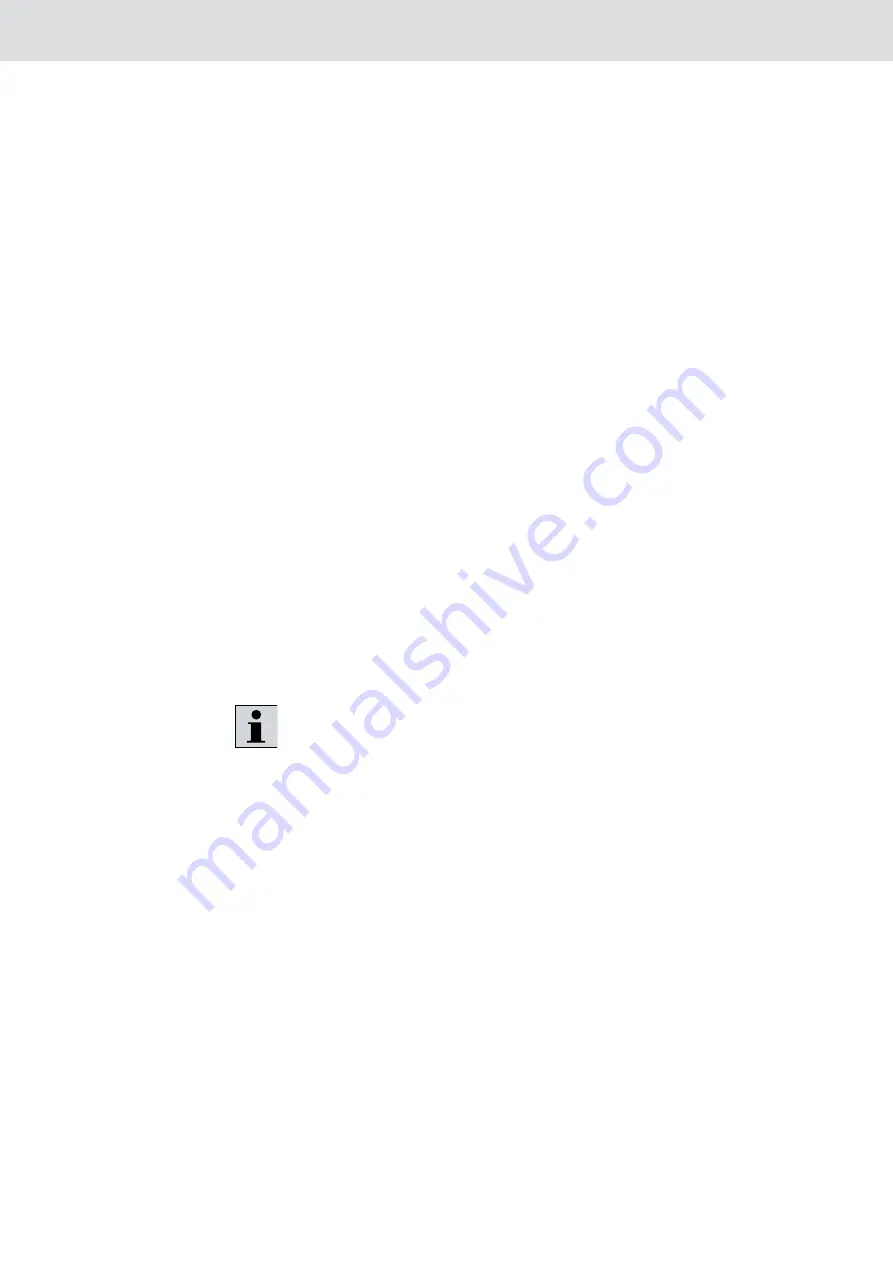
34/
56
Bosch Rexroth AG
Drive modules | RE 51150-B/07.11
Commissioning
Commissioning
8.1.8
The following steps are to be performed unless superordinate commissioning
instructions applicable at machine level are to be observed.
Start the electric motor in inching mode. Check the direction of rotation.
f
Flush the hydraulic system as described in Chapter 8.1.9.
f
Operate the directional valves and extend and retract the actuators several
f
times. Repeat the bleeding processes (bleeding is ensured if there is no oil
foam in the tank, no jerky movements at the actuator and no abnormal nois-
es).
Operate the system at low pressure until the drive module is completely bled.
f
Only increase the load step by step.
Observe the fluid level in the container and top up, if necessary.
f
Monitor the operating temperature as it sets itself after the machine has been
f
in full operation for several hours.
Check the drive module for external leakage, seal any leakage points; check
f
the connection points again for tightness after a few hours.
Tables describing the fault causes and their consequences in drive modules are
available as support for the systematic search and/or localization of faults
(see Chapter 15).
Flushing the hydraulic system
8.1.9
Flushing the hydraulic system to attain a specified oil cleanliness class prevents
faults and simultaneously increases the service life of the components. After in-
stalling the drive module into the machine and/or after installing with the hydraulic
system, it must be ensured that the minimum requirements are met with respect
to the cleanliness class of the components. Hydraulic systems in general indus-
trial applications require a cleanliness class of 20/18/15 according to ISO 4406,
whereas hydraulic systems with servo valves or high-response valves of higher
quality demand a higher cleanliness class e.g. 18/16/13.
You must take into consideration the cleanliness requirement for the compo-
nents as specified on the manufacturers' data sheets, when determining the
flushing target.
Preparations:
•
Supply of spare or flushing filter elements
If required: Supply of additional material for piping and hose assemblies for
•
establishing flushing and/or shorting links
Supply of flushing plates or directional valves
•
On a case-by-case basis: Supply of flushing fluid (see following note)
•
You can use the same medium as the one that is also to be used later when
operating the hydraulic system. When using another hydraulic fluid, the latter
must be compatible with the operating medium intended for use with the hydraulic
system, as well as with the materials, particularly seals, used in the hydraulic
system. A maximum admissible residual amount of flushing liquid in the operating
medium (e.g. 0.5 volume %) may be specified in certain circumstances (see
manufacturer’s specification); in this case, this has to be assured by carefully
draining the flushing liquid before filling with the operating medium.
Problems in the commissioning
Necessary material
Information on the flushing liquid