gas passing through motor windings.
d. Compressors shall be internally protected from
high discharge temperature conditions.
e. Compressors shall be protected from an over-
temperature and over-amperage conditions by
an internal, motor overload device.
f. Compressor shall be factory mounted on rubber
grommets.
g. Compressor motors shall have internal line
break thermal, current overload and high pres-
sure differential protection.
h. Crankcase heaters shall not be required for nor-
mal operating range, unless provided by the fac-
tory.
K. (23 81 19.13.K) Filter section
1. Filters access is specified in the unit cabinet section
of this specification.
2. Filters shall be held in place by a preformed slide
out filter tray, facilitating easy removal and instal-
lation.
3. Shall consist of factory-installed, low velocity,
throw-away 2-in. thick fiberglass filters.
4. Filters shall be standard, commercially available
sizes.
5. Only one size filter per unit is allowed.
6. 4-in. filter capability is possible with a field-
installed pre-engineered slide out filter track acces-
sory. 4-in. filters are field furnished.
L. (23 81 19.13.L) Evaporator fan and motor
1. Evaporator fan motor:
a. Shall have inherent automatic-reset thermal
overload protection or circuit breaker.
b. Shall have a maximum continuous bhp rating
for continuous duty operation; no safety factors
above that rating shall be required.
2. Belt-driven evaporator fan:
a. Belt drive shall include an adjustable-pitch motor
pulley and belt break protection system.
b. Shall use rigid pillow block bearing system with
lubricate fittings at are accessible or lubrication
line.
c. Blower fan shall be double-inlet type with for-
ward-curved blades.
d. Shall be constructed from steel with a corrosion
resistant finish and dynamically balanced.
M. (23 81 19.13.M) Condenser Fans and Motors
1. Condenser fan motors:
a. Shall be a totally enclosed motor.
b. Shall use permanently lubricated bearings.
Содержание Preferred Series
Страница 16: ...16 581J 17 BASE UNIT DIMENSIONS DIMENSIONS ...
Страница 17: ...17 581J 17 BASE UNIT DIMENSIONS cont ...
Страница 18: ...18 581J 17 CORNER WEIGHTS DIMENSIONS cont ...
Страница 20: ...20 DIMENSIONS cont 581J 20 24 BASE UNIT DIMENSIONS ...
Страница 21: ...21 581J 20 24 BASE UNIT DIMENSIONS cont ...
Страница 22: ...22 581J 20 24 CORNER WEIGHTS DIMENSIONS cont ...
Страница 24: ...24 581J 28 BASE UNIT DIMENSIONS DIMENSIONS cont ...
Страница 25: ...25 581J 28 BASE UNIT DIMENSIONS cont ...
Страница 26: ...26 581J 28 CORNER WEIGHTS DIMENSIONS cont ...
Страница 28: ...28 581J 17 ROOF CURB DIMENSIONS ACCESSORY DIMENSIONS ...
Страница 29: ...29 581J 20 24 ROOF CURB DIMENSIONS ...
Страница 30: ...30 581J 28 ROOF CURB DIMENSIONS ACCESSORY DIMENSIONS cont ...
Страница 46: ...46 581J 17 24 ELECTRO MECHANICAL CONTROL WIRING DIAGRAMS TYPICALWIRING DIAGRAM ...
Страница 47: ...47 581J 17 24 ELECTRO MECHANICAL CONTROL WIRING DIAGRAM WITH OPTIONAL PERFECT HUMIDITY SYSTEM ...
Страница 48: ...48 581J 17 24 TYPICAL POWER WIRING DIAGRAM 208 230V SHOWN TYPICALWIRING DIAGRAM cont ...
Страница 49: ...49 581J 17 24 TYPICAL POWER WIRING DIAGRAM WITH OPTIONAL PERFECT HUMIDITY SYSTEM 208 230V SHOWN ...
Страница 67: ......