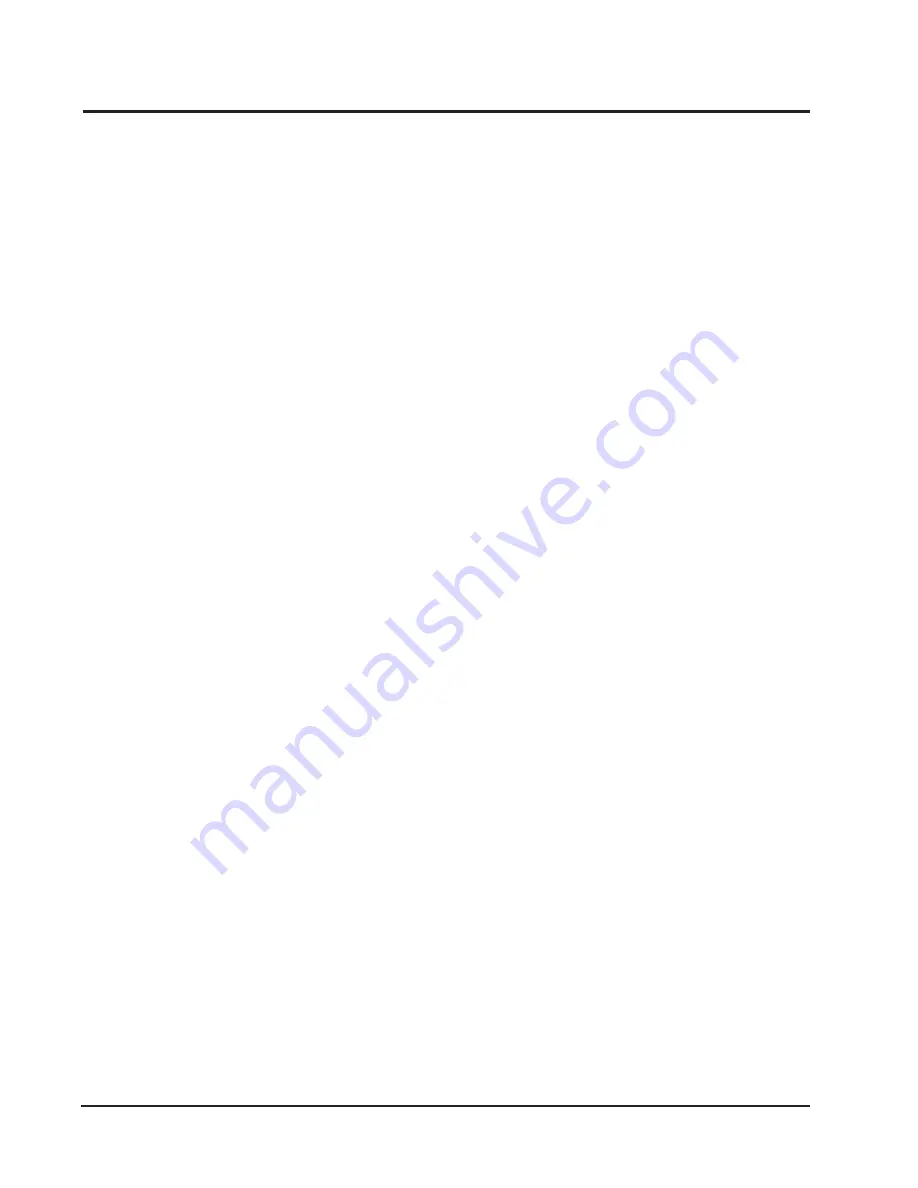
Manual 2100-384B
Page
8 of 19
INSTALLATION INSTRUCTIONS
WALL MOUNTING INFORMATION
1. These units are secured by wall mounting brackets
which secure the unit to the outside wall surface at
both sides.
2. On wood frame walls, the wall construction must be
strong and rigid enough to carry the weight of the
unit without transmitting any unit vibration.
3. Concrete block walls must be thoroughly inspected
to insure that they are capable of carrying the
weight of the installed unit.
PROPER UNIT PLACEMENT
Refer to Technical Bulletin TB01-4 “Wall Mount
Equipment Clearance for Proper Operation”. This
bulletin will provide information concerning the
placement of units as to clearance between dual unit
installation (mounted on common wall) of units
discharging against a wall, or essentially solid barrier,
and units discharging against opposing (facing) units.
MOUNTING THE UNIT
1. Two holes, for the supply and return air openings,
must be cut through the wall as shown in Figure 4.
NOTE: If the combination SUPPLY / RETURN Grille
Assembly model CSRG-1 is to be used in
conjunction with this unit a different size wall
opening is required. See Figure 3.
2. Locate and mark lab bolt locations and bottom
mounting bracket location, if desired. See Figure 4.
3. Hook top rain flashing under back bend of top. Top
rain flashing is shipped attached to the back of the
unit on the right side.
4. Position unit in opening and secure with 5/16 lag
bolts; use 7/8 inch diameter flat washers on the lab
bolts.
5. Secure rain flashing to wall and caulk across entire
length of top. See Figures 3 and 4.
6. For additional mounting rigidity, the return air and
supply air frames or collars can be drilled and
screwed or welded to the structural wall itself
(depending upon wall construction). Be sure to
observe required clearance if combustible wall.
7. On side-by-side installations, maintain a minimum
of 20 inches clearance on right side to allow access
to control panel and allow proper airflow to outdoor
coil. Additional clearance may be required to meet
local or national codes.