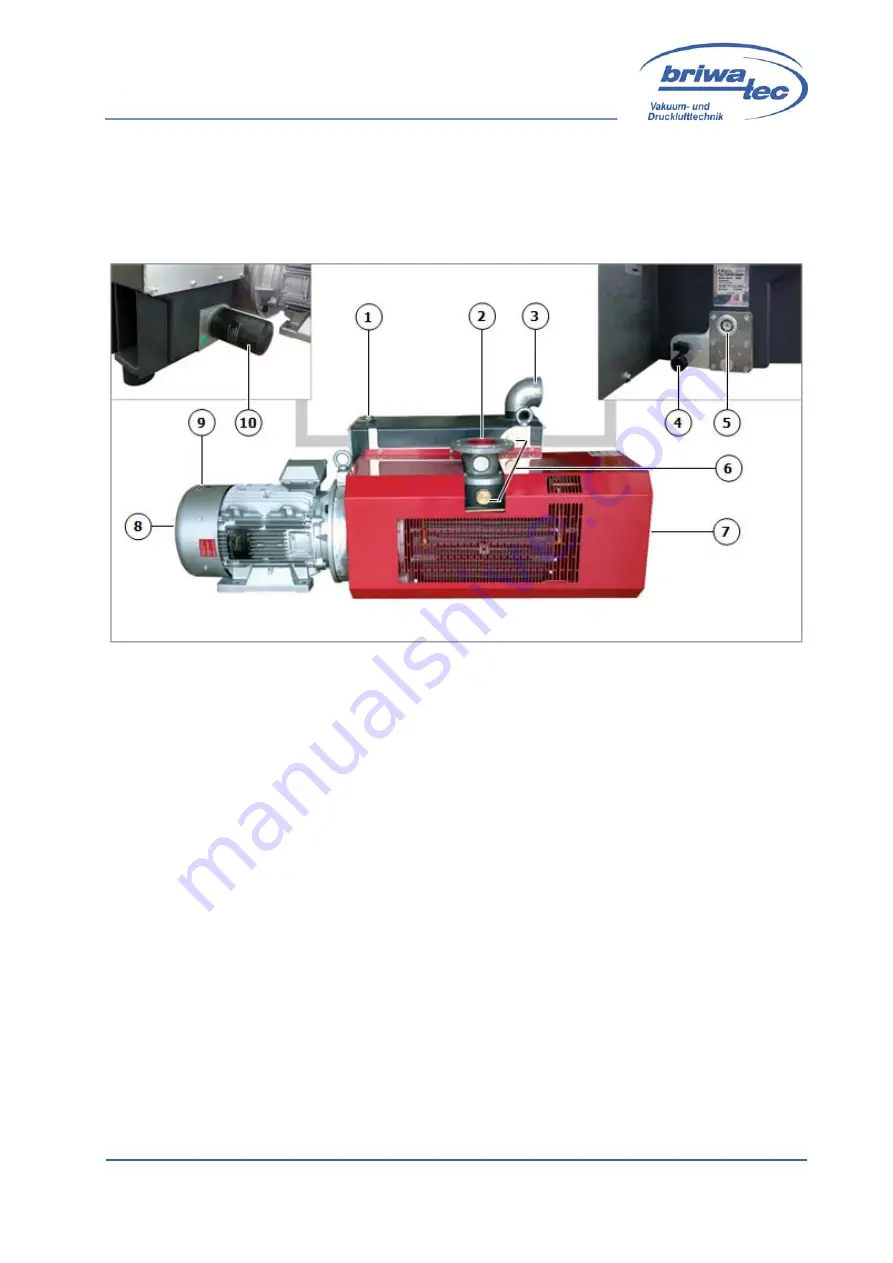
Functional description
B125 06/16 Rev.1
TOPAS E350V-E600V
14
5.2
Construction
The TOPAS rotary vane vacuum pump consists of the following major compo-
nents:
Fig. 4 TOPAS main components
1.
Oil filling point
2.
Vacuum connection
3.
Exhaust air outlet
4.
Oil drain valve
5.
Oil sight glass
6.
Connection for starting discharge (option with magnetic valve)
7.
Cooling air inlet
8.
Cooling air inlet
9.
Motor with direction of rotation arrow
10.
Oil filter