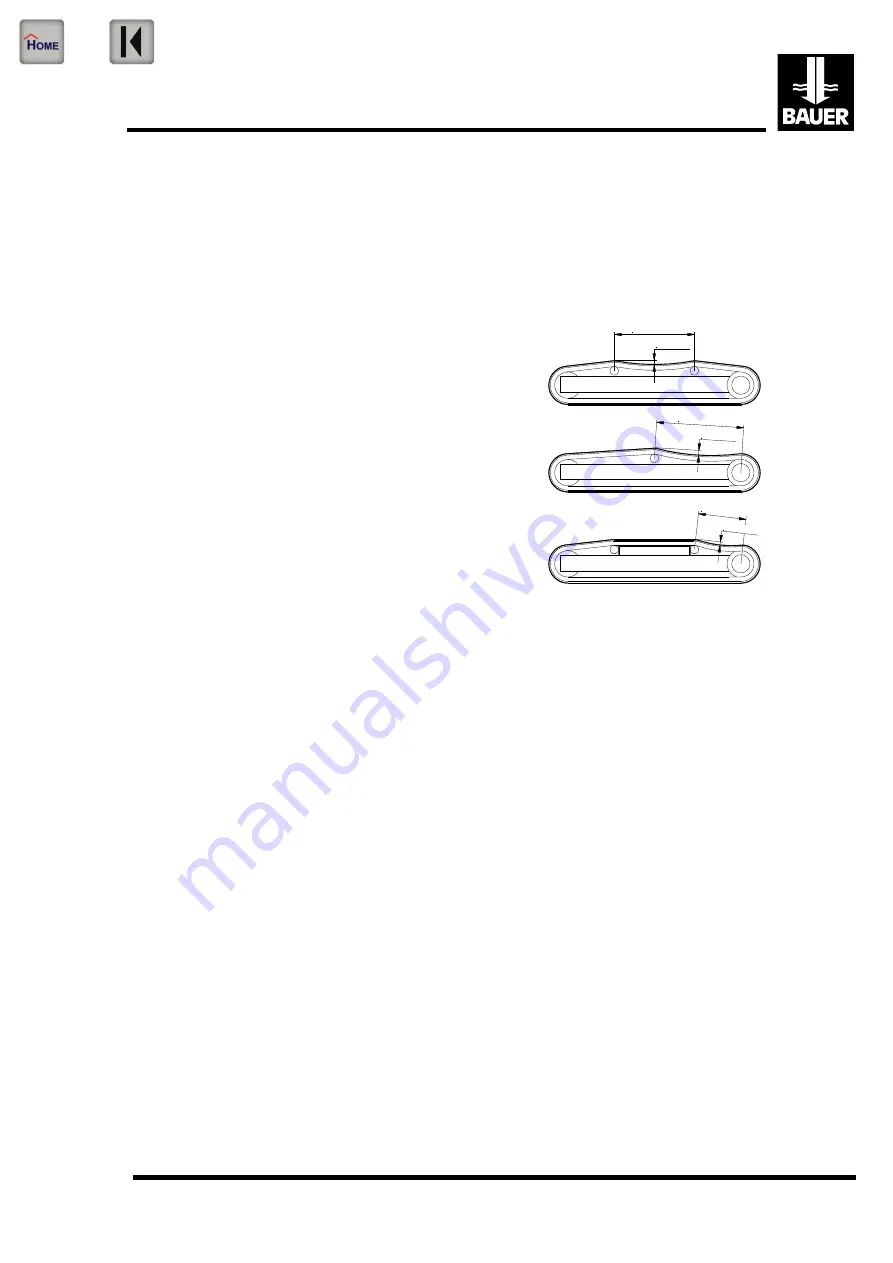
MAINTENANCE
BG 25 / 2011 /
2254_BG25_en_0000498763_V01
9 - 42
9.11.2
Crawler Tracks
9.11.2.1 To Check the Track Tension
Check track tension every 10 operating hours or daily.
Thoroughly clean each crawler, track
and rollers.
Travel forward a bit with the machine
and then park it.
Using a straight rod, measure the sag
of 1 - 1.5 m length of track in midway
(see fig.): The distance from the rod to
the track should be approx. 2
– 3 cm.
Otherwise, the track tension must be
readjusted.
2-3 cm
1 - 1,5 m
2-3 cm
1 - 1,5 m
2-3 cm
1 - 1,5 m
B0000680.wmf