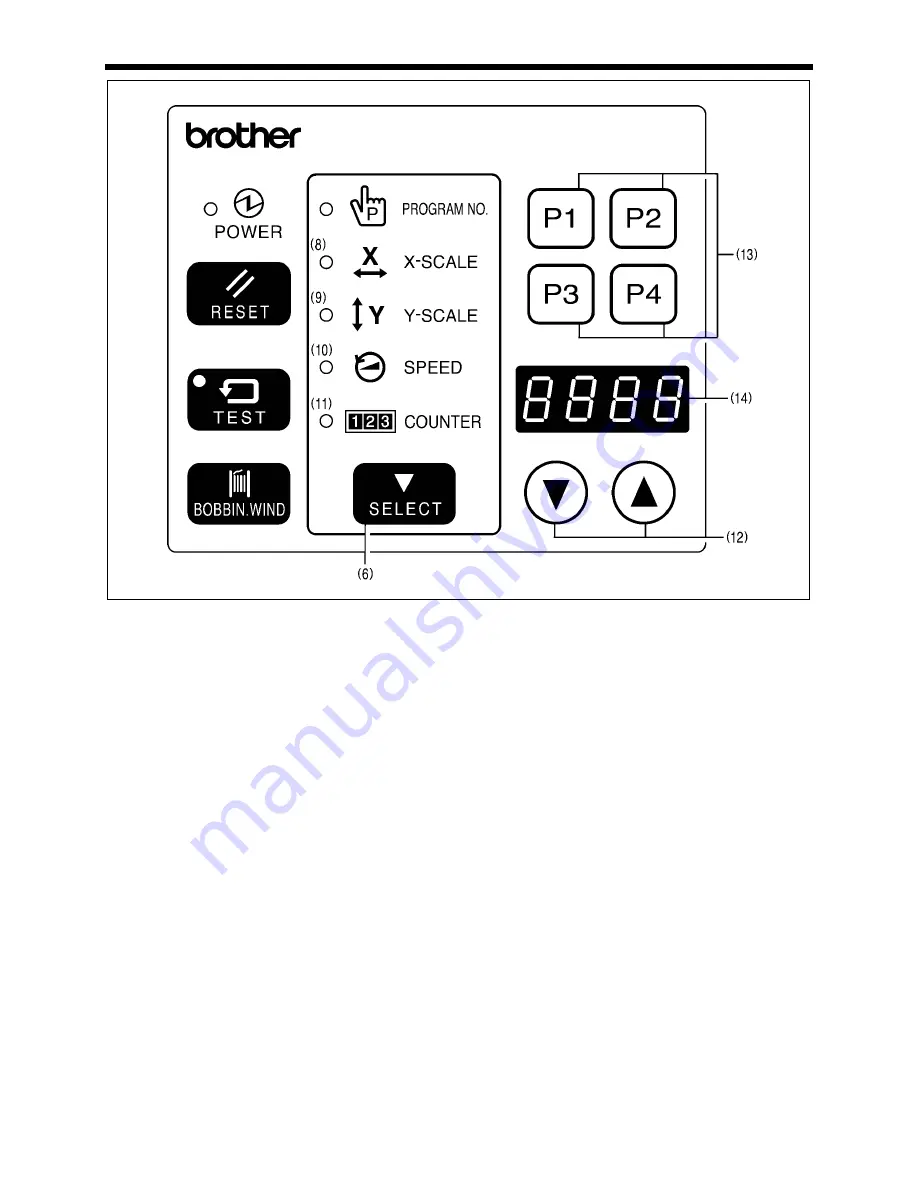
5. OPERATION
18
BE-438C
(8)
X-SCALE indicator .............. Illuminates when the SELECT switch (6) is pressed to shown the X-scale setting.
(9)
Y-SCALE indicator .............. Illuminates when the SELECT switch (6) is pressed to shown the Y-scale setting.
(10) SPEED indicator ................. Illuminates when the SELECT switch (6) is pressed to shown the speed setting.
(11) COUNTER indicator............ Illuminates when the SELECT switch (6) is pressed to show the bobbin thread or
production counter setting.
(12) DISPLAY SET switches ...... Used to change the menu details which are displayed in the window (14).
(13) User program switches ....... Used to set and select user programs.
(14) Display window ................... This display window will indicate the current statu for the selected menu, error or memory
switch.
2515Q