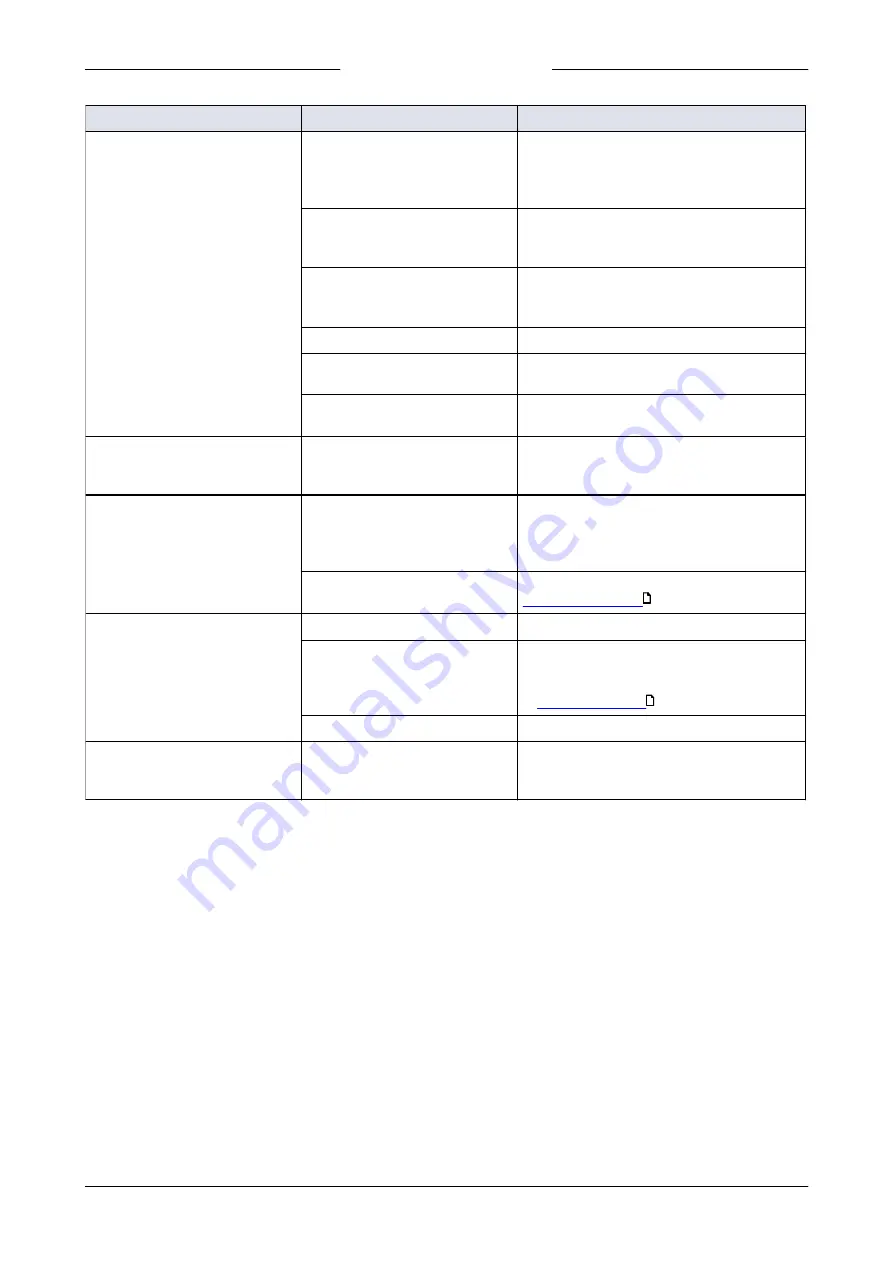
Bronkhorst®
Instruction Manual FLEXI-FLOW™ Compact
9.17.158A
19
Symptom
Possible cause
Corrective action
Flow rate never reaches setpoint
·
Piping, filters and/or control
valve clogged or blocked
·
Sensor obstructed or
contaminated
Flush fluid system with clean, dry air or non-
aggressive cleaning liquid (e.g. ethanol or
isopropyl alcohol)
Inlet pressure or differential
pressure too low
·
Check/increase inlet pressure
·
Use instrument in conditions it was designed
for
Outlet pressure too high
·
Check/decrease outlet pressure
·
Use instrument in conditions it was designed
for
Process outlet blocked
Check process outlet and downstream piping
Process gas condensation
Decrease inlet pressure or increase gas
temperature
Supplied fluid type does not match
selected fluid type
Supply equipment with other fluid or change
fluid type in instrument configuration
Pressure signal gradually
decreasing without setpoint
change
Process gas condensation
Decrease inlet pressure or increase gas
temperature
Measured value or output signal
indicates flow, while there should
be none
Fluid system leakage
·
Check fluid system for leakage
·
Follow mounting instructions when
installing third party components (e.g.
adapters, tubing, valves)
Zero point adjustment performed
incorrectly
Readjust zero point, following instructions in
Continuous maximum measured
value or output signal
Inlet pressure too high
Check inlet pressure
Valve fully open
·
Close valve
·
In case of normally open valve: check if valve
is in safe state; resolve cause if necessary (see
)
Sensor failure
Contact your Bronkhorst representative
Fluid system leakage
Bad connection between parts (e.g.
ferrules, nuts, tubing, piping,
valves)
Follow mounting instructions issued by third
party components (e.g. adapters, tubing, valves)
3.5
Returns
3.5.1
Removal and return instructions
When returning materials, always clearly describe the problem, and, if possible, the work to be done, in a covering letter.
Instrument handling:
1. Purge all fluid lines (if applicable)
2. If the instrument has been used with toxic or otherwise hazardous fluids, it must be cleaned before shipping
3. Disconnect all external cabling and tubing and remove the instrument from the process line
4. If applicable, secure movable parts with appropriate transport safety materials, to prevent damage during
transportation
5. The instrument must be at ambient temperature before packaging
6. Insert the instrument into a plastic bag and seal the bag
7. Place the bag in an appropriate shipping container; if possible, use the original packaging box
16
8