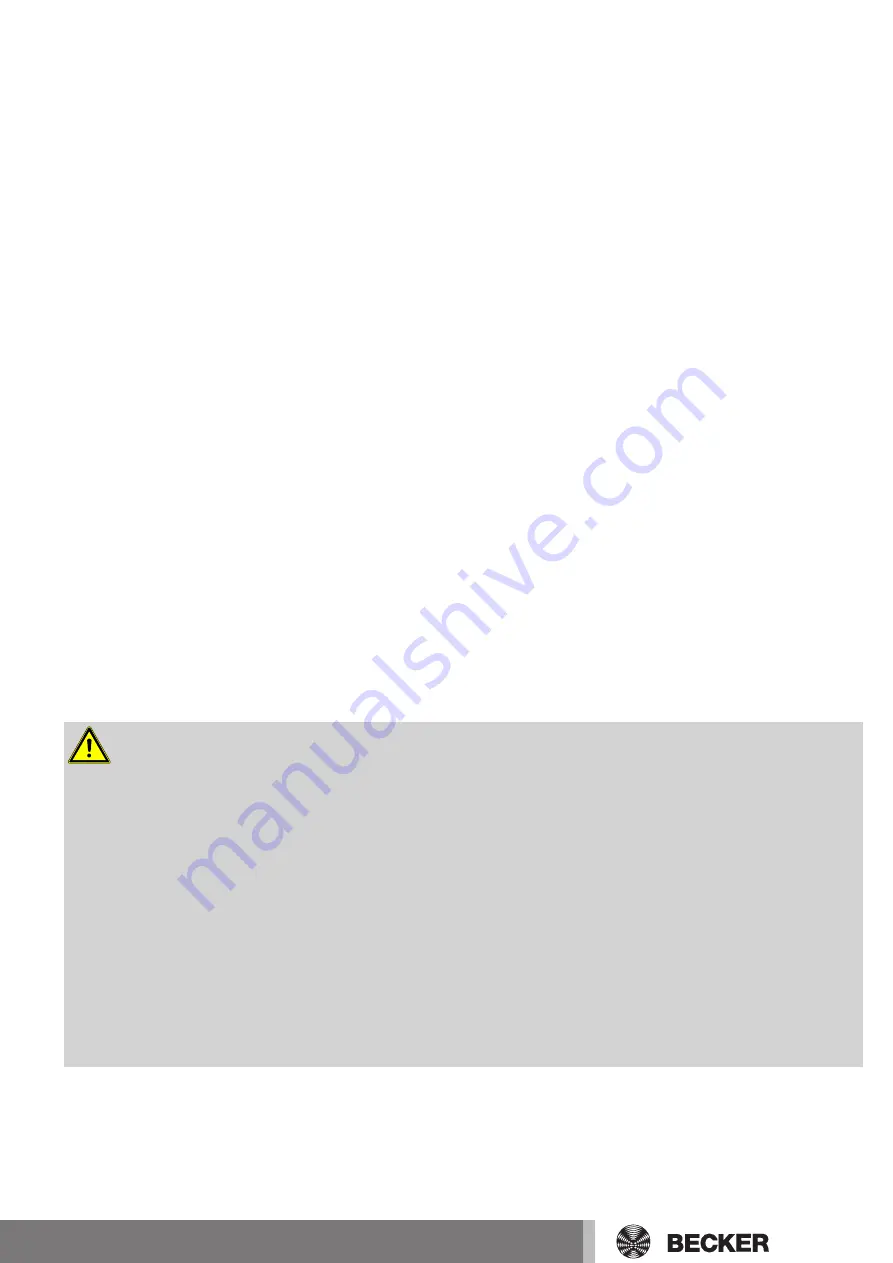
the drive manufacturer.
If any questions or uncertainties regarding the safety instructions contained in the standard arise,
please contact the manufacturer of the part or end product in question.
•
All applicable standards and regulations for electrical installation must be complied with.
•
All work, including maintenance and cleaning, on electrical installations as well as other system parts
must always be performed by authorised specialists, in particular qualified electricians.
•
Only use spare parts, tools and accessory devices which have been approved by the drive manufac-
turer.
Unapproved third-party products or modifications to the system and its accessories represent a risk to
your safety and the safety of others. This means that the use of unapproved third-party products, or
modifications which have not been agreed with or approved by us, are prohibited. We do not accept li-
ability for damage or injury arising from such actions.
•
Position control devices within sight of the driven product, but away from moving parts, at a height of
over 1.5 m.
•
Permanently mounted control devices must be positioned where they can be seen.
•
Rated torque and duty cycle must be suitable for the requirements of the driven product.
Technical data – rated torque and service life can be found on the type plate of the tubular drive.
•
Moving parts of drives must be installed at a height of over 2.5 m above floor level or any other surface
from which access to the drive is gained.
•
To ensure safe operation of the system after commissioning, the limit positions must be correctly set/
programmed in.
•
Drives with a H05VV-F connecting cable may only be used indoors.
•
Drives with a H05RR-F, S05RN-F or 05RN-F connecting cable may be used both indoors and outdoors.
•
To connect the drive to the driven part, solely mechanical accessory components made by the drive
manufacturer from the current product catalogue may be used. The components must be installed in
accordance with the manufacturer's instructions.
•
If the drive is used for shading solutions in a specially marked area (e.g. escape routes, hazard zones,
safety areas), compliance with all applicable regulations and standards must be ensured.
Caution
Safety instructions for avoiding serious injuries.
•
When electrical or electronic equipment and units are operated, certain components,
e.g., the power supply unit, are live. Physical injuries or damage to property can result in
the event of unauthorised interventions or failure to heed warnings.
•
Be careful when touching the tubular drive, as it heats up during operation for technolo-
gical reasons.
•
Before installation, shut down all lines and control devices that are not essential for op-
eration.
•
Crushing or shearing points must be avoided or protected.
•
When installing the drive, all-pole disconnection from the mains with a contact gap of at
least 3 mm per pole must be provided (EN 60335).
•
If the drive mains connecting cable is damaged, it must be replaced with the same type
of mains connecting cable, which is available from the drive manufacturer.
5
Содержание L120/11C PS(+)SMI
Страница 23: ...Declaration of conformity 23...
Страница 24: ......