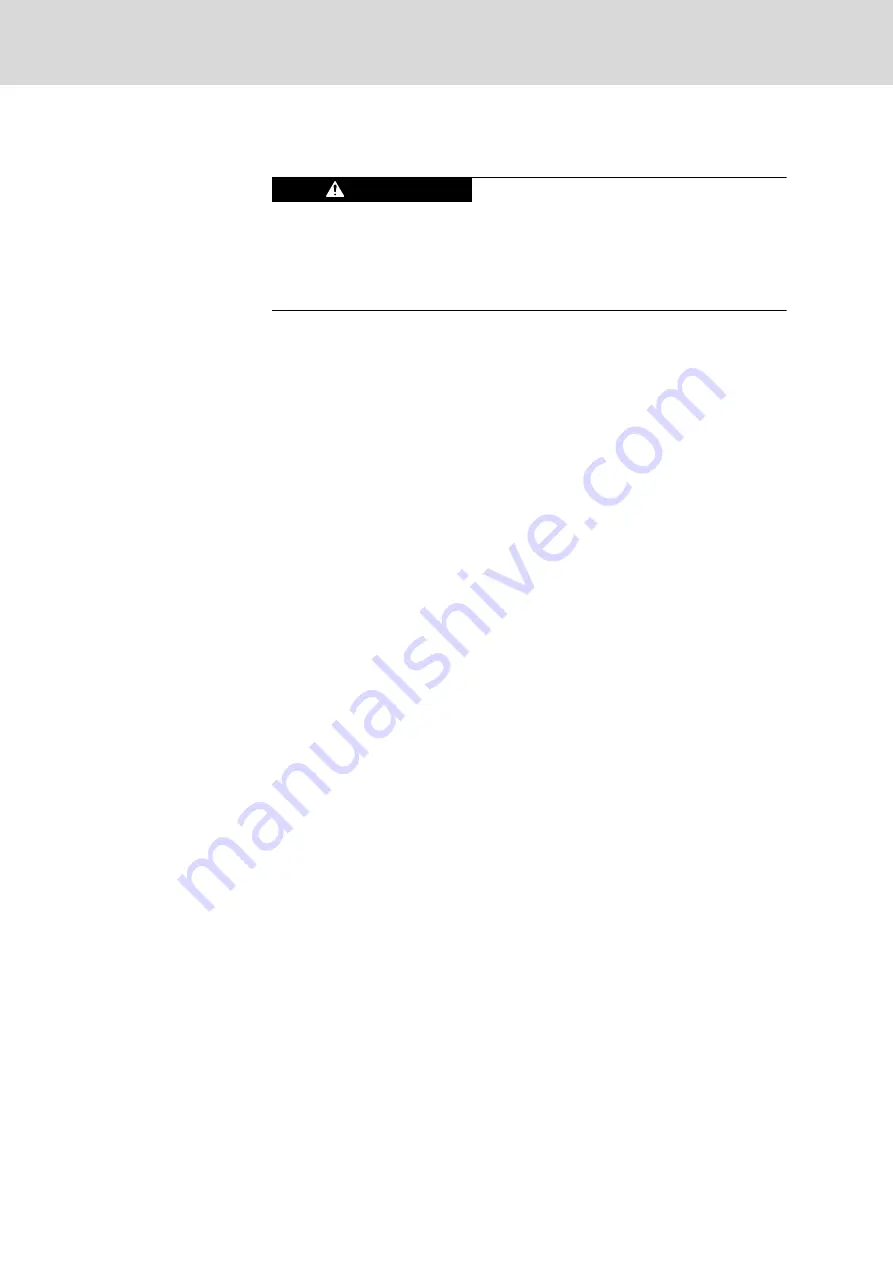
9.1.2
Application Conditions ATEX Device Group II, Category 2
Danger of explosion and life or high damage
to property!
DANGER
All used components and accessory parts must fulfill the requirements for ex‐
plosion protection according to the 94/9/EG directive.
The conditions on use given in this documentation must be taken into ac‐
count for any project planning and be observed during operation.
Notes about test number
The EC type test certificate number for MKE motors is designated by the "X"
in the declaration of conformity and on the type plate. This identification is a
note about special conditions, which have to be observed with regard to the
specified safety and medical requirements of this underlying standards.
Please observe the following special conditions for a safe operation of the
motors in your construction:
●
The allowed ambient temperature is 0 … 40 °C.
●
The gap width and length acc. to EN 60079-1:2009, table 1 were ex‐
ceed or fall below to ensure the higher requirements of the UL 674. A
repair acc. to the values of table 1 in EN 60079-1 is not allowed.
●
Maintenance and repair of motors have to be done by Rexroth service.
●
Use screws with a minimum property class of 8.8 to fasten the pressur‐
izing room (housing, terminal box, ...).
●
Only such components for assembly and disassembly (cables and cable
entries, connecting parts, bulk head connectors, ...) are allowed, which
correspond technically to the standards EN 60079-0:2009, EN
60079-15:2010, EN 60079-31:2009, which are suitable for the condi‐
tions of use and have a special certificate.
Maximum housing temperature
The maximum housing temperature is 115 °Con the motor housing at an am‐
bient temperature of 40 °C. The ignition temperature of materials which come
into contact with the motors must not come under 135°C.
Connection Conditions
The motors are only allowed to operate with the Rexroth drives IndraDrive,
ECODRIVE, DURADRIVE and DIAX04. Drive control devices of other manu‐
facturers are not permitted.
Grounding
Speed-controlled drive systems create discharge currents. For this reason
the motors have to be grounded over the motor cable and over a second sep‐
arate ground wire with a minimum cross section of 4 mm². Check that the po‐
sition of the grounded conductor is fixed before commissioning.
Corrosion
Corrosion of the motor housing by aggressive materials (such as certain cool‐
ants, lubricants, cutting oils or salt mists) must be prevented.
Emergency stop
Stored energies in the drive controller must be removed or isolated as quickly
as possible when the emergency stop device is actuated to ensure that the
risk or an effect into the danger zone is reduced in the event of a failure
(ATEX directive 94/9/EC, appendix II, chapter 1.6.2)
The user has the following possibilities:
●
Energy isolation is guaranteed from the exit of the drive device, if at
emergency stop, in addition to the power loss of the drive device is
locked electronically. This results from line contactor-shutdown with sub‐
sequent failure reaction of the drive device because of power failure (cp.
F281). Adjusting the required drive-end failure reaction must be made
by the user at the drive device via the drive parameters (cp. P-0-0119)
according to the functional description.
Bosch Rexroth AG
DOK-MOTOR*-MKE*GEN2***-PR06-EN-P
Rexroth MKE Synchronous Motors for Potentially Explosive Areas acc. to ATEX and UL/CSA
76/135
Operating Conditions and Application Notes
LSA Control S.L. www.lsa-control.com [email protected] (+34) 960 62 43 01