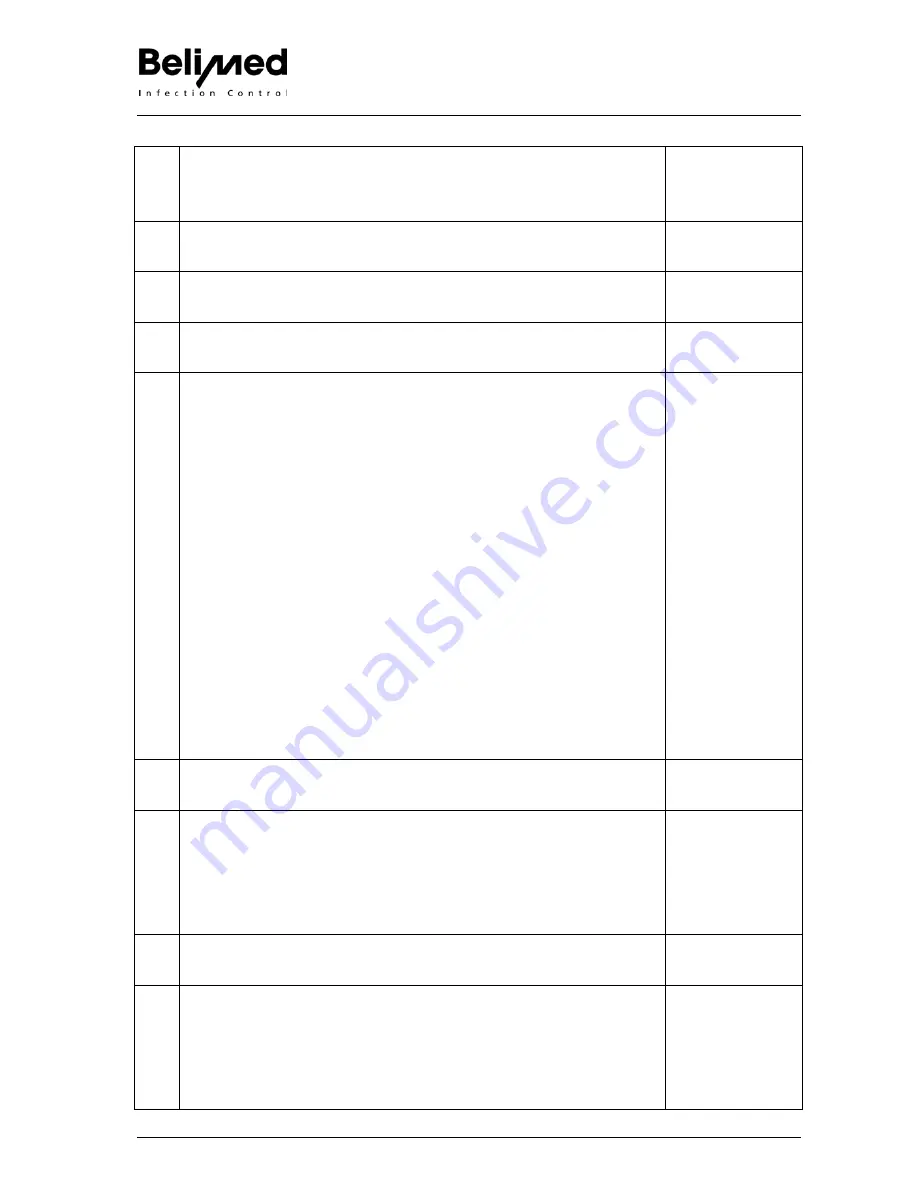
Operating Manual WD 425E
Rev. 1.
1
, LS Page 30 of 34
78563_E rev 1.1.doc
Dosing pump defective
Replace
Dosing pump clogged
Clean
IF DOSING PUMP BUTTON IS PRESSED, SYSTEM GOES TO ERROR MODE
152
As 151, but with flow meter 2
Improper dosing
D2
153
As 151, but with flow meter 3
Improper dosing
D3
154
As 151, but with flow meter 4
Improper dosing
D4
161
The temperature sensor in the wash chamber does not recognize any temperature change
during heating phase.
If minimal temperature change of 1°C within a predetermined period th (3 minutes) is de-
tected in the wash chamber (NTC 1) during heating phase, control system cuts running
program off under error indication. The same is the case if the target temperature is not
attained again attained within the holding phase th (3 minutes).
Monitoring of limit values: During heating phase with water.
Cause: Remedy:
Actuate heater contactor K16 with Control
(button 3), only while water is in tank
Safety temperature limiter
Check / reset
Heater contactor K 16 defective
Replace
Heater out of order
Replace
Cable connections are burned through
Replace connector
Drain valve leaks
Clean / replace membrane
Suction system has excessive suction
Reduce negative pressure
Exhaust damper remains open
Repair
No heat
Error code 161
161
Adjusting limit value
, minimal
water heating th.
1 – 6 Min., Default = 3 Min.
Delta Temp. NTC 1
3
Min.
162
The temperature sensor in the DI boiler does not detect any temperature change during
heating phase.
If during heating phase in the DI boiler (NTC 4) the minimal temperature change of 1°C
within a predetermined period thdi (5 minutes) is not detected, control system shuts down
current process under error indication.
Monitoring limit value: during heating and holding phase.
No heat
Error code 162
162
Adjustment of limit value, minimal water heating on DI boiler
thdi.
1 – 6 Min., Default = 5 Min.
Delta Temp. NTC 4
5
Min.
170
In left hand endoscope system during fill phase, test pressure of 280/ 230 mbar (2.74/ 2.34
V) is not reached within 10 minutes.
Cause:
Left hand endoscope or endoscope adapter or on system in machine, a significant leak has
been detected. The compressor or the test valves of the test block are defective. Pressure
sensor PL is defective.
Left Endo leaks
Error code 170