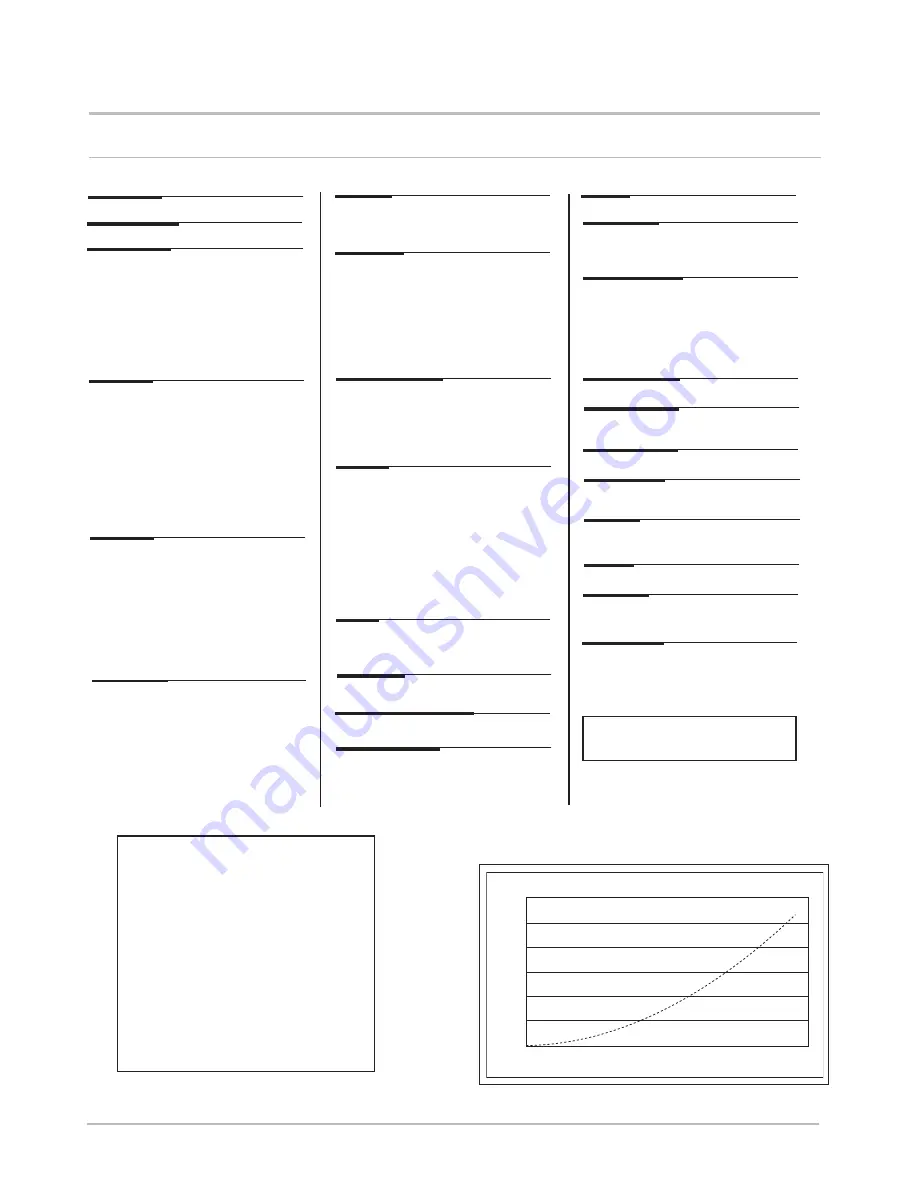
14
EcoBlue Heat
3
Technical Specification
7219717 - 02 (08/15)
3
Technical Specifications
3.1
Technical Data
NOTE:
All data in this section are nominal
values and subject to normal production
tolerances.
Appliance Category
CAT I
2H
Horizontal
Flue Terminal
Diameter 100mm
Dimensions
Projection 125mm
Outercase Dimensions
Overall Height
Inc Flue Elbow
- 790mm
Casing Height - 625mm
Casing Width - 370mm
Casing Depth - 270mm
Connections
Gas Supply - 22mm
Central Heating Flow
(compression fitting) - 22mm
Central Heating Return
(compression fitting)
- 22mm
Condensate Drain - for 21.5mm
plastic waste pipe
Recommended System
Temperature Drop
Condensing 20°C
Heat Input Qn Hs (
Gross)
Max Min
12 model kW 14.88 8.59
15 model kW 18.32 8.59
18 model kW 21.75 8.59
21 model kW 24.04 8.59
24 model kW 28.62 8.59
Heat Output Pn
(Non Condensing 70° C Mean Water
Temp)
Max Min
12 model kW 13 7.5
15 model kW 16 7.5
18 model kW 19 7.5
21 model kW 21 7.5
24 model kW 25 7.5
Electrical Supply
230V~ 50Hz
(Appliance must be connected to an
earthed supply)
Power Consumption Max Rate
12 model W 17
15 model W 20
18 model W 23
21 model W 25
24 model W 33
External Fuse Rating
3A
Internal Fuse Rating
(Terminal Strip)
Fuse 1.6T
Appliance Type
C
13
C
33
C
53
Nox Class
5
Water Content
litres 1.7
Static Head
max 25 metres
Low Head
0.4m min
System Detail
fully pumped open vented & sealed systems
Electrical Protection
IPX4D
CO/CO2 Ratio
Up to a maximum
of 0.004
Flow Temperature
(adjustable)
30° C to 80° C (± 5° C)
Max Gas Rate
(Natural Gas - G20)
(After 10 Mins)
m
3
/hr
12 model 1.42
15 model 1.75
18 model 2.07
21 model 2.29
24 model 2.73
Pressure Switch
12/15/18 Model - Not Fitted
21/24 Model - Fitted
300
250
200
150
100
50
0
0.0
0.2
0.4
0.6
0.8
1.0
1.2
1.4
1.6
1.8
Flow (m
3
hr)
Pressure drop vs Flow
Pressure drop (mbar)
Clearances
Both Sides 5mm Min
Above Casing
(Top Flue)
19 0mm Min
Above Casing
(Rear Flue)
35mm Min
Below Casing
(in Cupboard)
35mm Min
Below Casing 120 mm Min
Front (For Servicing) 500mm Min
Front (In Operation) 5mm Min
See Section 5.3.6 for full details !
Weights
Packaged Boiler Carton 21.5 kg
Installation Lift Weight 19.5 kg
Dynamic (nominal) Inlet Pressure
(Natural Gas - G20)
mbar 20
with a CV of 37.78 MJ/m
3
SAP 2009 Annual Efficiency
12 model - 89.2% 21 model - 89.2%
15 model - 89.2% 24 model - 89.1%
18 model - 89.2%
This value is used in the UK Government’s Standard
Assessment Procedure (SAP) for energy rating of
dwellings. The test data from which it has been
calculated has been certified by 0063.
Product Characteristics Database
(SEDBUK)