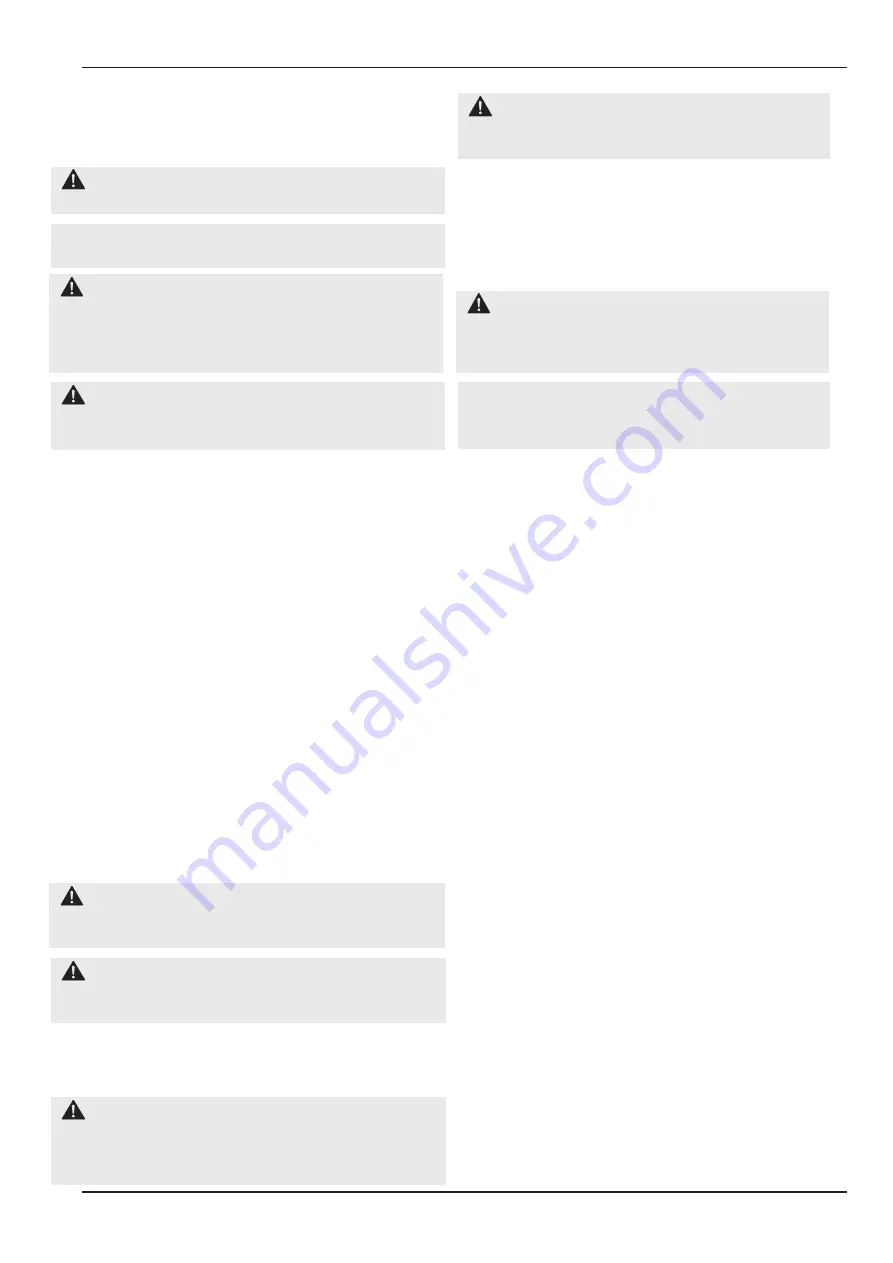
17
Manual Manifold
2006230.03
6.0 Component Replacement
Procedures
WARNING: IT IS ESSENTIAL THAT ONLY
GENUINE BEACONMEDÆS SPARE PARTS ARE FITTED
DURING MAINTENANCE.
CAUTION: Ensure no contaminates, oil
or grease come into contact with any of the gas
connection/internals.
6.1 Preparation For Component
Replacement
CAUTION: For primary manifolds ensure an
adequate backup supply is available and operating
correctly before taking the main supply off line for
maintenance.
5.3.7 To test the empty cylinder contact gauge close
the duty bank cylinder valves and observe the alarm
condition as the pressure drops.
I
MPORTANT! Open the cylinder valves on
the original duty bank once the test is completed.
Note - If there is no demand on the supply you can
simulate this by opening the test valve ‘C’.
WARNING: If venting gas from valve ‘C’, for
anaesthetic and oxygen manifolds ensure that the
manifold room is well ventilated and no potential
ignition sources are present while running this
test.
WARNING: This check may effect the
continuity of gas supply, ensure it is safe to carry
out this test before proceeding.
5.3.8 Finally, tighten all joints, and inspect with
suitable leak detection fluid.
5.3.9 Perform the steps in
section 4.2 - Procedure
to prime the control manifold
.
5.4 5 Years
Replace the pressure safety valve for a new certified
relief valve,
see section 6
. Replacement of the
regulators is also recommended at this time.
5.5 As Required
Replace tailpipes, pressure safety valve, pressure
regulator, high-pressure isolation valve, isolation
valves, contact gauges, non-return valve etc. as and
when required
(see section 6.0)
.
CAUTION: For emergency backup
manifolds ensure the main supply is functioning
correctly before taking off line for maintenance.
6.1.1 Close the manifold line isolation valve
‘A’
(See figure 8)
. Close all the cylinder isolation
valves.
6.1.2 Open the sampling outlet valve ‘C’, to
depressurise the system.
CAUTION: When exhausting anaesthetic
and oxygen manifolds ensure that the manifold
room is well ventilated and no potential ignition
sources are present.
Note - If the cylinder contents gauges are not
rapidly falling in pressure, stop draining the system
and check all cylinders are correctly isolated.
6.2 Replace line non-return
valve (P/N: 2005951)
6.2.1 Complete steps in
section 6.1
before
carrying out any component replacement on the
manifold control panel.
6.2.2 Slowly turn the swivel nut of the top 1”
connection. If you hear gas escaping do not fully
unscrew the joint until the system is fully drained.
6.2.3 Fully disconnect all three joints as shown in
figure 11
and gently remove the unit by sliding it
towards you. Take care not to damage the seals.
6.2.4 Inspect the existing seals and replace if
required,
see figure 11
for seal part numbers.
6.2.5 Taking care not to damage the O-ring seals
replace the new non-return valve as shown in
figure 11
, and fasten the 3 flat face joints.
6.2.6 Disconnect the test point valve from the
original non-return manifold and fit to the new
unit.
6.2.7 Follow steps in
section 6.11
to bring the
manifold back online.