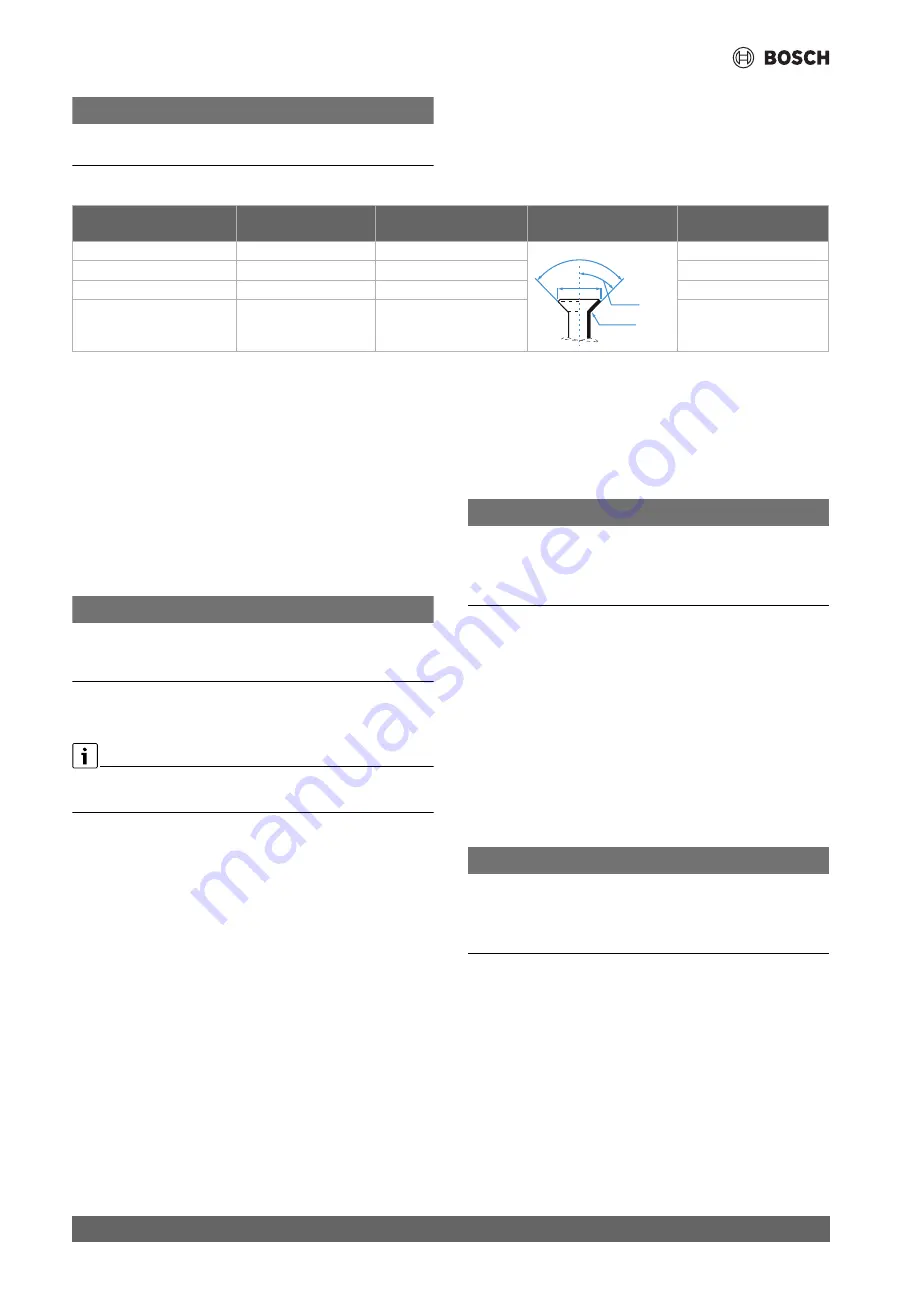
Installation
Climate 5000 L • Climate 5000i U/L – 6721841493 (2022/05)
58
NOTICE
Reduced efficiency due to heat transfer between refrigerant pipes
▶ Thermally insulate the refrigerant lines separately.
▶ Fit the insulation on the pipes and secure.
Table 8 Key data of pipe connections
3.5.2
Connecting condensate pipe to the indoor unit
Depending on the type of installation, the condensate pipe must either
be connected to the integrated condensate pump or the condensation
catch pan.
▶ Use PVCpipes with 32 mm inside diameter and 5-7 mm wall
thickness.
▶ Insulate drain pipe to prevent condensate formation.
▶ Connect drain pipe to indoor unit and secure connection with
a hose clip.
▶ Install drain pipe on slope (
Fig. 20). With a condensate pump
installed, the outlet of the drain pipe may be higher than the indoor
unit if the dimensions and wiring diagram are observed.
NOTICE
Danger due to water damage!
If the pipes are routed incorrectly, water may be discharged, or may flow
back into the indoor unit and cause the water level switch to malfunction.
▶ To prevent the pipes from sagging, install a support every 1–1.5 m.
▶ Route a drain pipe to the sewer via a siphon.
Testing the condensate pipe ensures that all connections are tight.
▶ Test the condensate pipe before closing the cover.
3.5.3
Testing the condensate pipe
if the condensate pump can only be tested once the electrical connection
has been established.
▶ Fill the condensation catch pan or water injection pipe with roughly
2 l of water.
▶ Switch on cooling mode. The drainage pump can be heard.
▶ Make sure that the condensate drains away properly.
▶ Check tightness of all connections.
3.5.4
Checking tightness and filling the system
Checking tightness
Observe the national and local regulations when carrying out the
tightness test.
▶ Remove the caps of the valves of a connection pair
(
Fig. 15 and 16, [1], [2] and [3]).
▶ Connect the Schrader opener [6] and pressure gauge [4]
to the service socket [1].
▶ Open Schrader valve [1].
▶ Leave valves [2] and [3] closed and fill the pipes with nitrogen until
the pressure is 10% above the maximum operating pressure
(
Page 66).
▶ Check whether the pressure is still the same after 10 minutes.
▶ Discharge the nitrogen until the maximum operating pressure is
reached.
▶ Check whether the pressure is still the same after at least 1 hour.
▶ Discharge nitrogen.
Filling the system
NOTICE
Malfunction due to incorrect refrigerant
The outdoor unit is filled with refrigerant R32 at the factory.
▶ If refrigerant needs to be topped up, only use the same refrigerant.
Do not mix refrigerant types.
▶ Evacuate and dry the pipes with a vacuum pump (
[5]) for at least 30 minutes at roughly −1 bar (approx. 500 microns).
▶ Open valve [3] on liquid side.
▶ Use a pressure gauge to [4] check whether the flow is unobstructed.
▶ Open valve [2] on gas side.
The refrigerant is distributed round the connected pipes.
▶ Afterwards, check the pressure ratios.
▶ Unscrew the Schrader opener [6] and close the Schrader valve [1].
▶ Remove the vacuum pump, pressure gauge and Schrader opener.
▶ Reattach the valve caps.
▶ Reattach the cover for pipe connections to the outdoor unit.
3.6
Mount the wired room controller
NOTICE
Damage to the wired room controller
Opening the wired room controller in the wrong way or tightening the
screws too tightly can damage it.
▶ Do no exert too much pressure on the wired room controller.
▶ Remove the wall plinth of the wired room controller (
Fig. 24).
– Insert the tip of a screwdriver at the bending point [1] on the rear
of the wired room controller.
– Lift up the screwdriver to lever open the wall plinth [2].
▶ If necessary, prepare the wall and communication wire (
Fig. 25).
– [1] Realise putty or insulating material.
– [2] Make an elbow in the cable.
▶ Attach the wall plinth to the wall (
Fig. 26, [1]).
▶ Fix the wired room controller to the wall plinth (
Fig. 28).
External diameter of pipe Ø
[mm]
Tightening torque [Nm]
Flared opening diameter
(A) [mm]
Flared pipe end
Pre-assembled flare nut
thread
6.35 (1/4")
18-20
8.4-8.7
3/8"
9.53 (3/8")
32-39
13.2-13.5
3/8"
12.7 (1/2")
49-59
16.2-16.5
5/8"
15.9 (5/8")
57-71
19.2-19.7
3/4"
R0.4~0.8
A
45°± 2
90°± 4
Содержание CL5000iL CF 53 E
Страница 30: ......
Страница 31: ...Bosch Thermotechnik GmbH Junkersstrasse 20 24 D 73249 Wernau www bosch thermotechnology com ...