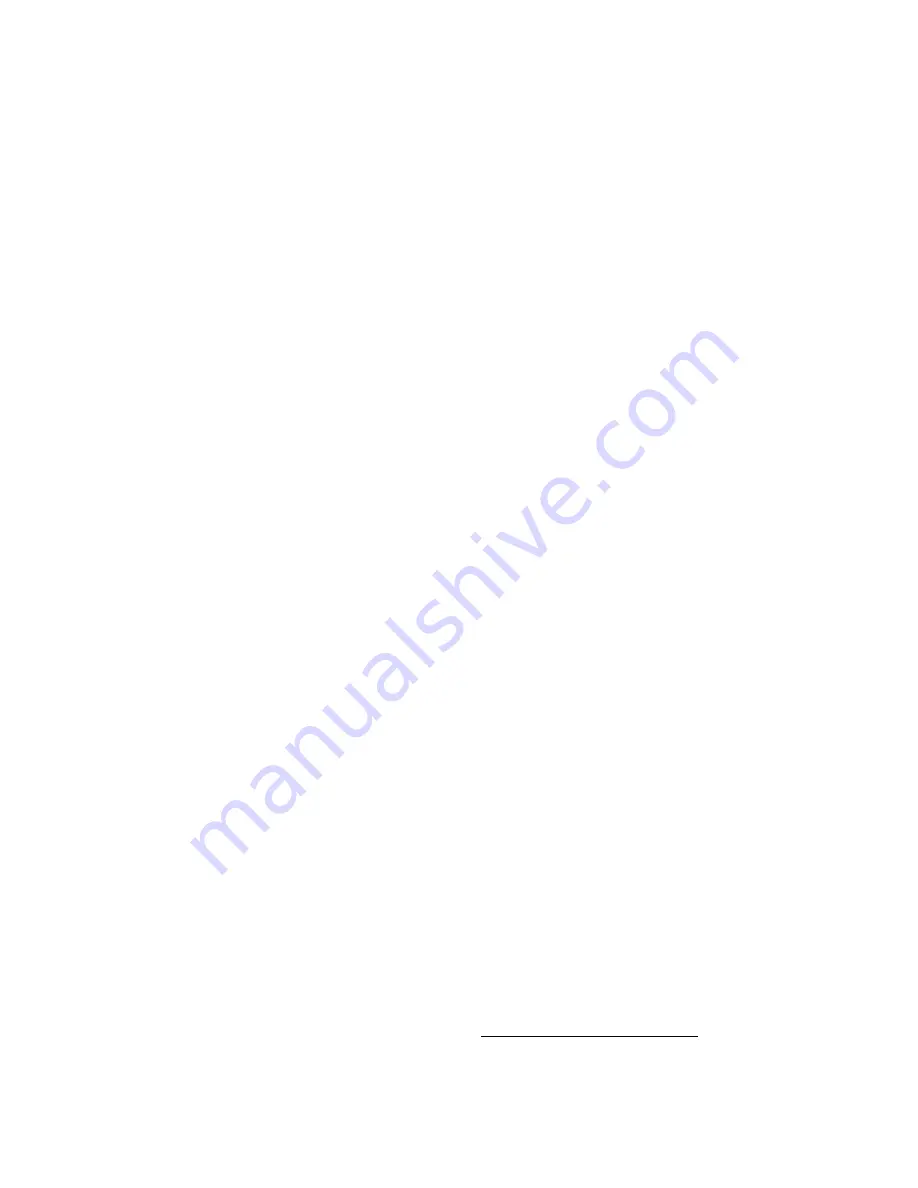
58
3. Shall include a central control terminal board to
conveniently and safely provide connection points
for vital control functions such as: smoke detectors,
phase monitor, economizer, thermostat, DDC con-
trol options, loss of charge, freeze switch, high
pressure switches.
4. The heat exchanger shall be controlled by an inte-
grated gas controller (IGC) microprocessor. See
heat exchanger section of this specification.
5. Unit shall include a minimum of one 8-pin screw
terminal connection board for connection of con-
trol wiring.
B. (23 09 33.23.B) Safeties:
1. Compressor over-temperature, over-current.
2. Low-pressure switch.
a. Units with 2 compressors shall have different
sized connectors for the circuit 1 and circuit 2
loss of charge switches. They shall physically
prevent the cross-wiring of the safety switches
between circuits 1 and 2.
b. Loss of charge switch shall use different color
wire than the high pressure switch. The purpose
is to assist the installer and service technician to
correctly wire and/or troubleshoot the rooftop
unit.
3. High-pressure switch.
a. Units with 2 compressors shall have different
sized connectors for the circuit 1 and circuit 2
high pressure switches. They shall physically
prevent the cross-wiring of the safety switches
between circuits 1 and 2.
b. High-pressure switch shall use different color
wire than the low-pressure switch. The purpose
is to assist the installer and service technician to
correctly wire and/or troubleshoot the rooftop
unit.
4. Automatic reset, motor thermal overload protector.
5. Heating section shall be provided with the follow-
ing minimum protections.
a. High-temperature limit switches.
b. Induced draft motor speed sensor.
c. Flame rollout switch.
d. Flame proving controls.
Part 6 — (23 09 93) Sequence of operations for HVAC con-
trols
6.01
(23 09 93.13) Decentralized, Rooftop Units:
(23 09 93.13.A) INSERT SEQUENCE OF
OPERATION
Part 7 — (23 40 13) Panel air filters
7.01
(23 40 13 13) Decentralized rooftop units:
A. (23 40 13 13.A) Standard filter section
1. Shall consist of factory-installed, low velocity,
throwaway 2-in. thick fiberglass filters of commer-
cially available sizes.
2. Unit shall use only one filter size. Multiple sizes
are not acceptable.
3. Filters shall be accessible through a dedicated,
weather tight access panel.
4. 4-in. filter capabilities shall be capable with pre-
engineered and approved Bryant filter track field-
installed accessory. This kit requires field furnished
filters.
Part 8 — (23 81 19) Self-contained air conditioners
8.01
(23 81 19.13) Medium-Capacity Self-Contained Air
Conditioners (581J*17-28)
A. (23 81 19.13.A) General
1. Outdoor, rooftop mounted, electrically controlled,
heating and cooling unit utilizing hermetic scroll
compressor(s) for cooling duty and gas combustion
for heating duty.
2. Factory assembled, single piece heating and cool-
ing rooftop unit. Contained within the unit enclo-
sure shall be all factory wiring, piping, controls,
and special features required prior to field start-up.
3. Unit shall use Puron
®
R-410A refrigerant.
4. Unit shall be installed in accordance with the
manufacturer’s instructions.
5. Unit must be selected and installed in compliance
with local, state, and federal codes.
B. (23 81 19.13.B.) Quality Assurance
1. Unit meets ASHRAE 90.1-2016 and IECC
1
-2015
minimum efficiency requirements.
2. Units are ENERGY STAR
2
certified where sizes
are required.
3. Unit shall be rated in accordance with AHRI Stan-
dard 340/360.
4. Unit shall be designed to conform to ASHRAE 15.
5. Unit shall be ETL-tested and certified in accor-
dance with ANSI Z21.47 Standards and ETL-listed
and certified under Canadian standards as a total
package for safety requirements.
6. Insulation and adhesive shall meet NFPA 90A
requirements for flame spread and smoke genera-
tion.
7. Unit internal insulation linings shall be resistant to
mold growth in accordance with “mold growth and
humidity” test in ASTM C1338, G21, and UL 181
or comparable test method. Air stream surfaces
shall be evaluated in accordance with the “Erosion
Test” in UL 181, as part of ASTM C1071.
8. Unit casing shall be capable of withstanding 500-
hour salt spray exposure per ASTM B117 (scribed
specimen).
9. Roof curb shall be designed to conform to NRCA
Standards.
10. Unit shall be subjected to a completely automated
run test on the assembly line. The data for each unit
1. IECC is a registered trademark of the International Code Coun-
cil, Inc.
2. Energy Star is registered trademark of the United States
Department of Energy.
GUIDE SPECIFICATIONS (cont)
Содержание Preferred Series
Страница 16: ...16 581J 17 BASE UNIT DIMENSIONS DIMENSIONS ...
Страница 17: ...17 581J 17 BASE UNIT DIMENSIONS cont ...
Страница 18: ...18 581J 17 CORNER WEIGHTS DIMENSIONS cont ...
Страница 20: ...20 DIMENSIONS cont 581J 20 24 BASE UNIT DIMENSIONS ...
Страница 21: ...21 581J 20 24 BASE UNIT DIMENSIONS cont ...
Страница 22: ...22 581J 20 24 CORNER WEIGHTS DIMENSIONS cont ...
Страница 24: ...24 581J 28 BASE UNIT DIMENSIONS DIMENSIONS cont ...
Страница 25: ...25 581J 28 BASE UNIT DIMENSIONS cont ...
Страница 26: ...26 581J 28 CORNER WEIGHTS DIMENSIONS cont ...
Страница 28: ...28 581J 17 ROOF CURB DIMENSIONS ACCESSORY DIMENSIONS ...
Страница 29: ...29 581J 20 24 ROOF CURB DIMENSIONS ...
Страница 30: ...30 581J 28 ROOF CURB DIMENSIONS ACCESSORY DIMENSIONS cont ...
Страница 46: ...46 581J 17 24 ELECTRO MECHANICAL CONTROL WIRING DIAGRAMS TYPICALWIRING DIAGRAM ...
Страница 47: ...47 581J 17 24 ELECTRO MECHANICAL CONTROL WIRING DIAGRAM WITH OPTIONAL PERFECT HUMIDITY SYSTEM ...
Страница 48: ...48 581J 17 24 TYPICAL POWER WIRING DIAGRAM 208 230V SHOWN TYPICALWIRING DIAGRAM cont ...
Страница 49: ...49 581J 17 24 TYPICAL POWER WIRING DIAGRAM WITH OPTIONAL PERFECT HUMIDITY SYSTEM 208 230V SHOWN ...
Страница 67: ......