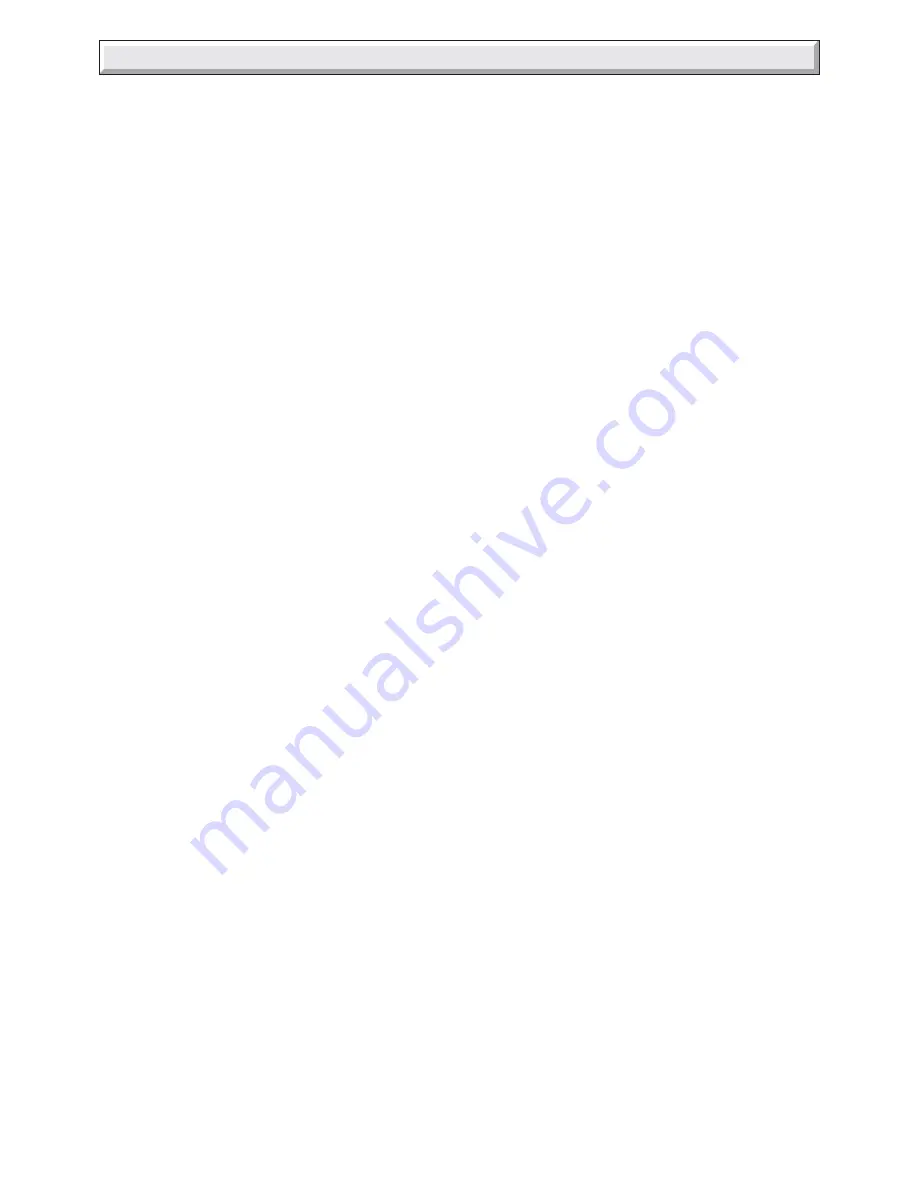
35
0020008877-04
13.1 Important Notes
When replacing a part on this appliance, use only spare parts
that you can be assured conform to the safety and performance
specification that we require. Do not use reconditioned or copy
parts that have not been clearly authorised by British Gas.
Replacement of parts must be carried out by a competent
person.
Before replacing any parts the boiler must be isolated from the
mains electric supply and the gas must be turned off at the
service cock on the boiler, see diagrams 11.2 and 11.3.
Unless stated otherwise parts are replaced in the reverse order
to removal.
After replacing any parts always test for gas soundness and if
necessary carry out functional test of the controls.
For replacement of parts, remove the casing panels and chassis
front panel of the boiler, see diagrams 10.1 and 11.5 .
Remove the two screws on the underside of the front casing,
then undo the two screws on the front of the inner front panel
and lift off. Remove the four screws from the chassis front
panel, then remove it by pulling it out at the top from its retaining
slots.
NOTE: When replacing chassis front panel ensure the bottom
fits behind the lip.
The side panels can be hinged sideways to aid replacement of
parts.
Undo and remove the three screws securing each side panel to
the boiler, two at the front and one at the top.
NOTE: The following replacement parts in sections 13.5 to 13.9
will require the removal of the burner door assembly. This will
require that you replace the burner door seal and nyloc nuts.
13.2 Spark Electrode
For access, refer to section 13.1.
Remove the spark plug lead, earth lead and two securing
screws. Withdraw the spark electrode carefully from the
combustion chamber, see diagram 11.4.
13.3 Igniter Unit
For access, refer to section 13.1.
Remove ignition lead and electrical connections, see diagram
13.4.
Remove igniter unit by removing two securing screws, see
digram 13.4.
13.4 Ignition Lead
For access, refer to section 13.1.
Refer to diagram 11.6.
Pull the spark plug style connector off the spark electrode and
the spade connector connected to the igniter unit.
13 Replacement of Parts
13.5 Gas Valve
For access, refer to section 13.1.
Refer to section 11.5 for removal of the fan, gas valve and
burner assembly.
Before removing the gas valve note its position on the fan.
Remove the three securing screws, which fix the gas valve,
plastic swirl plate to the venturi on the fan.
Remove the gas valve.
Remove the gas supply pipe from the gas valve.
When refitting the gas valve take care as it can be fitted more
than one way.
After assembly test for gas soundness and purge in accordance
with the current issue of BS6891 or in IE, the current edition of
I.S.813 "Domestic Gas Installations".
Once the appliance has been reassembled (apart from the front
and inner casing panels) the gas valve may require adjustment.
Connect a CO
2
combustion analyser to the sampling point on
the flue
elbow, see diagram 11.8.
Turn on the gas service cock, see diagram 11.3.
With the power off and the appliance cold, unclip the controls
fascia and hinge it down to reveal the potentiometers on the rear
of the User interface, see diagram 11.10. Take care not to allow
the fascia to drop down and damage the wiring.
Turn on the electrical supply.
Ensure external controls are calling for heat. The boiler should
fire automatically.
Allow the boiler to fire for a minimum of 60 seconds and then,
using an electrical screwdriver, rotate the ‘service’ potentiometer
fully clockwise, see diagram 11.10. This will allow the digital
display to indicate the ‘flashing’ fan speed on the appliance
fascia.
This should correspond to the range rated output of the boiler,
as indicated on the boiler data label. If the appliance is set to
18kW and the security label on the Pmax potentiometer is intact
this is the maximum output for the boiler. If the seal is broken the
output should be taken as 31kW, with an adequate gas supply,
see Range Rating Table 4.
If adjustment proves necessary then proceed as follows:
Any adjustment to the gas valve should only be carried out by
a competent person.
Refer to diagram 10.3.
Adjust the CO
2
with the throttle to 9.1% + 0.3 - 0.3.
(Rotate anti-clockwise to increase).
Rotate the ‘service’ potentiometer fully anti-clockwise. Hold it
in this position for about 5 seconds before rotating the service
potentiometer clockwise to the mid-point or 3 o’clock position.
The fan should reduce to 1200 rpm which will flash ‘12’ on the
digital display.
Check the CO
2
value which should be 9.1% + 0.3 - 0.3.
If adjustment of the CO
2
at minimum rate is required, it is very
coarse so carefully adjust the CO
2
with the offset adjustment to
9.1%, see diagram 10.3.
Rotate the ‘service’ potentiometer fully clockwise, see diagram
11.10, and recheck the combustion, which should be 9.1% +
0.3 -0.3.
Turn the service potentiometer back fully anti-clockwise to
return the boiler to normal operation, close the front fascia panel
and replace the cap on the sampling point.
Содержание 330
Страница 32: ...32 0020008877 04 12 Fault Finding Diagram 12 2 12933 ...
Страница 33: ...33 0020008877 04 12 Fault Finding 12191 Diagram 12 3 ...
Страница 34: ...34 0020008877 04 12 Fault Finding Diagram 12 4 12188 ...
Страница 42: ...42 0020008877 04 ...