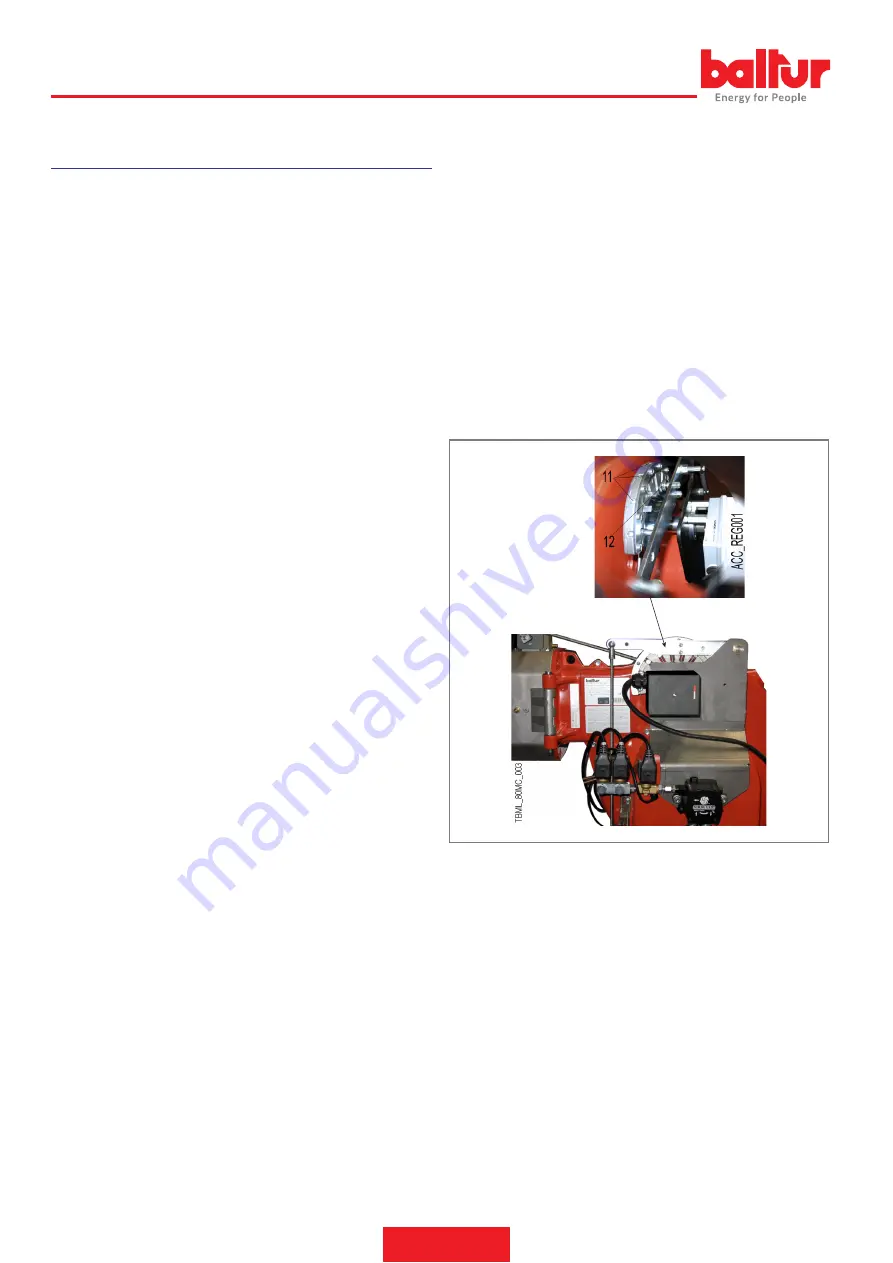
NATURAL GAS IGNITION AND RE-
GULATION
f
irSt
ignition
poWer
adjuStment
•
Now turn on the burner panel switch START/STOP switch. The
control equipment is powered and the programmer activates the
burner as described in the chapter “Operation description”. During
pre-ventilation, make sure that the air pressure switch changes
its status. If the air pressure switch does not detect sufficient
pressure, the ignition transformer is not switched on, nor are the
gas valves, therefore the equipment “locks out”.
•
During the first ignition several “lock outs” may occur due to the
following reasons:
•
The gas piping has not been bled from air correctly and so there
is not enough gas to provide a stable flame.
•
A “lock out” with flame presence could be caused by flame
instability due to an incorrect air/gas ratio. This can be solved
by changing the amount of air and/or gas supplied, so as to find
the right ratio. The same problem may be caused by incorrect
air/gas distribution in the combustion head. This can be solved
through the combustion head adjustment device, by closing or
opening further the air passage between combustion head and
gas diffuser.
•
Correct the air flow in first stage using the screw(s) (11) corre
-
sponding to the bearing (12).
Clockwise rotation increases air flow rate;
In anticlockwise rotation the air flow decreases
S
econd
Stage
poWer
regulation
.
•
After adjusting the regulation for the first ignition, turn off the
burner and close the electrical circuit commanding inclusion of the
second stage.
•
Check that the electric servomotor second stage
gas flow rate regulation cam is positioned on
130°.
•
Switch the burner on again activating the main switch (1) on
the synoptic panel. The burner will switch on automatically and
activate the second stage. With the aid of appropriate instrumen
-
ts, attend to the regulation of the air and gas flow according to the
procedures subsequently described:
•
To regulate the gas flow operate the valve pressure regulator.
Consult the instructions related to the single stage gas valve
model installed.Avoid keeping the burner running if the heating
capacity is greater than the maximum amount allowed for the
boiler, to avoid damaging it.
•
Check the combustion parameters with appropriate instruments
(CO2 MAX=10% O2 MIN= 3% CO MAX=0.1%)
f
irSt
Stage
poWer
regulation
After regulation of the burner in the second stage, return the burner
to the first stage. Set the switch on the printed circuit to the 1st stage
position without varying the adjustment of the gas valve already per
-
formed previously.
•
Set the first stage gas flow rate to the needed value, as described
above.
•
Adjust the gas flow in the 1st stage to the desired value using the
electric servomotor.
•
If necessary, correct the combustion air supply adjusting the
screw(s) (11) as described previously.
•
Check the combustion parameters in the 1st stage with appropria
-
te instruments (CO2 MAX=10% O2 MIN= 3% CO MAX=0.1%)
• The air pressure switch prevents the opening of the gas valves
if the air pressure is not the foreseen one. The pressure switch
must therefore be adjusted to intervene closing the contact when
the air pressure in the burner reaches a sufficient value. If the
air pressure switch does not detect a pressure greater than that
calibrated, the equipment runs through its cycle but does not swi
-
tch on the ignition transformer and does not open the gas valves
and so the burner “locks-out”. To ensure correct working of the air
pressure switch, you must,
with burner on and with first
flame only
, increase the regulation until it is triggered and
immediately locks-out the burner. To release the burner, press the
release button and adjust the pressure switch to a sufficient level
to detect the existing air pressure during the pre-ventilation stage.
TBML_ACC_REG_001
28 / 50
0006160331_202310
ENGLISH
Содержание TBML 80 MC
Страница 2: ......
Страница 45: ...SCHEMI ELETTRICI TBML 50 MC 200 MC 43 50 0006160331_202310 ITALIANO...
Страница 46: ...TBML 50 MC 200 MC 44 50 0006160331_202310 ITALIANO...
Страница 47: ...45 50 0006160331_202310 ITALIANO...
Страница 49: ...TBML 260 MC 360 MC 47 50 0006160331_202310 ITALIANO...
Страница 50: ...TBML 260 MC 360 MC 48 50 0006160331_202310 ITALIANO...
Страница 51: ...TBML 260 MC 360 MC 49 50 0006160331_202310 ITALIANO...
Страница 95: ...WIRING DIAGRAMS TBML 50 MC 200 MC 43 50 0006160331_202310 ENGLISH...
Страница 96: ...TBML 50 MC 200 MC 44 50 0006160331_202310 ENGLISH...
Страница 97: ...45 50 0006160331_202310 ENGLISH...
Страница 99: ...TBML 260 MC 360 MC 47 50 0006160331_202310 ENGLISH...
Страница 100: ...TBML 260 MC 360 MC 48 50 0006160331_202310 ENGLISH...
Страница 101: ...TBML 260 MC 360 MC 49 50 0006160331_202310 ENGLISH...
Страница 103: ......