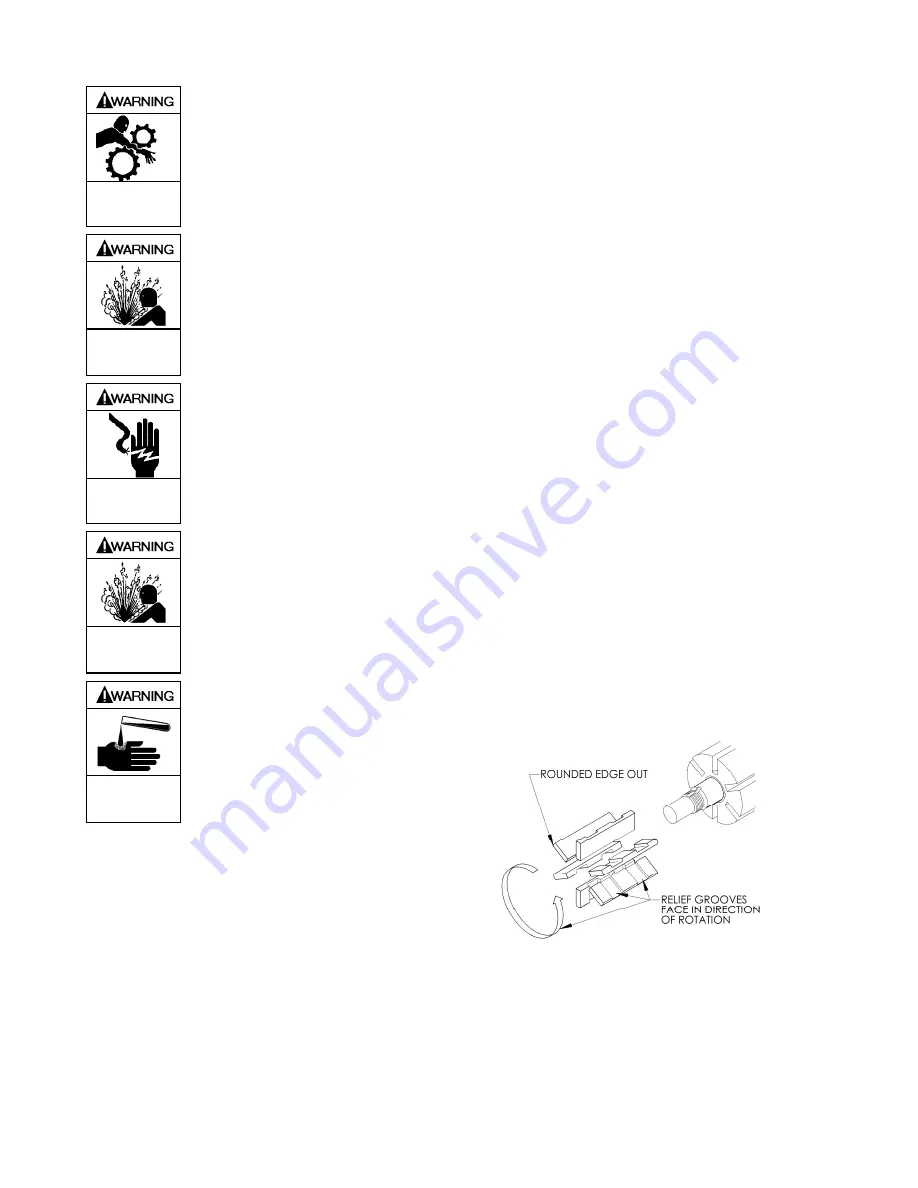
104-A00 Page 7/12
MAINTENANCE
Failure to disconnect and lockout
electrical power or engine drive before
attempting maintenance can cause
severe personal injury or death
Hazardous
machinery can
cause serious
personal injury.
Failure to relieve system pressure prior
to performing pump service or
maintenance can cause personal injury
or property damage.
Hazardous pressure
can cause personal
injury or property
damage
Failure to disconnect and lockout
electrical power before attempting
maintenance can cause shock, burns or
death
Hazardous voltage.
Can shock, burn or
cause death.
Disconnecting fluid or pressure
containment components during pump
operation can cause serious personal
injury, death or major property damage
Hazardous pressure
can cause personal
injury or property
damage
If pumping hazardous or toxic fluids,
system must be flushed and
decontaminated, inside and out, prior to
performing service or maintenance
Hazardous or toxic
fluids can cause
serious injury.
NOTICE:
Maintenance shall be performed by qualified technicians
only. Following the appropriate procedures and
warnings as presented in this manual.
STRAINERS
Strainers must be cleaned regularly to avoid pump starvation.
Schedule will depend upon the application and conditions.
LUBRICATION
NOTICE:
To avoid possible entanglement in moving parts do not
lubricate the pump, gear reducer or any other parts while
the pump is running
.
NOTICE:
If pumps are repainted in the field, ensure that the
grease relief fittings (76A) are functioning properly after
painting. Do NOT paint them closed. Remove any
excess paint from the fittings.
Lubricate the ball bearings, and motor couplings (if required),
every three months at a minimum
Recommended Grease:
Mobil® - Mobilgrease XHP222,
Exxon® - RONNEX MP Greas
e,
or equivalent.
Greasing Procedure:
1. Remove the grease relief fittings (76A) from the bearing
covers (27A).
2. Apply grease with a hand gun until grease begins to
escape from the grease relief fitting port.
3. Replace the grease relief fittings (76A).
DO NOT over grease pump bearings. While it is normal for
some grease to escape from the grease tell-tale hole after
lubrication, excessive grease on pumps equipped with
mechanical seals can cause seal failure.
VANE REPLACEMENT
NOTICE:
Maintenance shall be performed by qualified technicians
only. Follow the appropriate procedures and warnings
as presented in manual.
1. Remove the head assembly and all other parts on the
outboard (non-driven) side of the pump. See the "Pump
Disassembly" Section.
2. Turn the shaft by hand until a vane (14) comes to the top
(12 o'clock) position of the rotor.
Figure 5 –
Vane
Replacement
3. Remove and replace the vane, making sure to install the
vane with the rounded edge outward to contact the
cylinder and the relief grooves are facing towards the
direction of rotation.
4. Rotate the shaft until the next rotor slot is in the top
position, and replace the vane.
5. Continue this procedure until all new vanes are in place.
6. Reassemble the pump as instructed in "Pump
Assembly."