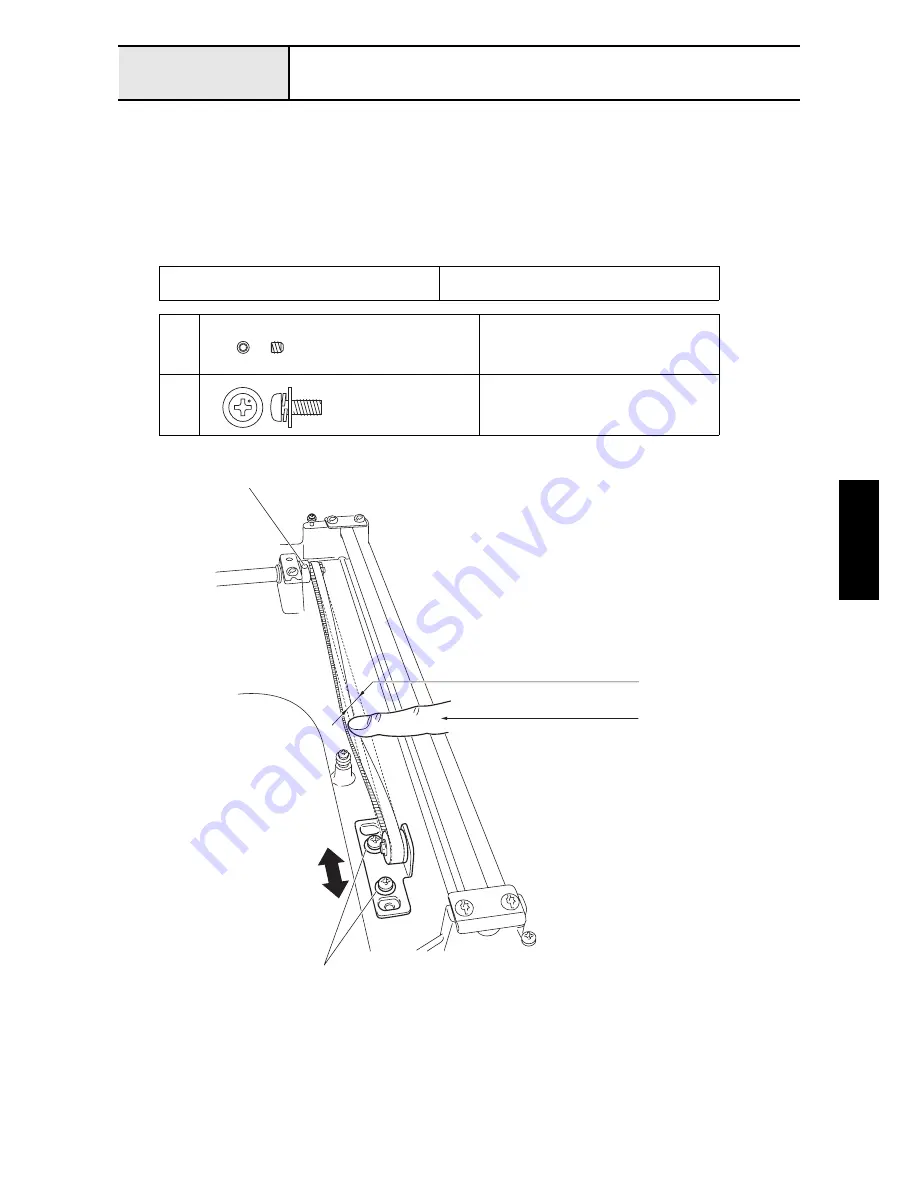
4 - 31
In
spection and
Adjustment
Adjustment
Y-belt tension adjustment
1. Loosen the 2 screws
1
.
2. Loosen the 2 screws
2
.
3. Move the Y tension plate assembly back and forth to adjust the Y-belt tension.
4. Tighten the 2 screws
2
.
5. Repeat the same steps to adjust the Y-belt tension on the right side.
6. Tighten the 2 screws
1
.
Load when the center of the Y-belt is deflected
4.3 mm
2.35 - 2.55 N (240 - 260g)
1
Torque
0.78 - 1.18 N-m
2
Torque
1.18 - 1.57 N-m
Set Screw, Socket (CP)
M3X3
Color; Black
Screw, Pan (S/P washer)
M
4X10DB
3.9mm
2.35 - 2.55N (240 - 260g)
2
1
Содержание PR-600II
Страница 1: ......
Страница 2: ......
Страница 20: ...2 2 Main parts Main unit ...
Страница 33: ...2 15 Disassembly Feed unit Main unit ...
Страница 44: ...2 26 Needle thread unit Main unit ...
Страница 47: ...2 29 Disassembly Needle bar change unit Main unit ...
Страница 50: ...2 32 Thread wiper unit Main unit ...
Страница 54: ...2 36 Needle bar unit Main unit ...
Страница 60: ...2 42 Upper shaft unit Main unit ...
Страница 70: ...2 52 Lower shaft unit Main unit ...
Страница 73: ...2 55 Disassembly Power unit Main unit ...
Страница 78: ...2 60 Thread cut unit Main unit ...
Страница 82: ...2 64 Thread tension unit Main unit ...
Страница 91: ...2 73 Disassembly Operation panel Main unit ...
Страница 98: ...2 80 ...
Страница 100: ...3 2 Operation panel Main unit ...
Страница 108: ...3 10 Thread tension unit Main unit ...
Страница 118: ...3 20 Thread cut unit Main unit ...
Страница 122: ...3 24 Power unit Main unit ...
Страница 128: ...3 30 Lower shaft unit Main unit ...
Страница 132: ...3 34 Upper shaft unit Main unit ...
Страница 147: ...3 49 Assembly Needle bar unit Main unit ...
Страница 157: ...3 59 Assembly Thread wiper unit Main unit ...
Страница 162: ...3 64 Needle bar change unit Main unit ...
Страница 166: ...3 68 Needle thread unit Main unit ...
Страница 170: ...3 72 Feed unit Main unit ...
Страница 188: ...3 90 Main unit Main unit ...
Страница 206: ...4 4 Inspection Blunt needle 1 Touch the needle tip with your finger to check that the needle tip is not blunt ...
Страница 244: ...4 4 Inspection Blunt needle 1 Touch the needle tip with your finger to check that the needle tip is not blunt ...
Страница 282: ...4 42 ...
Страница 311: ...6 1 6Maintenance ...
Страница 333: ......