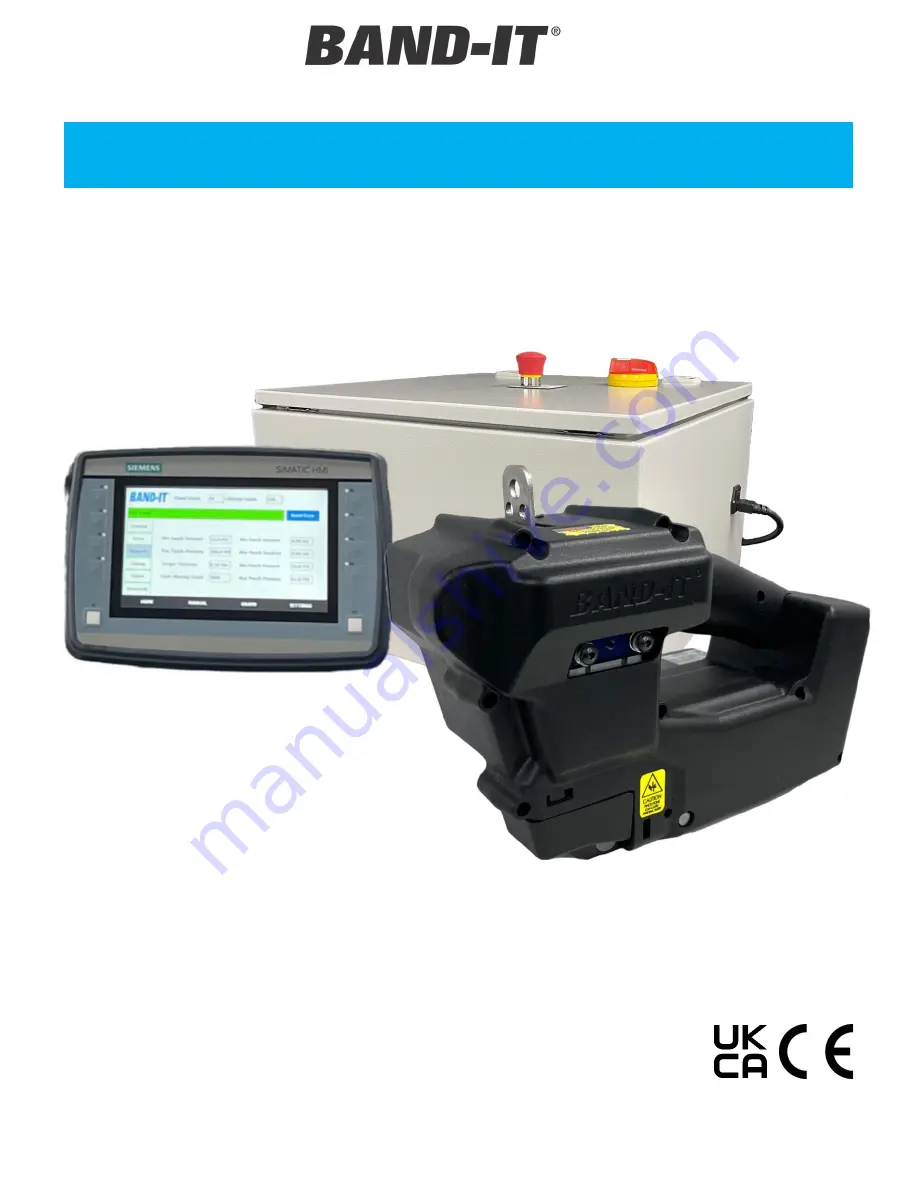
1
User Manual
IT8000 3/8” TIE
-LOK DATA TOOL
IT7000 1/4” TIE
-LOK DATA TOOL
ITC800 CONTROL SYSTEM
Document # P80080 Rev. C.3
© Copyright
BAND-IT-IDEX, Inc. 2024
All rights reserved
All rights reserved
BAND-IT-IDEX, Inc.
A Unit of IDEX Corporation
4799 Dahlia Street
Denver, CO 80216-3070 USA
P: 1-800-525-0758
IT8000/IT7000/ITC800
User Manual
Original Instructions
(Not a translation)