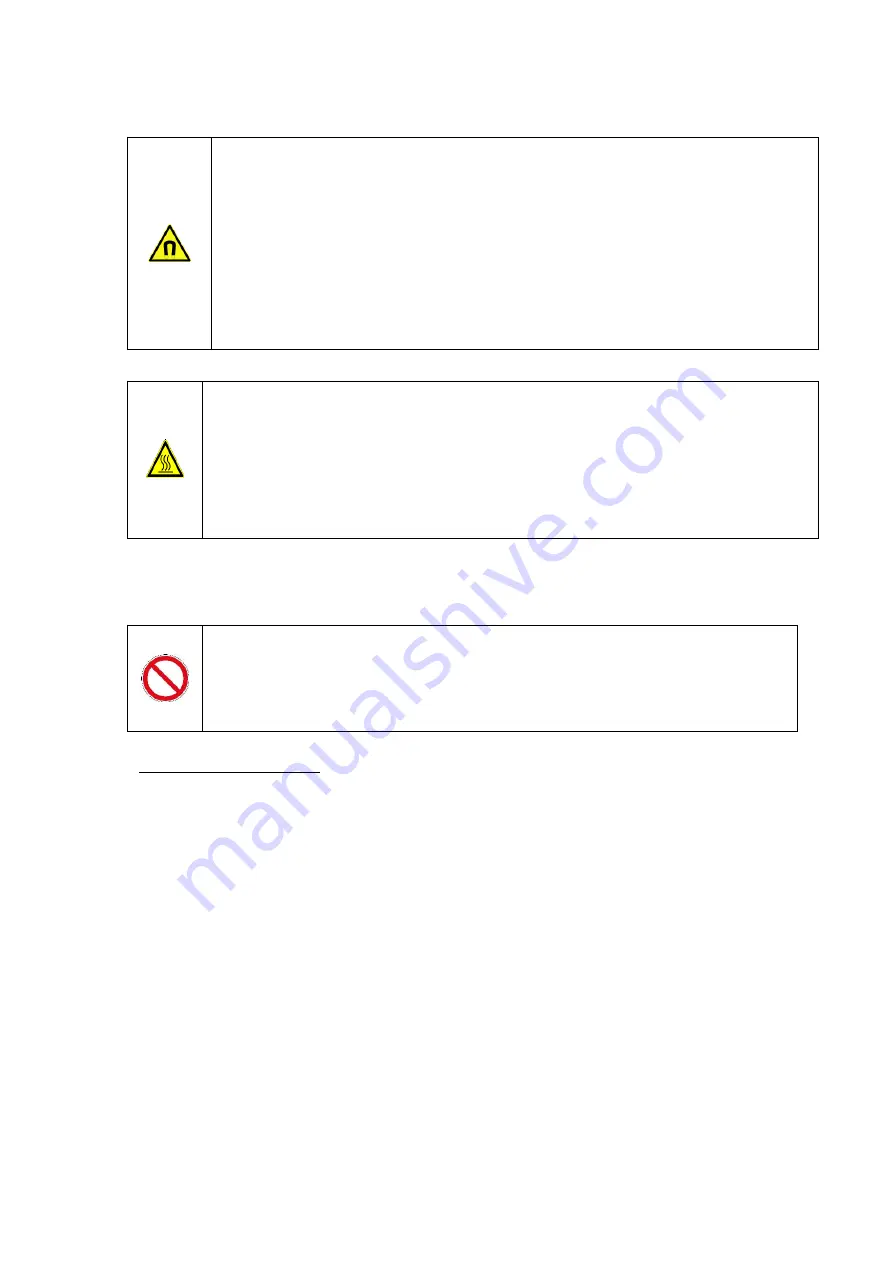
TAM 00695
6
DST2-135
– 400 W
10 / 2019
Three-phase synchronous motor, water-cooled
English
Motor design with rare-earth magnets:
Please be aware of the following risks in the vicinity of a retracted or exposed rotor with
a strong magnetic field:
People with electronic or metallic implants (e. g. cardiac pacemakers, hearing aids,
plates or pins) are at risk, if the distance between the implant and the magnetic
pole is less than 0.5 m.
Due to the strong attraction forces exerted on ferromagnetic parts there is a risk of:
o
Crushinginjuries
o
Damage to measuring and assembly tools, credit cards, watches etc.
o
Contamination of the rotor assembly due to attracting metal debris or powder
Thermal hazards:
Caution! Highly inflammable!
Temperatures of
over 70 °C
can build up on the motor surfaces. Touch contact measures
should be implemented if necessary!
Temperature-sensitive parts, e.g. normal cables or electronic components, must not be
placed on or fixed to the hot surfaces.
Thermal overloading can destroy the winding and the bearing. A thermal sensor should
be used to monitor the temperature.
1.3
Prohibition of unauthorised modifications and changes
For safety reasons, unauthorised modifications and changes to the electric motor are
not permitted. If such modifications / changes are necessary, please contact the
manufacturer.
No safety devices may be dismantled or decommissioned prior to the operation of the
device.
2
Operating conditions
2.1
Product description
Electric motors of the series
“DST2…W”
are permanently excited, high-pole, three-phase
synchronous motors with rare-earth magnets.
An innovative motor concept with integrated liquid cooling (water-based coolant) ensures a high
torque density at low and medium speeds and a robust and compact design.
The elimination of the fan unit significantly reduces noise emission and provides for a high level of
protection. In connection with the low-maintenance motor design, these motors are ideally suited
for direct drive applications with production machines (e.g. printing presses, extruders, injection
molding machines etc.).
Thrust-bearing motors: Thanks to the integration of an axial thrust bearing turning in oil, very high
return pressures, e.g. such as those that occur in extrusion, can be taken up by the motor shaft.
This makes the low-maintenance motors the best for use as a direct drive for production machines
(e.g. extruders etc.).
Moreover, when operating with a motor-controlled pulse converter, the speed and position of these
compact motors can be optimally controlled. These drives have a high overload capacity and are
therefore ideally suited for applications in mechanical engineering.