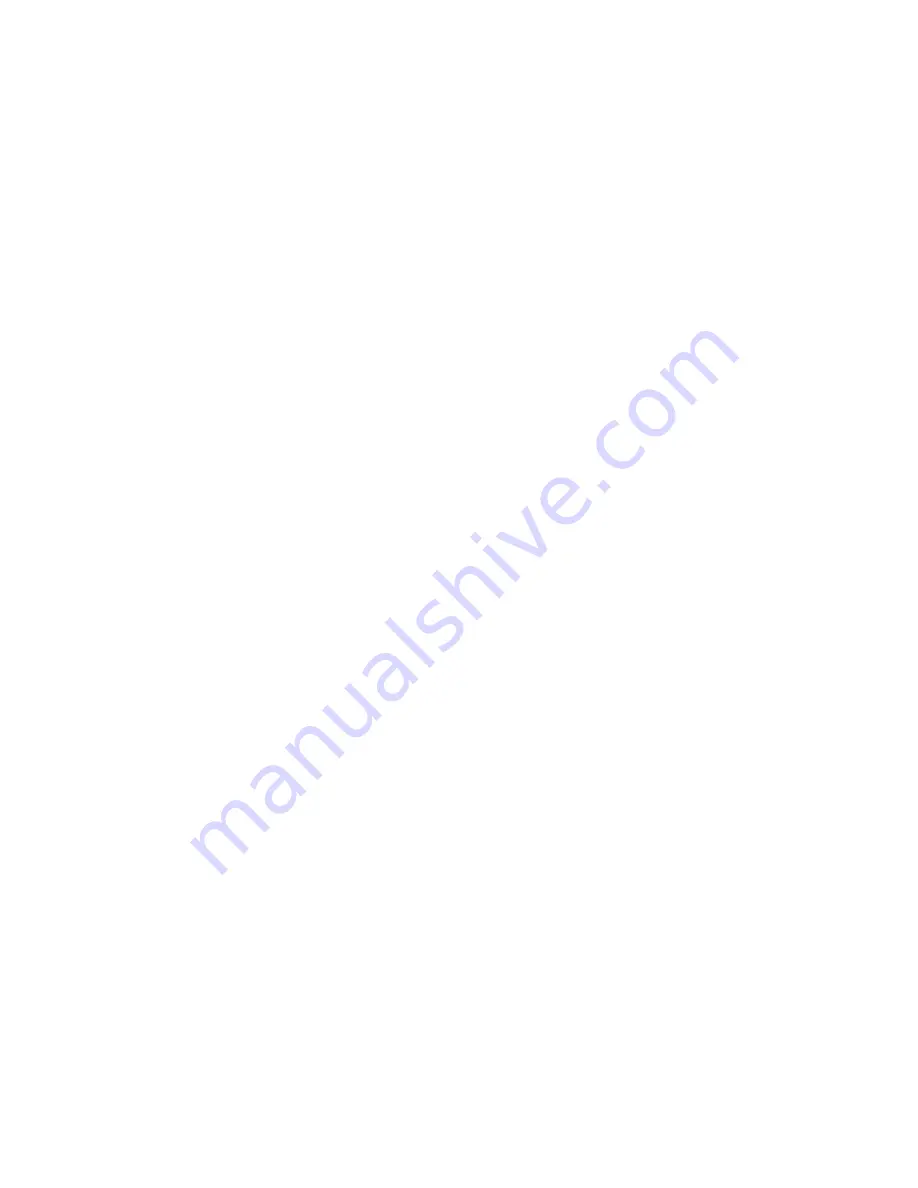
1. Each month or after every 200 hours of operation, lubricate bearing and seals. See instruc-
tions on the machine.
(a) Use a premium grade lithium complex grease. Never mix two types of grease.
(b) Pump the grease gun slowly, permitting only the following number of strokes:
(c) Each bearing grease fitting, 2 strokes
Do not pump the grease gun if grease comes out of the bearing housing. This can result in
over lubrication, causing damage to bearings and seals.
2. If the machine is provided with automatic lubricators, check that they are injecting grease.
Normally they last for approximately one year - less for larger machines or if the laundry
is operating on more than one shift (see TSB016 for details). Mark new lubricators with
installation date.
3. Clean the AC drive fins:
(a) Remove the AC drive box cover.
(b) Blow the fins clean using compressed air at a pressure of 60- 90 psi (4-6 Bar) or by using
canned compressed air. Use care to avoid damaging cooling fan or other components.
NOTE: No amount of visible foreign matter should be allowed to accumulate on fins, finger
guard, cooling fan or fan filter. Replace damaged fan filters.
4. Use the following procedures to determine if V-belts require replacement or adjustment. Call
a qualified service technician in either case.
(a) Check V-belts for uneven wear and frayed edges.
(b) After disconnecting power to the machine and removing all panels necessary for access
to the drive belts, use the following method to verify that the V-belts are properly ten-
sioned. Belt deflection should be measured as close to the center of the span length as
possible. A set force should be applied in the center of the length, as specified in the ta-
ble below. Belt tension is adjusted by turning the set screw on the idler pulley. Turning
the set screw clockwise tighten the belt, and vice versa. Refer to figures 7.4, 7.1 and 7.5
on pages 47 and 48.
(c) Verify that V-belts are properly aligned by checking pulley alignment. Place a straight-
edge across both pulley faces. The straight edge should make contact with the pulleys
in four places. See figure 7.4 on page 47.
5. Verify that air pressure regulators are set to the correct values: No more than 15 PSI (1 bar) on
the door gasket, and no more than 60 PSI (4 bar) on the tilt regulator located on the interior
of the machine on the rear electrical enclosure.
6. Verify that the hydraulic pressure does not exceed 200 psi on models with only the hydraulic
door assist and 750psi on models with the hydraulic door assist and hydraulic loading chute
options during operation. The gauge is mounted on the pump, just inside the frontmost
right side panel. See figure 7.1 on page 45 for the hydraulic door only models and figure
7.2 on page 46 for models with the loading chute. If pump pressure is incorrect, adjust using
44
Содержание SI Series
Страница 1: ...Washer Extractor SI Series Installation and Operation Manual 9 Sep 2013 Revision 2 20 ...
Страница 6: ...Figure 1 1 SI Product Family 2 ...
Страница 14: ...Chapter 4 General Specifications 10 ...
Страница 15: ...Figure 4 1 SI Series General Specifications 11 ...
Страница 33: ...Figure 5 9 Loading Chute Installation 29 ...
Страница 34: ...Figure 5 10 Loading Chute Up Switch Installation 30 ...
Страница 40: ...Figure 6 2 Chute Maintenance Switch 36 ...
Страница 50: ...Figure 7 2 Hydraulic Pump Detail for models with Loading Chute Option Figure 7 3 Hydraulic Pump Adjustment 46 ...