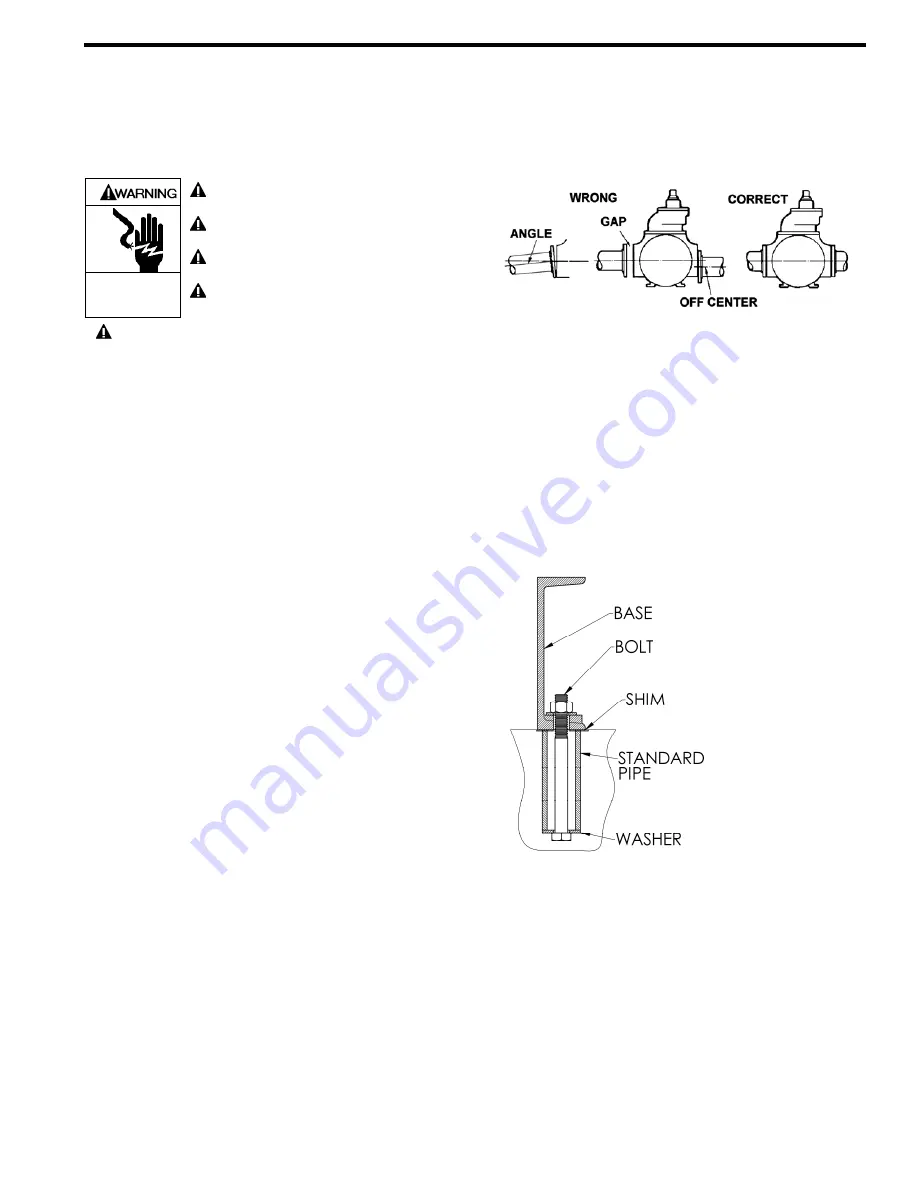
104-A00 page 3/12
INSTALLATION
NOTICE:
Blackmer pumps must only be installed in systems
designed by qualified engineering personnel. System
design must conform with all applicable regulations and
codes and provide warning of all system hazards.
Install, ground and wire to local and
National Electrical Code requirements.
Install an all-leg disconnect switch near
the unit motor.
Disconnect and lockout electrical power
before installation or service
Electrical supply MUST match motor
nameplate specifications.
Hazardous voltage.
Can shock, burn or
cause death.
Motors equipped with thermal protection automatically
disconnect motor electrical circuit when overload exists.
Motor can start unexpectedly and without warning.
PRE-INSTALLATION CLEANING
NOTICE:
New pumps contain residual test fluid and rust inhibitor.
If necessary, flush pump prior to use.
Foreign matter entering the pump WILL cause extensive
damage. The supply tank and intake piping MUST be cleaned
and flushed prior to pump installation and operation.
LOCATION AND PIPING
Pump life and performance can be significantly reduced when
installed in an improperly designed system. Before starting the
layout and installation of the piping system, review the
following suggestions:
1. Locate the pump as near as possible to the source of
supply to avoid excessive inlet pipe friction.
2. The inlet line must be at least as large as the intake port on
the pump. Slope the piping downward to the pump, without
any upward loops. Eliminate restrictions such as sharp
bends; globe valves, unnecessary elbows, and undersized
strainers.
3. Install a system bypass valve that returns excess flow to
the supply tank or pump inlet piping as appropriate for the
pumping system. Insure that the bypass valve pressure
setting is appropriate for the pump and system component
working pressures.
4. It is recommended a strainer be installed in the inlet line to
protect the pump from foreign matter. Locate the strainer at
least 24" (0.6m) from the pump, and have a net open area
of at least four times the area of the intake piping. Strainers
must be cleaned regularly to avoid pump starvation.
5. The intake system must be free of air leaks.
6. Expansion joints, placed at least 36" (0.9m) from the pump,
will compensate for expansion and contraction of the pipes.
Contact the flexible connector/hose manufacturer for
required maintenance/care and design assistance in their
use.
7. Install pressure gauges in the 1/4” BSPP ports provided in
the pump casing to check pump at start up.
8. ALL piping and fittings MUST be properly supported to
prevent any piping loads from being placed on the pump.
9. Check alignment of pipes to pump to avoid strains which
might later cause misalignment. See Figure 1. Unbolt
flanges or break union joints. Pipes must not spring away
or drop down. After pump has been in operation for a
week or two, completely recheck alignment.
Figure 1
10. When pumping liquids at elevated temperature, make
provisions to compensate for expansion and contraction of
the pipes, especially when long pipe lines are necessary.
Steel pipe expands approximately 3/4” (1.9 cm) per 100
feet (30.49 m) per 100°F (37.8°C) rise in temperature.
PUMP MOUNTING
A solid foundation reduces noise and vibration, and will
improve pump performance. On permanent installations it is
recommended the pumping unit be secured by anchor bolts as
shown in Figure 2. This arrangement allows for slight shifting
of position to accommodate alignment with the mounting holes
in the base plate.
Figure 2 - Pipe Type
Anchor Bolt Box
For new foundations, it is suggested that the anchor bolts be
set in concrete. When pumps are to be located on existing
concrete floors, drill holes into the concrete to hold the anchor
bolts.
When installing units built on channel or structural steel type
bases, use care to avoid twisting the base out of shape when
anchor bolts are tightened. Use shims under the edges of the
base prior to tightening the anchor bolts to level the base and
prevent distortion.