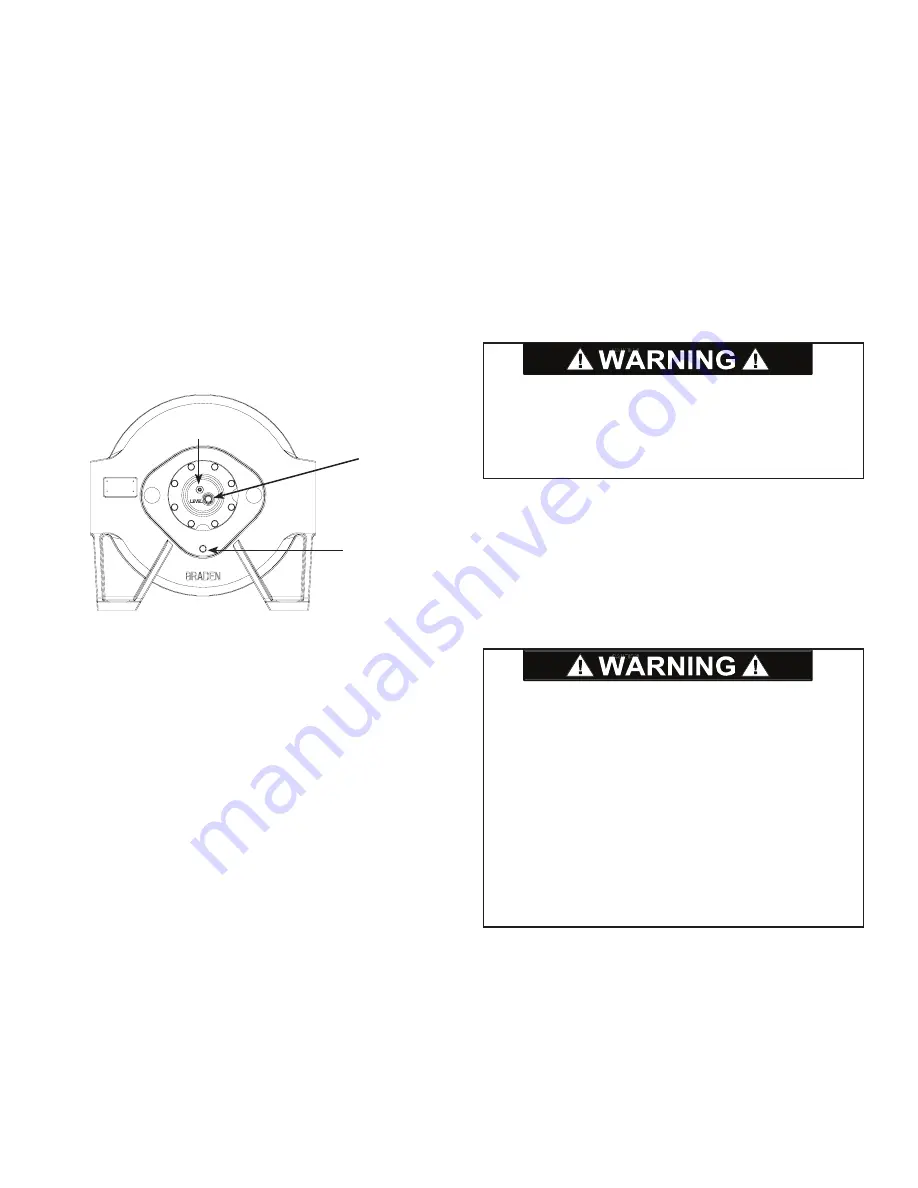
11
PREVENTIVE MAINTENANCE
A regular program of preventive maintenance for your
planetary hoist is strongly recommended to minimize the
need for emergency servicing and promote safe, reliable
hoist operation.
Initially, the gear oil should be changed after the first 100
hours of operation.
1.
Vent Plug and Oil Level
The vent plug and oil level sight gauge are located in the
bearing support on the end of the hoist opposite the motor.
It is important to keep the vent clean and unobstructed.
Whenever gear oil is changed, remove the vent plug and
sight gauge, clean in solvent and reinstall.
Do not paint over the vent or replace with a solid plug.
2.
Oil Change
Rotate the drum to align the drain plug with the lowest
hole in the support bracket. Install a short piece of 1-inch
pipe into the threads around the drain plug. Remove the
drain plug (5/16-inch hex) and drain the oil into a suitable
container. Always dispose of used oil in an environmental-
ly responsible manner. Remove the 1-inch pipe and rotate
the drum to align the hole in the drum with the highest hole
in the support bracket. Reinstall the pipe and fill the hoist
drum with the recommended oil to the center of the sight
gauge. Install the drain plug and remove the pipe.
3.
Hydraulic System
The original filter element should be replaced after the first
50 hours of operation, then every 500 operating hours or
three months, or in accordance with the equipment manu-
facturer’s recommendations.
4.
Wire Rope
Inspect entire length of wire rope according to wire rope
manufacturer’s recommendations.
5. Mounting Bolts
Tighten all hoist base mounting bolts to recommended
torque after the first 100 hours of operation, then every
1,000 operating hours or six months, whichever occurs first.
6. Warm-up Procedures
A warm-up procedure is recommended at each start-up
and is essential at ambient temperatures below +40°F
(4°C).
The prime mover should be run at its lowest recommended
RPM with the hydraulic hoist control valve in neutral,
allowing sufficient time to warm up the system. The hoist
should then be operated at low speeds, forward and
reverse, several times to prime all lines with warm hydraulic
oil, and to circulate gear lubricant through the planetary
gear sets.
7. Recommended Planetary Gear Oil
Field experience, supported by engineering endurance
tests, indicates use of the proper gear oil and a program of
regular preventive maintenance will help provide extended
gear train life and reliable hoist brake performance. Refer
to Recommended Gear Oil, later in this section.
For simplicity, BRADEN has listed available products in
each temperature range that have been tested and found
to meet our specifications. This is not to say that other
lubricant brands would not perform equally as well.
If the following lubricant brands are not available in your
area, make certain your lubricant vendor supplies you
with oil equivalent to those products listed on following
page..
Failure to properly warm up the hoist, particularly un-
der low ambient temperature conditions, may result in
temporary brake slippage due to high back pressures
attempting to release the brake, which could result in
property damage, severe personal injury, or death.
Failure to use the proper type and viscosity of planetary
gear oil may contribute to intermittent brake clutch slip-
page which could result in property damage, severe
personal injury, or death. Some gear lubricants contain
large amounts of extreme-pressure (EP) and antifric-
tion additives which may contribute to brake slippage
and damage to brake friction discs or seals. Oil viscos-
ity with regard to ambient temperature is also critical to
reliable brake operation. Our tests indicate that exces-
sively heavy or thick gear oil may contribute to inter-
mittent brake slippage. Make certain that the gear oil
viscosity used in your hoist is correct for your prevailing
ambient temperature.
Oil Level
Sight Gauge
Oil Drain
Hole(s)
Vent Plug