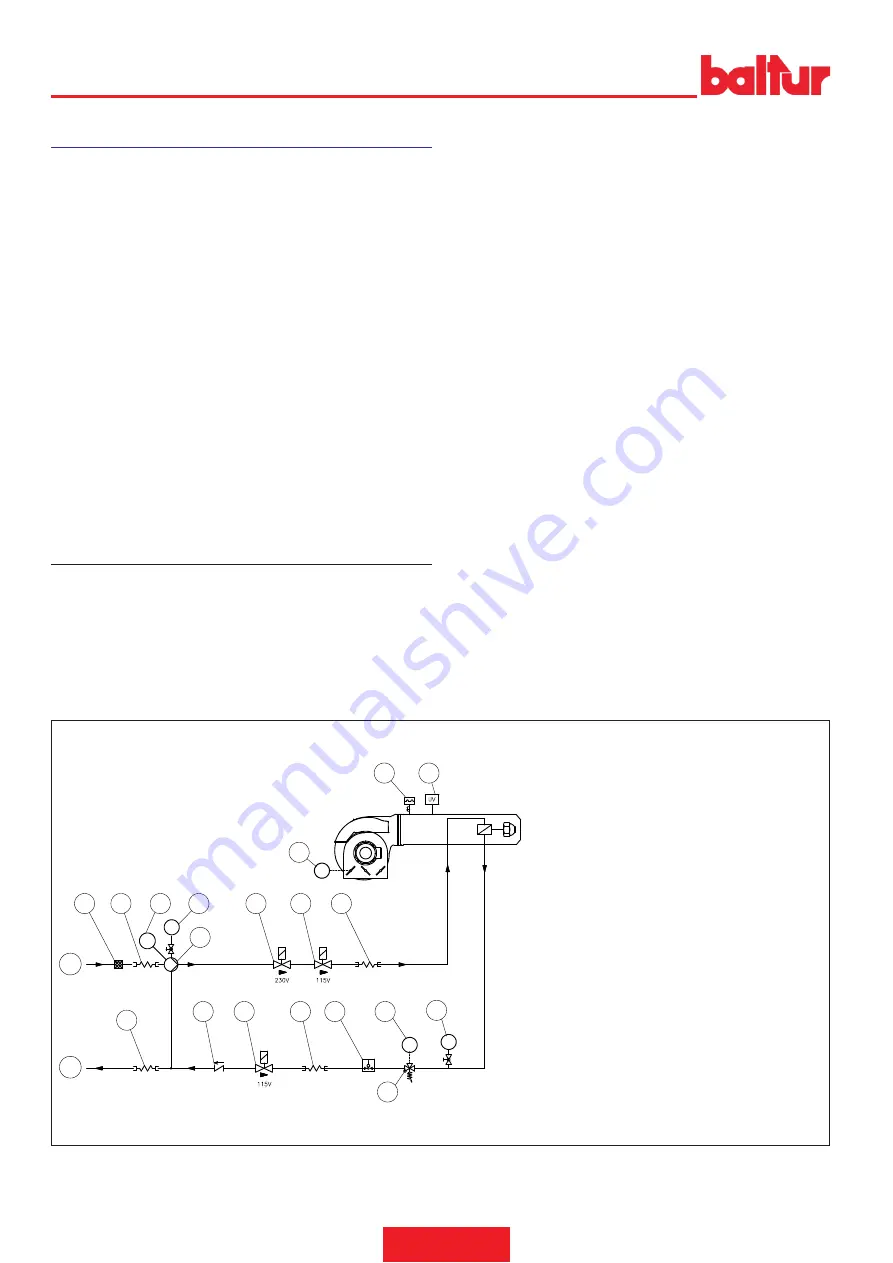
LIQUID FUEL SUPPLY SYSTEM
The burner pump must receive the fuel from a suitable supply circuit
featuring an auxiliary pump which may feature a pressure regulator
adjustable from 0.5 to 3 bar.
The fuel supply pressure to the burner pump must not change both
with burner off and with working burner at the maximum fuel output
required by the boiler.
The supply circuit can be realized without pressure regulator, using the
dedicated hydraulic diagram.
The pipe dimensioning must be carried out according to the pipe length
and the flow rate of the installed pump.
Where a removable fitting is required, use the welded flange method
with a fuel resistant gasket inserted to ensure a perfect sealing.
Avoid connecting the return pipe directly to the suction pipe.
Only return pipes can lead to a single manifold pipe with an adequate
cross section leading to the fuel tank.
The intake pipe should run up-slope towards the burner to avoid the
possible build-up of gas bubbles.
These instructions ensure a good operation of the product.
The anti-pollution prescriptions, as well as the provisions set forth by
the local authorities, refer to the specific publications in force in the
country where the product will be installed.
AUXILIARY PUMP
In some cases (excessive distance or differences in level) the system
must be implemented with a "loop" supply circuit with an auxiliary
pump, avoiding to connect the burner pump directly to the tank.
In this case, the auxiliary pump can be started when the burner starts
and stopped when it stops.
The electrical connection of the auxiliary pump is made by connecting
the coil (230V), which controls the pump remote control switch, to ter-
minals “N” (input terminal board of the equipment) and “L1” (downstre
-
am the motor remote control switch).
Always follow the instructions below:
•
The auxiliary pump must be installed as close as possible to the
liquid to be sucked.
•
The head must be suitable for the relative plant.
•
We recommend a flow rate equal at least to that of the burner pump.
•
The connection pipes must be dimensioned based on the flow rate
of the auxiliary pump.
•
Avoid electrically connecting the auxiliary pump directly to the remo
-
te control switch of the burner.
BLOCK DIAGRAM OF HYDRAULIC CIRCUIT
M
M
PI
M
PI
8
7
3
1
2
10
13
14
9
13
2
5
6
12
13
13
4
14
C
D
0002906610
11
1
Pump motor unit 25 bar
2
Pressure gauge 0 - 40 bar
3
Air regulation servomotor
4
Diesel return flow rate regulator (5,5 ÷ 17 bar)
5
Liquid fuel regulation servomotor
6
Maximum diesel pressure switch regulated at 5
bars
7
Air pressure switch
8
Flame sensor
9
Main delivery solenoid valve normally closed
10
Delivery safety solenoid valve normally closed
11
Return safety solenoid valve normally closed
12
Non-return valve
13
Flexible hose
14 Filter
C
System return
C
System delivery
12 / 34
0006160393_202104
ENGLISH
Содержание TBL 1000 ME
Страница 2: ......
Страница 30: ...SCHEMI ELETTRICI TBL 650ME 750ME 1000ME 28 34 0006160393_202104 ITALIANO ...
Страница 31: ...TBL 650ME 750ME 1000ME 29 34 0006160393_202104 ITALIANO ...
Страница 32: ...TBL 650ME 750ME 1000ME 30 34 0006160393_202104 ITALIANO ...
Страница 33: ...TBL 650ME 750ME 1000ME 31 34 0006160393_202104 ITALIANO ...
Страница 34: ...TBL 650ME 750ME 1000ME I1 I2 BA I4 I3 32 34 0006160393_202104 ITALIANO ...
Страница 36: ...34 34 0006160393_202104 ITALIANO ...
Страница 64: ...WIRING DIAGRAMS TBL 650ME 750ME 1000ME 28 34 0006160393_202104 ENGLISH ...
Страница 65: ...TBL 650ME 750ME 1000ME 29 34 0006160393_202104 ENGLISH ...
Страница 66: ...TBL 650ME 750ME 1000ME 30 34 0006160393_202104 ENGLISH ...
Страница 67: ...TBL 650ME 750ME 1000ME 31 34 0006160393_202104 ENGLISH ...
Страница 68: ...TBL 650ME 750ME 1000ME I1 I2 BA I4 I3 32 34 0006160393_202104 ENGLISH ...
Страница 70: ...34 34 0006160393_202104 ENGLISH ...
Страница 71: ......