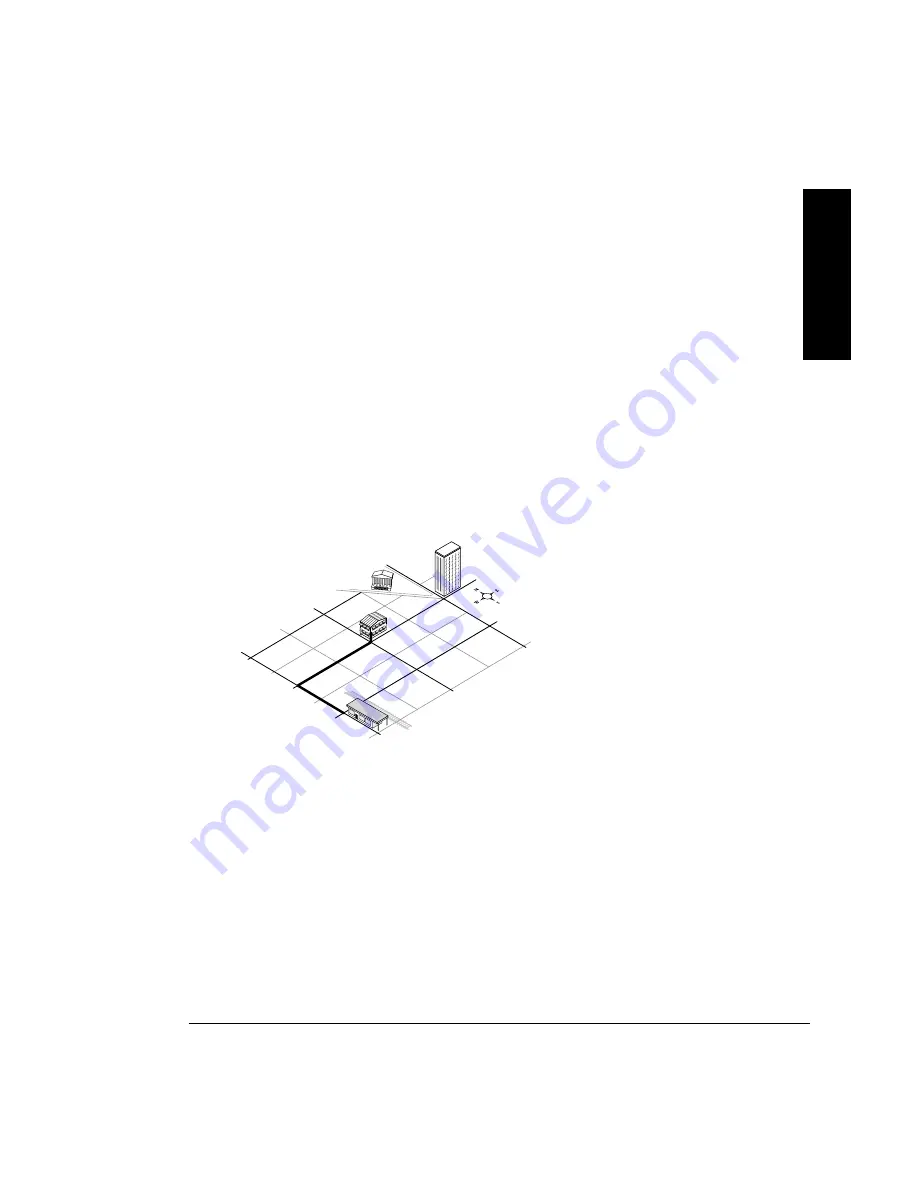
Introduction to CMM
Global User Manual
10-9
Intro. to CMM
An Explanation of Datum
A datum is a location. We use datum’s as guides to tell others
where we are or as directions on how to get to places. On the
map shown the Ritz Hotel is a datum. So are streets, the train
station, the museum, and the restaurant. Thus, by using an
origin, datum’s, directions and distances people have all the
information they need to get from one location to another.
For example, to get from the train station (origin) to the restau-
rant, you walk 2 blocks north on Elm Street (datum), take a
right, and walk 2 blocks east on Maple (datum).
Figure 14
Map Datums
Ma
ple
A
1
2
3
4
5
B
C
D
E
Birc
h
Ch
es
tnu
t
Sycamore
Elm
Oak
Ritz Hotel (Datum)
Restaurant (Datum)
Train Station (Datum)
Museum (Datum)
Figure 6
Содержание Global 121510
Страница 2: ......
Страница 6: ......
Страница 8: ......
Страница 16: ...Global General Information Global User Manual 1 10 Floor Plan Global 9XX8 Front View ...
Страница 18: ......
Страница 31: ...System Set Up Global User Manual 2 15 System Set Up Alignment Dots ...
Страница 34: ......
Страница 36: ......
Страница 38: ......
Страница 40: ......
Страница 48: ......
Страница 50: ......
Страница 62: ......
Страница 64: ......
Страница 73: ...System Options Global User Manual 6 11 System Options ...
Страница 76: ......
Страница 78: ......
Страница 83: ...Global Controls Global User Manual 7 7 Controls GC 1 Global Controller and Workstation GC 1 ...
Страница 94: ......
Страница 102: ......
Страница 108: ......
Страница 137: ...Introduction to CMM Global User Manual 10 31 Intro to CMM ...
Страница 138: ......
Страница 144: ......