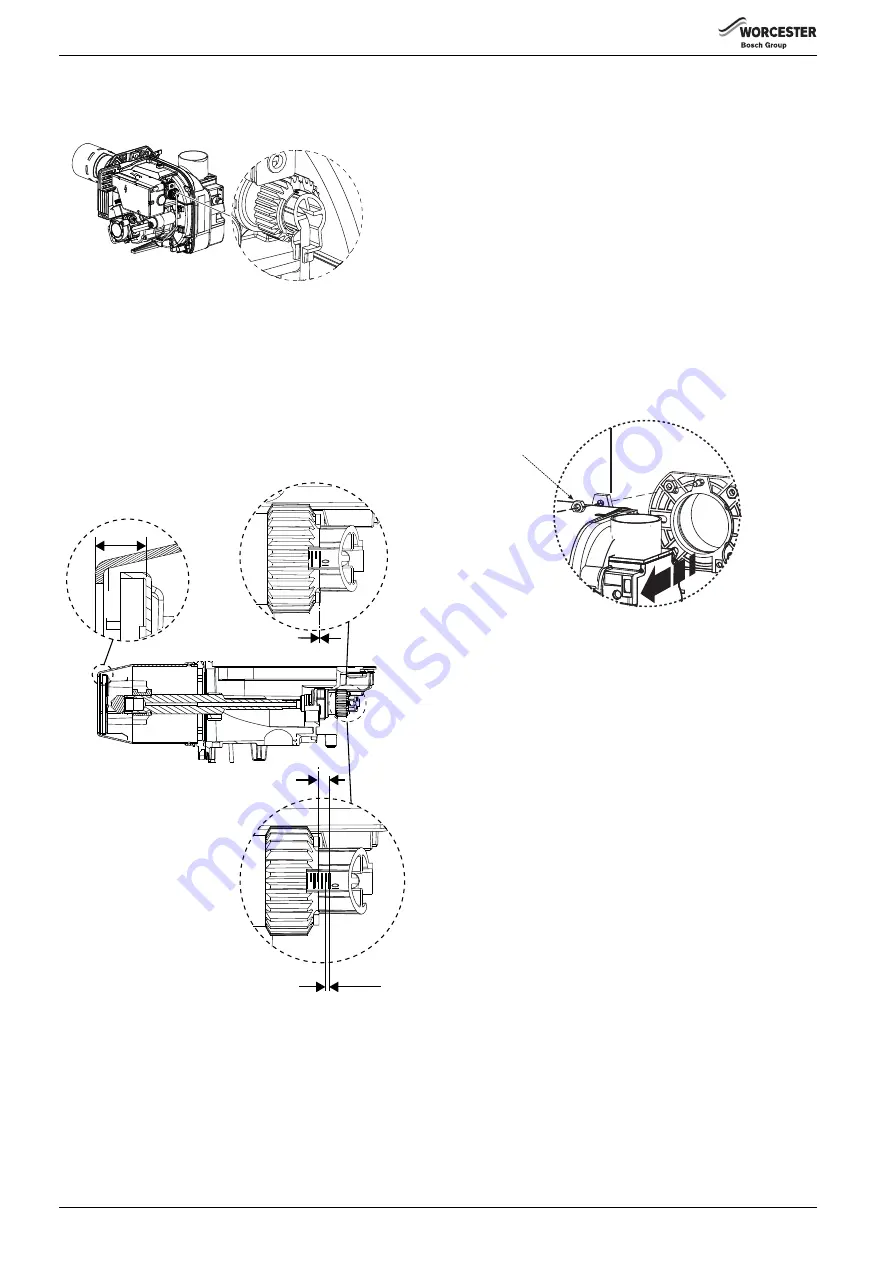
Commissioning
Greenstar Danesmoor Utility
ErP+
and Utility System
ErP+
- 6 720 821 720 (2018/04)
40
6.4.4
Burner head setting
Adjustments to the burner head are made on the basis of the required
output, refer to table 11 for the required setting for your boiler.
Fig. 67 Burner head adjustment thumbwheel
One complete rotation clockwise (cw) from the minimum position
equals approximately one millimetre. Adjust the thumb-wheel to achieve
the setting indicated in the table 11, according to your appliance model
and output.
Using an engineer’s rule or vernier gauge measure from the lip of the
blast tube to the inside of the break plate as show in the figure below.
Ensure that the break plate is level, check at four equal points to get an
average of the required setting. The setting tolerance should be no more
than
±
0.25mm
Fig. 68 Burner head adjustment
6.4.5
Boiler lockout indicator on:
If the burner fails to establish a normal firing pattern or flame failure
occurs the flame monitoring photocell mounted in the burner body will
alert the burner control box to shut the burner down and provide a safe
lockout state indicated by the illumination of the lockout indicator (D).
▶ Wait 2 minutes then press the lockout reset button D (
to initiate another start sequence.
▶ Repeat procedure until a flame is established.
1. Start and run for 3 minutes then switch off.
▶ Release the burner retainer nut (F).
▶ Remove the burner.
▶ Check for after-spurting from the nozzle, indicated by oil saturation
on the combustion head (
item G, figure 71).
If after-spurting occurs:
▶ Remove the combustion head (G) and electrodes, hold the burner
vertical to unscrew the nozzle and fill the nozzle holder with
kerosene.
▶ Refit nozzle, electrodes, combustion head (G) and the burner.
▶ Restart and run for 3 minute intervals until after-spurting stops.
Fig. 69
6720821683-24.1W
o
D
X=0
1
m m
X
6720821683-23.1Wo
1.
F
6720808218-59.1Wo