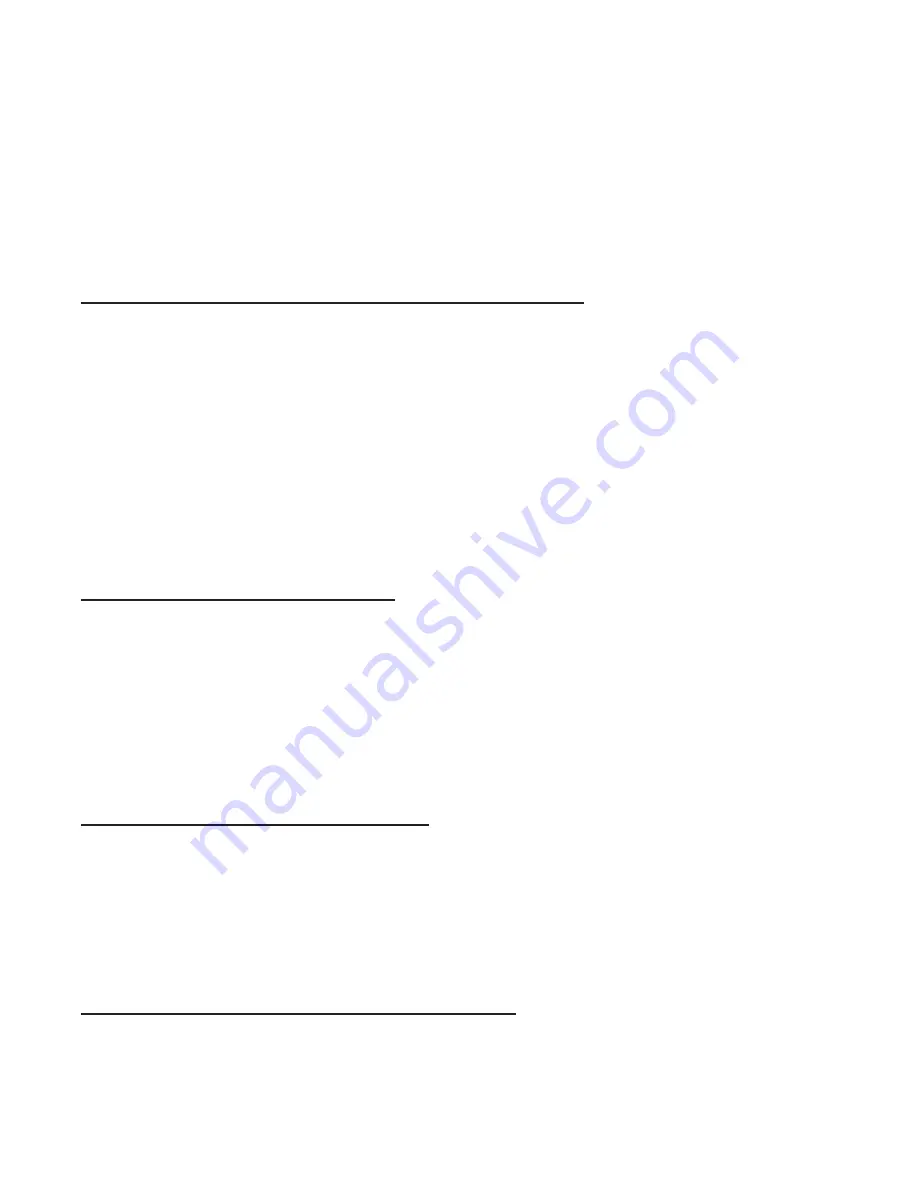
13
Inspection, testing, and preventive maintenance requirements are divided into several categories: Pre-use, Quarterly,
Semiannual and Annual as outlined below. The Installation, Maintenance, and Service Manual for each model provides
specific instructions for maintenance and service.
Some inspection intervals make reference to hoists used in severe-duty applications. Severe-duty applications are
where the hoist is operated more than 12 hours per day and/or for extended periods of time at or near the rated capac-
ity of the hoist.
Anytime that the hoist exhibits erratic operation and/or unusual noise(s), the hoist should be taken out of ser-
vice until it is inspected and serviced by a qualified technician.
REGULAR INSPECTION, TESTING, AND PREVENTIVE MAINTENANCE
— Must include, but not be limited to the
following:
PRE-USE INSPECTION (each shift the hoist is used)
: Will be performed prior to placing the crane into service and
then as necessary during the day for extended operation.
1. Check for external oil leaks and repair as necessary.
This is extremely important because of the accelerated
wear that can be caused by insufficient lubricating oil in the hoist.
Lubricant level must be maintained between
the maximum and minimum levels. Use only the recommended type of lubricant; see service manual for details. On
models without a sight glass, check oil level monthly.
2. Check the ratchet and pawl mechanism (if so equipped) for proper operation and for full engagement of the pawl with
the ratchet wheel. Repair and/or adjust as necessary.
3. Check hydraulic plumbing for damage, such as chafed or deteriorated hoses, and repair as necessary.
4. Visually inspect for loose or missing bolts, pins, keepers or cotter pins and replace or tighten as necessary.
QUARTERLY INSPECTION (every 3 months)
or monthly in severe-duty applications or prior to putting the machine
into service if it has not been used for 3 months or more. Documentation of the inspections must be kept with the hoist/
crane for a minimum of two years from the date of the inspection (see Page 3).
Perform the PRE-USE INSPECTION plus the following:
1. Check the lubricant level in the hoist(s) and maintain it between maximum and minimum levels. Use only recom-
mended type of lubricant; see service manual for details.
2. On hoists used for personnel handling, the internal spring-applied brake shall be tested in accordance with the pro-
cedure on Page 6 of publication PB-308.
3. Inspect for corrosion of fasteners, mounting base, drum, etc. and repair/replace as necessary.
SEMIANNUAL INSPECTION (every six months)
, or quarterly in severe-duty applications. Documentation of the
inspections must be kept with the hoist/crane for a minimum of two years from the date of the inspection (see next
page).
Perform the
PRE-USE INSPECTION
and
QUARTERLY INSPECTION
plus the following:
Take a sample of the lubricating oil from the hoist drum, following the oil sampling procedure on Page 5 of publication
PB-308, and analyze it for wear metals content, the correct viscosity, signs of overheating, water and other contami-
nates. If the oil sample contains an unusual amount of metallic particles, the hoist should be taken out of service and
undergo a teardown inspection. The oil sample must be taken prior to changing the lubricating oil. The semiannual
oil analysis can be omitted if the crane has been used less than 250 hours since the previous oil sample.
ANNUAL INSPECTION, Testing, and Preventive Maintenance
or semiannually in severe-duty applications. Docu-
mentation of the inspections must be kept with the hoist/crane for a minimum of two years from the date of the inspec-
tion (see next page). The annual inspection must include, but not be limited to the following:
1. Perform the
PRE-USE INSPECTION, QUARTERLY,
and
SEMIANNUAL INSPECTIONS
, plus the following:
2. Change lubricating oil in hoist drum or gearbox after oil sample is taken. Refer to Recommended Gear Oil, earlier in
this section. Failure to follow these recommendations may result in brake failure.
BRADEN recommends the following inspection, testing, and preventive maintenance procedures.
For additional details, refer to BRADEN publication PB-308.