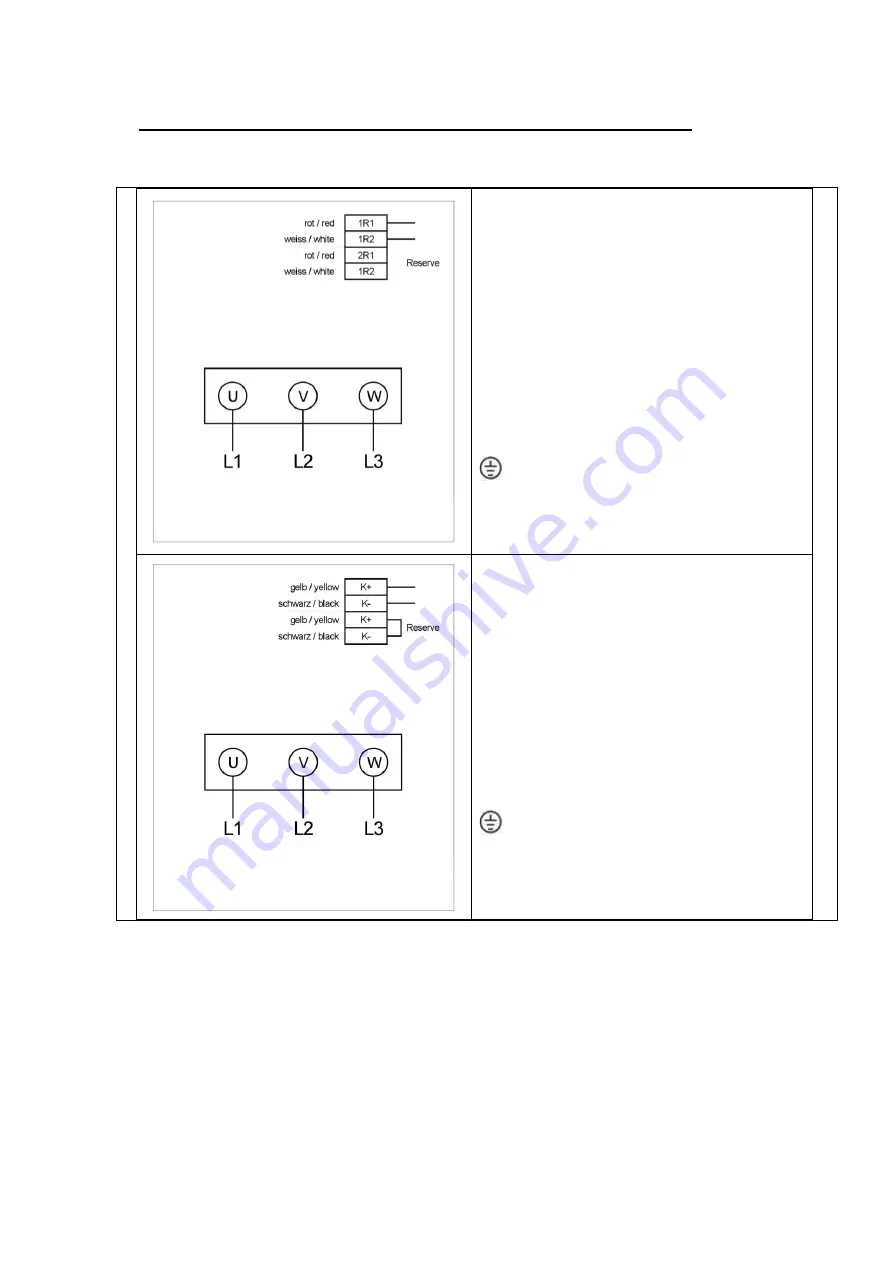
TAM 00695
21
DST2-135
– 400 W
10 / 2019
Three-phase synchronous motor, water-cooled
English
7
Appendix 1: pole assignment (main connection and control port)
7.1 Main connection with terminal box
U V W
Power connection
1R1/ 1R2
1R1/ 1R2
Temperature sensor (PT1000)
Temperature sensor Reserve
Protection
U V W
Power connection
K + K -
Temperature sensor
(KTY 84)
(Reserve gebrückt)
Attention:
When connecting the temperature sensor KTY
84 the polarity must be considered.
Please,
observe the safety notes in Chapter 3.4
Protection
Figure 2: Main connection with terminal box
The cable inlets of the terminal boxes and the main connection terminals are listed below together
with the permitted tightening torque.
We recommend EMC screwed fittings for the cable inlets.
It is recommended when tightening the terminal screw to support against the conductor to prevent
mounting rail deformation and to keep the terminal base free of torsional forces.
Please refer to the
Technical Product list DST2-135 - 400 W
for the size of the cable glands and
terminals.