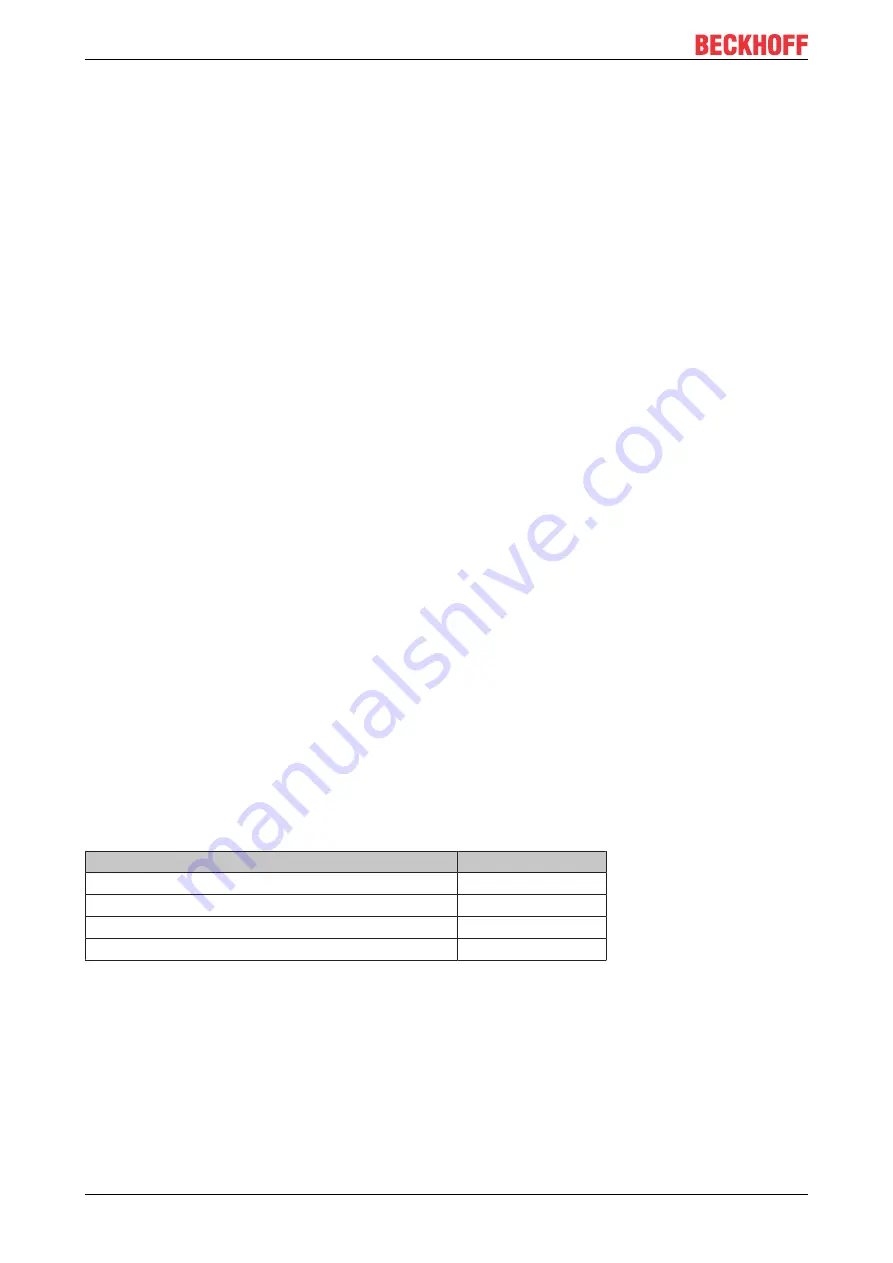
Electrical installation
Coreless linear motor AL3800
26
Version: 3.6
8.4
Calculation of the brake resistor
During the braking procedure of the linear axis, energy is fed back into the servo drive. During the design the
regenerative power must be calculated in order to select a brake resistor if necessary.
To do this the peak and continuous power must be calculated.
P
max
= 0.9 * (m * V²) / (2 t
b
)
P
rated
= P
max
* t
b
/ t
z
P
max
= maximum power of the brake resistor in Watts (W)
P
rated
= continuous power of the brake resistor in Watts (W)
M = moved mass (ca load) in kg
V = carriage velocity in m/s
t
b
= braking time in seconds
t
z
= cycle time in seconds
8.5
Temperature sensor
The coil unit is equipped with two temperature sensors, a PTC-1k and a NTC. The temperature sensors are
used to monitor the temperature in the coil unit. The temperature cable contains four wires.
8.5.1
PTC specification
The PTC-1k sensor exhibits a sharp rise in temperature when the temperature is close to a certain critical
value, and therefore operates as a digital indicator. A gradual temperature signal can, however, not be
generated from this PTC.
At room temperature, the PTC has an electrical resistance of around 65 ohms. As the temperature rises up
to a critical temperature, the resistance exhibits an almost linear rise up to 1000 ohms. Above this
temperature, the resistance rises exponentially. The switching resistance is therefore 1000 ohms. The servo
drive will immediately disconnect the power supply if this resistance is exceeded. This makes it possible to
guard against overheating the motor. The thermal protection contact cable must therefore be properly
connected to the servo drive.
Temperature
Resistance
Up to 20° C below the critical temperature
< 250 Ω
Up to 5° C below the critical temperature
< 550 Ω
Switching resistance
> 1000 Ω
Above the critical temperature
> 1330 Ω