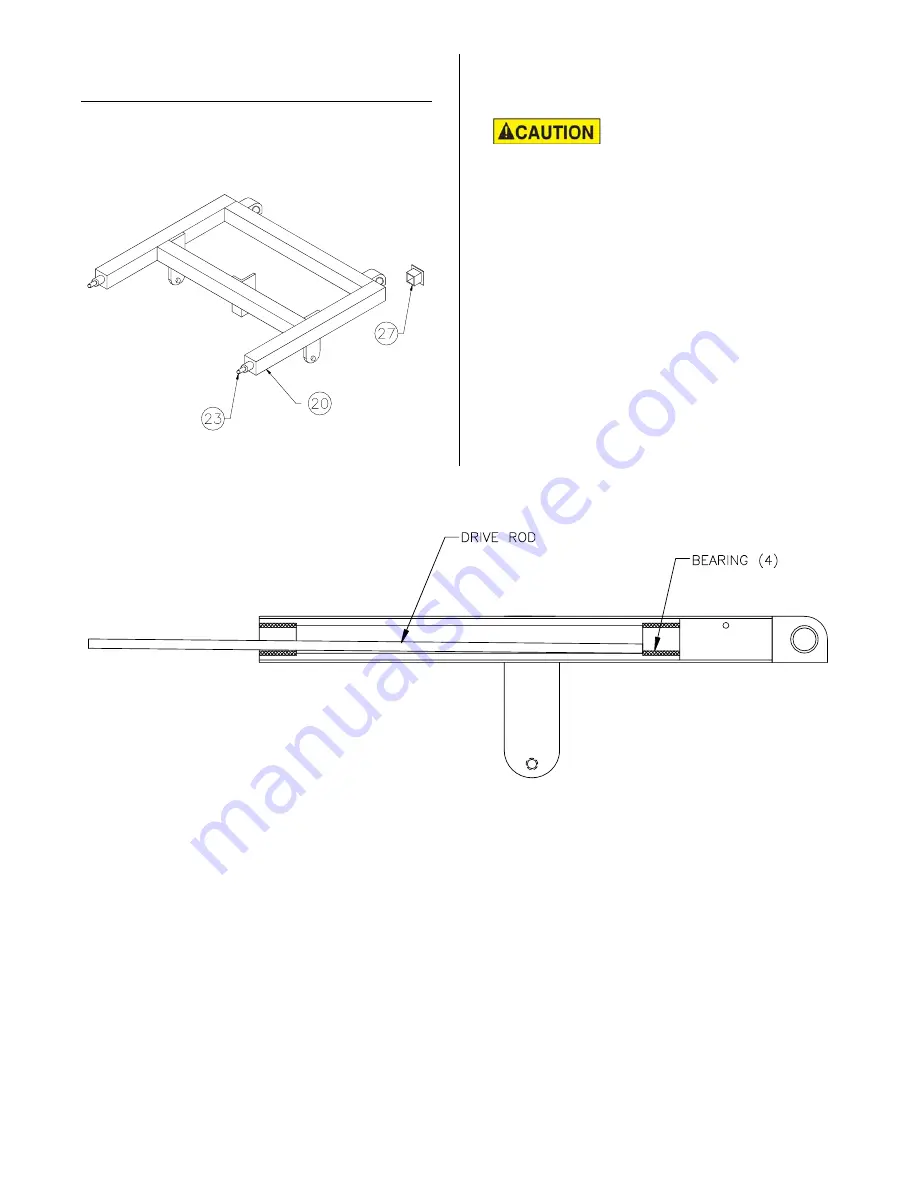
5-8
SLIDE ROD AND BEARING
REPLACEMENT
1. Remove plastic caps (27).
2. Remove the slide rod (23) from the lift
assembly (20).
DO NOT allow the sliding
rod bar to be damaged. It
may not be able to be reinserted into the
lift assembly.
3. Drive out old bearings using a bar
1/4” Dia. x 15” long. (See diagram).
4. Install new bearings.
5. Reassemble in reverse order.
broaster.com Manual #15460 8/02 Rev 6/15
Содержание 2004E
Страница 2: ......
Страница 8: ......
Страница 12: ......
Страница 21: ...2 9 MODEL 2400GH DOMESTIC MODEL 2400GHXP EXPORT broaster com Manual 15460 8 02 Rev 7 14 ...
Страница 22: ...2 10 MODEL 2400GHCE EU broaster com Manual 15460 8 02 Rev 7 14 1 2 2 1 2 1 ...
Страница 44: ......
Страница 45: ...5 COVER YOKE AND LIFT 5 1 FAMILIARIZATION broaster com Manual 15460 8 02 Rev 9 14 ...
Страница 54: ......
Страница 81: ...9 9 This page intentionally left blank broaster com Manual 15460 8 02 Rev 3 16 ...
Страница 87: ...broaster com Manual 15460 8 02 SERVICE NOTES ...
Страница 88: ...broaster com Manual 15460 8 02 SERVICE NOTES ...
Страница 89: ...broaster com Manual 15460 8 02 SERVICE NOTES ...
Страница 90: ......
Страница 91: ......
Страница 92: ...Broaster Company 2855 Cranston Road Beloit WI 53511 3991 608 365 0193 broaster com ...