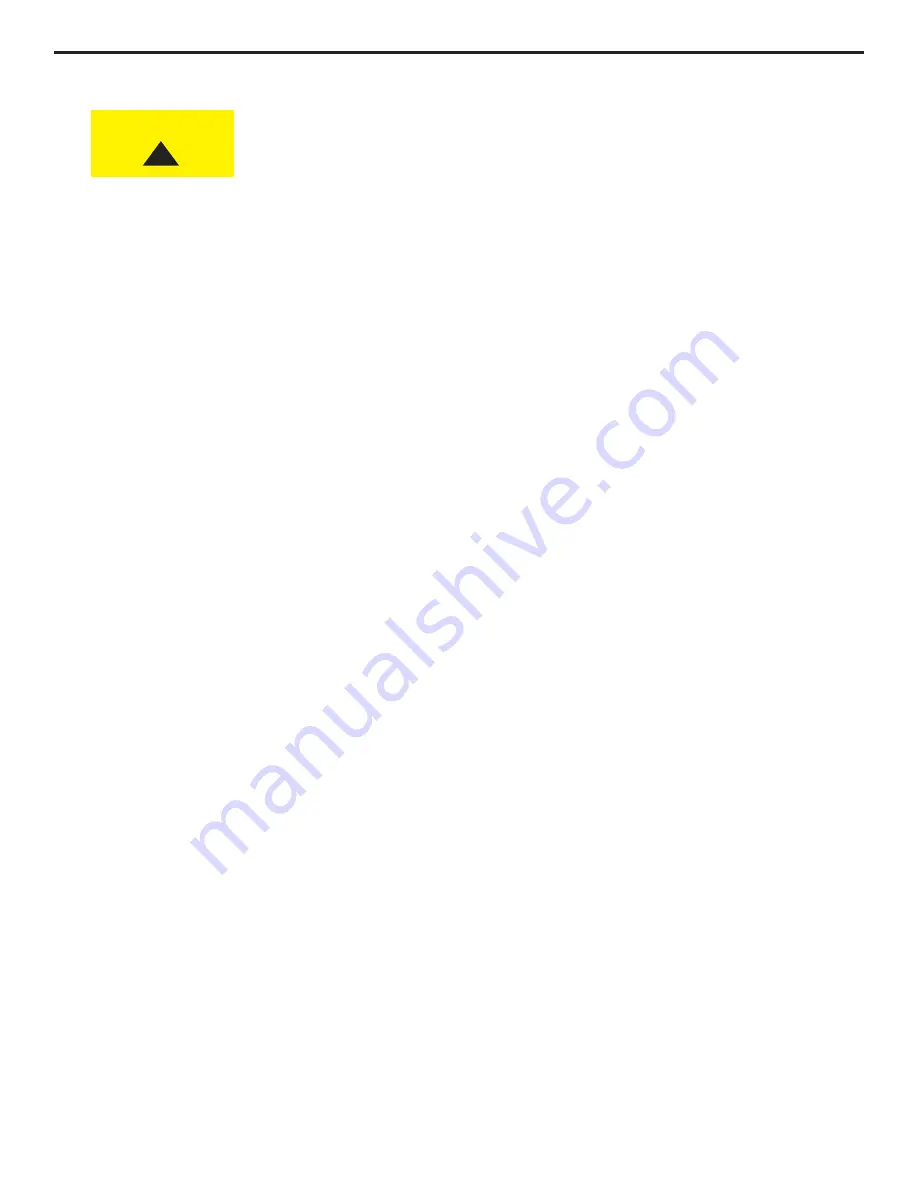
9.0
OUTPUT ADJUSTMENT
The speed of the pumping mechanism is adjustable from 0.01 to 100 % motor speed (0.01 RPM to 65 RPM).
10.0 ENHANCED TUBE FAILURE DETECTION (TFD+)
The pump is equipped with a Enhanced Tube Failure Detection (TFD+) system,
which is designed to stop the pump and provide an output alarm in the event
the pump tube should rupture, and a chemical enters the pump head.
This TFD+ system can detect the presence of many chemicals, including
sodium hypochlorite (chlorine), hydrochloric (muriatic) acid, sodium hydroxide,
oils based polymers, water based polymers, and many others. The system will
not be triggered by water (rain, condensation, etc.) or silicone oil (roller lubri-
cant).
NOTE
: If the system has detected a chemical, the pump tube must be
replaced, and the pump head and roller assembly must be thoroughly
cleaned. Failure to clean the roller assembly will void the warranty.
NOTE
: If the TFD+ alarm is triggered, the pump will stop, and close an alarm
output.
Fluid
Tubing failure
10.1 Confirming Chemical Detection
To determine if a chemical will be detected by the system:
1. Remove the pump head cover, and the pump tube and roller assembly.
2. Place a small amount of chemical in the bottom of the pump head that is enough to cover the sensors.
3. Reinstall
only
the pump head cover.
4. Turn on the pump by pressing the START button.
NOTE
: If the TFD+ system
detects
a chemical, the pump will stop after a two-second confirmation period.
NOTE
: If the TFD+ system
does not detect
a chemical, the pump will continue to operate after the
confirmation period.
5. Carefully clean the chemical out of the pump head. Ensure to remove all the chemical traces from the sensor
probes.
6. Replace the roller assembly and tubing.
7. Reinstall the pump head cover.
8. Press the START button to clear the alarm condition.
9. Restart the pump.
11.0 PUMP MAINTENANCE
Always wear protective clothing, face shield, safety glasses and gloves when working on or
near your metering pump. Additional precautions should be taken depending on the solution
being pumped. Refer to MSDS precautions from your solution supplier.
11.1 Routine Inspection and Maintenance
The pump requires minimal maintenance. However, the pump and all the accessories should be checked weekly,
especially when pumping chemicals. Inspect all the components for signs of leaking, swelling, cracking,
discoloration, or corrosion. Immediately replace worn out or damaged components.
Cracking, crazing, or discoloration during the first week of operation are signs of a severe chemical attack. If this
occurs, perform the following steps:
1. Immediately remove the chemical from the pump.
2. Determine which parts are being attacked.
3. Replace the damaged parts with parts that have been manufactured using more suitable materials.
4. After servicing, operate the pump to verify normal operation.
NOTE
: The manufacturer does not assume responsibility for damage to a pump that has been caused by a
chemical attack.
11.2 Cleaning and Lubricating the Pump
>
The pump will require occasional cleaning, and it will depend on the severity of service.
>
When changing the pump tube assembly, the pump head chamber, the roller assembly, and the pump head
cover should be wiped of any dirt and debris.
>
Clean the motor shaft with a clean towel, and then apply a small amount of grease to the shaft. This will help
prevent the rotor from sticking to the motor shaft.
>
Periodically, or when necessary, grease the pump head cover bearing. Apply a small amount of grease
(Aeroshell aviation grease #5 or equivalent).
>
100% silicone lubrication may be used on the roller assembly.
>
Periodically clean the injection fitting /check valve assembly, especially since injecting fluids, like sodium
hypochlorite, can calcify. These lime deposits and other buildups can clog the fitting, increase back pressure,
and interfere with the check valve operation.
>
Periodically clean the suction strainer.
CAUTION
!
Page 16
®
FLEXFLO M1
Page 17
®
FLEXFLO M1
Содержание FLEXFLO M1 Series
Страница 1: ...Peristaltic Metering Pump Series M1...
Страница 25: ...1 2 3 4 5 6 Page 25 14 1 EXPLODED VIEW FLEXFLO M1...