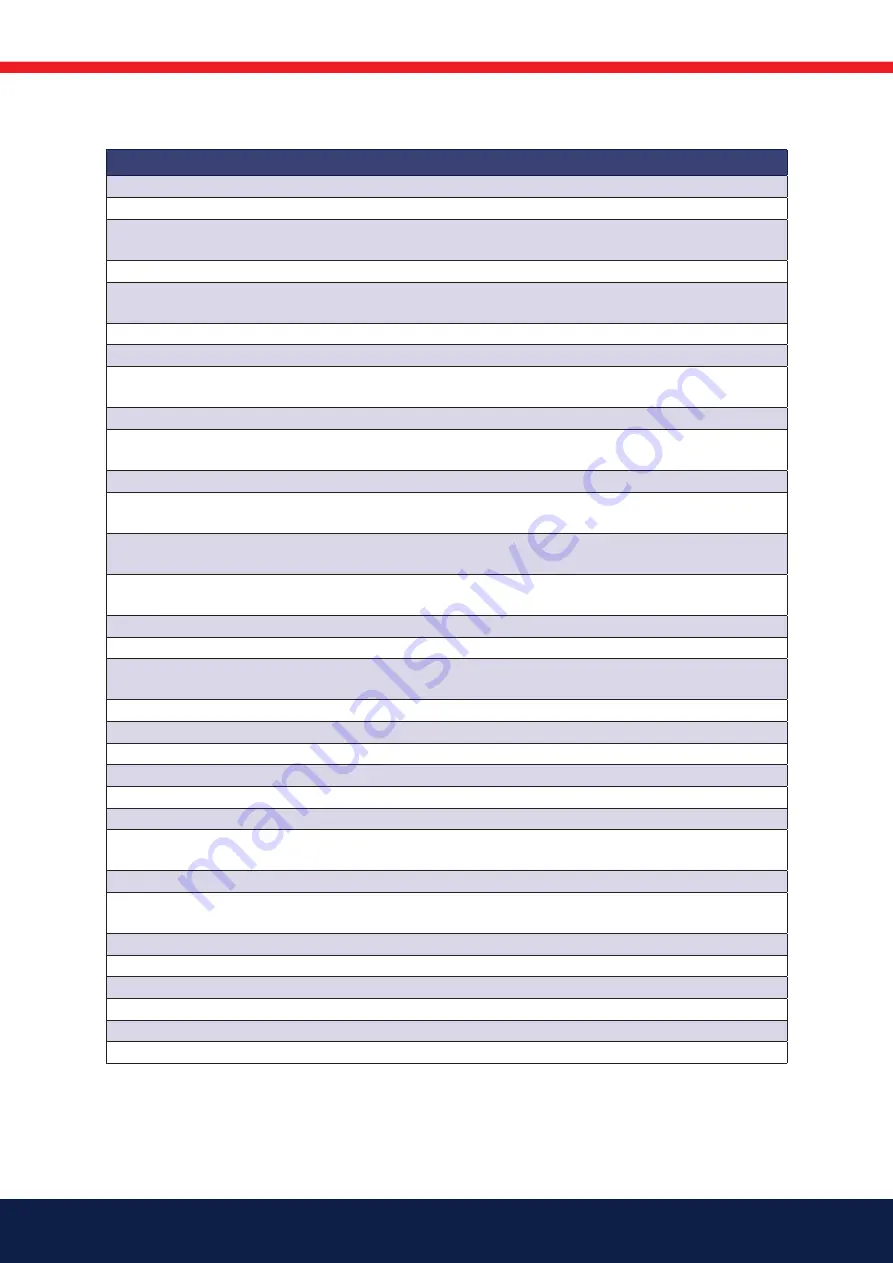
43
Bentone
Cause of fault
Action
Burner control faulty
Replace
Air pressure gauge incorrectly set or faulty
Check the settings and reset, or replace
No acknowledgement signal due to incorrect adjustment or
misalignment of the control motor cams.
Check the settings and realign.
Burner trips after safety time limit despite flame propagation
No ionisation current or UV cell incorrectly positioned
Adjust ionisation electrode and UV cell
Check cables and connectors
Burner control monitor faulty
Replace burner control
Voltage lower than 185 V
Contact an electrician
Ignition electrodes disrupting ionisation current
Adjust ignition electrodes. Re-polarise the
transformer
Poor earth connection
Ensure adequate earth connection
Phase and neutral swapped around
Check wiring diagram and change
accordingly
Burner trips during pre-aeration.
Air sensor faulty or incorrectly set
Increase/decrease air setting. Reduce air
volume
Ignition load incorrectly set
Increase/decrease gas supply Reduce
airflow
Gas pressure too low
Increase pressure. If necessary, contact gas
supplier
Pulsations at start-up
Ignition electrodes incorrectly set
Adjust
Gas pressure too high
Check and adjust using pressure gauge and
pressure control valve
Flue gas side blocked
Check the chimney flue
Burner pulsates during operation
Burner incorrectly set
Adjust
Burner dirty
Clean the burner
Incorrect chimney
Check and modify dimensions if necessary
Burner functioning properly but with occasional blockage
Ionisation current too low
Check. Must be at least 6 µA, but should
ideally lie between 8 and 20 µA
UV cell incorrectly positioned
Adjust
Voltage drop at certain times
Must not drop below 15% of rated voltage.
Contact an electrician if necessary
Incorrectly set or faulty air sensor
Check the settings and reset, or replace
Ignition electrode overload
Replace
Burner control ambient temperature too high
Insulate for heat, Max. 60 °
Ignition spark too weak
Check the transformer
Poor combustion
Poor draught conditions
Check the chimney
Содержание BG 650
Страница 2: ...2 Bentone...
Страница 19: ...19 Bentone 4 10 Gas nozzle 45 Natural gas Propan Biogas UV detector...
Страница 38: ...38 Bentone 9 2 Wiring diagram LME Design without A3 AGQ Option...
Страница 45: ...172 905 04 2018 02 15 12 EU Declaration of conformity Bentone Gasburners...
Страница 48: ...Enertech AB P O Box 309 SE 341 26 Ljungby www bentone se www bentone com...