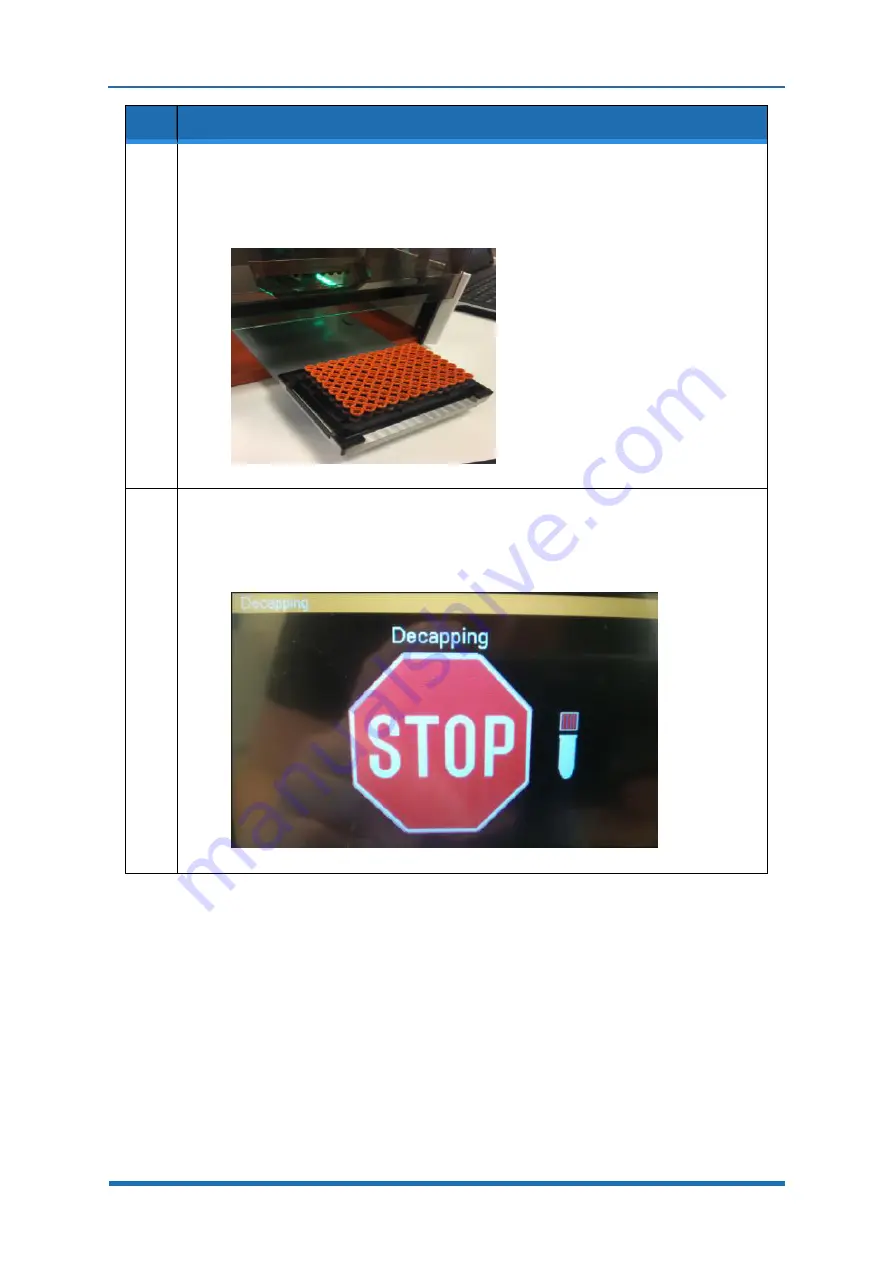
Brooks Automation
5. Operation
Part Number: 319430 Rev. A
Starting the IntelliXcap
Step
Action
5.
Place the correct rack for the cap-driver cartridge being used into the stage and press the start
button on the display.
Choose the
Start
button. The instrument confirms the height of the tubes and then starts de-
capping.
6.
When in use, the IntelliXcap displays the current process with a large
STOP
button display
indicating the unit is in use.
In case of need, you have the option to stop the current process by clicking the button on
screen or by pressing the E-Stop button located at the top of the unit.
Copyright © 2019, Brooks Automation, Inc.
24