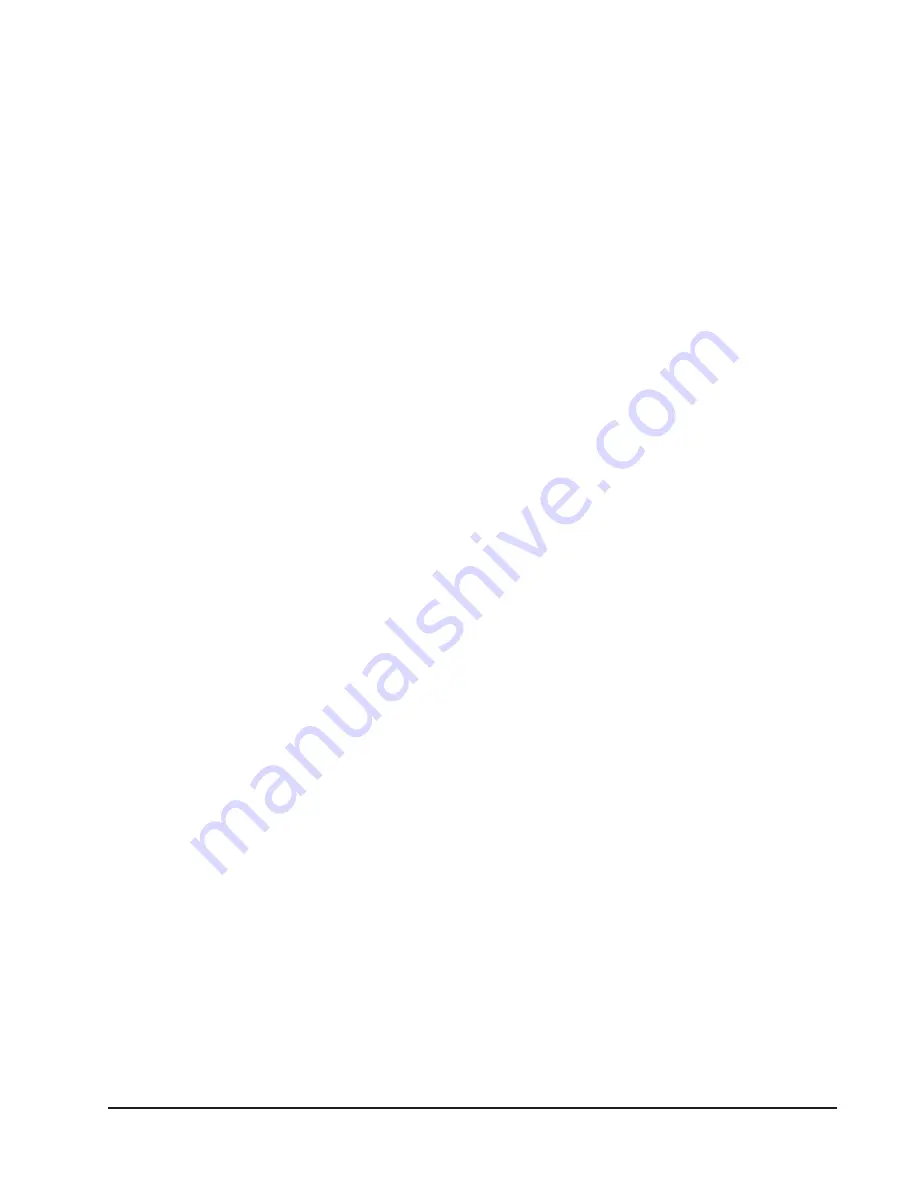
Manual
2100-549G
Page
49 of 59
ENERGY RECOVERY VENTILATOR
MAINTENANCE
GENERAL INFORMATION
The ability to clean exposed surfaces within air moving
systems is an important design consideration for the
maintenance of system performance and air quality.
The need for periodic cleaning will be a function of
operating schedule, climate, and contaminants in the
indoor air being exhausted and in the outdoor air being
supplied to the building. All components exposed to the
airstream, including energy recovery wheels, may
require cleaning in most applications.
Rotary counterflow heat exchanges (heat wheels) with
laminar airflow are “self-cleaning” with respect to dry
particles. Smaller particles pass through; larger
particles land on the surface and are blown clear as the
flow direction is reversed. For this reason, the primary
need for cleaning is to remove films of oil-based
aerosols that have condensed on energy transfer
surfaces. Buildup of material over time may eventually
reduce airflow. Most importantly, in the case of
desiccant coated (enthalpy) wheels, such films can close
off micron sized pores at the surface of the desiccant
material, reducing the efficiency with which the
desiccant can absorb and desorb moisture.
FREQUENCY
In a reasonably clean indoor environment such as a
school, office building, or home, experience shows that
reductions of airflow or loss of sensible (temperature)
effectiveness may not occur for ten or more years.
However, experience also shows that measurable
changes in latent energy (water vapor) transfer can occur
in shorter periods of time in commercial, institutional
and residential applications experiencing moderate
occupant smoking or with cooking facilities. In
applications experiencing unusually high levels of
occupant smoking, such as smoking lounges, nightclubs,
bars and restaurants, washing of energy transfer
surfaces, as frequently as every six months, may be
necessary to maintain latent transfer efficiency. Similar
washing cycles may also be appropriate for industrial
applications involving the ventilation of high levels of
smoke or oil-based aerosols such as those found in
welding or machining operations, for example. In these
applications, latent efficiency losses of as much as 40%
or more may develop over a period of one to three years.
CLEANABILITY AND PERFORMANCE
In order to maintain energy recovery ventilation
systems, energy transfer surfaces must be accessible for
washing to remove oils, grease, tars and dirt that can
impede performance or generate odors. Washing of the
desiccant surfaces is required to remove contaminate
buildups that can reduce adsorption of water molecules.
The continued ability of an enthalpy wheel to transfer
latent energy depends upon the permanence of the bond
between the desiccant and the energy transfer surfaces.
Bard wheels feature silica gel desiccant permanently
bonded to the heat exchange surface without adhesives;
the desiccant will not be lost in the washing process.
Proper cleaning of the Bard energy recovery wheel will
restore latent effectiveness to near original performance.
MAINTENANCE PROCEDURES
NOTE: Local conditions can vary and affect the required time
between routine maintenance procedures, therefore all
sites (or specific units at a site) may not have the same
schedule to maintain acceptable performance. The
following timetables are recommended and can be
altered based on local experience.
QUARTERLY MAINTENANCE
1.
Inspect mist eliminator/prefilter and clean if
necessary. This filter is located in the fresh air
intake hood on the front of the unit. This is an
aluminum mesh filter and can be cleaned with
water and any detergent not harmful to aluminum.
2.
Inspect wall mount unit filter and clean or replace
as necessary. This filter is located either in the unit,
in a return air filter grille assembly, or both. If in
the unit it can be accessed by removing the lower
service door on the front of the unit. If in a return
air filter grille, by hinging the grille open to gain
access.
3.
Inspect energy recovery ventilator for proper wheel
rotation and dirt buildup. This can be done in
conjunction with Item 2 above. Energize the energy
recovery ventilator after inspecting the filter and
observe for proper rotation and/or dirt buildup.
4.
Recommended energy recovery wheel cleaning
procedures follow Steps 5 through 8.
5.
Disconnect all power to unit. Remove the lower
service door of the wall mount unit to gain access to
the energy recovery ventilator.
6.
Remove the front access panel on the ventilator.
Unplug amp connectors to cassette motors. Slide
energy recovery cassette out of ventilator.
7.
Use a shop vacuum with brush attachment to clean
both sides of the energy recovery wheels.
8.
Reverse shop vacuum to use as a blower and blow
out any residual dry debris from the wheel.
NOTE: Discoloration and staining of the wheel
does not affect its performance. Only
excessive buildup of foreign material needs
to be removed.
9.
If any belt chirping or squealing noise is present,
apply a small amount of LPS-1 or equivalent dry
film lubricant to the belt.