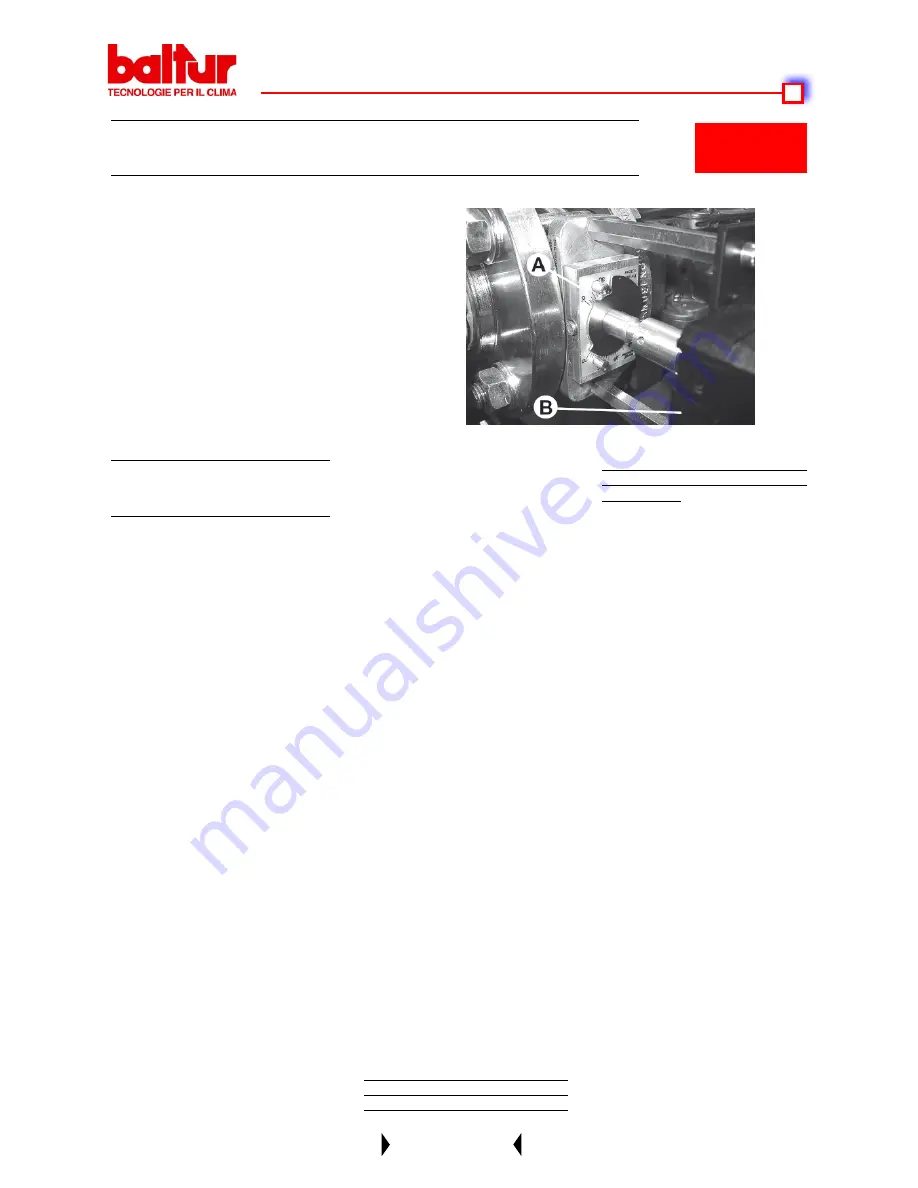
3 / 68
000608220_2007/03
DETAIL OF GAS FEED REGULATOR THROTTLE VALVE WITH
DUNGS SERVOMOTOR
A
Gas throttle valve position reference index
B
Gas modulation servomotor
N° 0002934220
Rev. 29/06/2004
1) If not already done at the moment
of connecting the burner to the gas
pipeline, it is indispensable to carry
out a purge of the air contained in
the pipeline. As a precaution, special
care should be taken and doors and
windows should be opened. Open
the pipe union on the pipeline situa-
ted near the burner and then open a
little the gas cut-off cock (or cocks).
When the characteristic odour of
gas can be smelled, close the cut-
off cock. Wait until the gas present in
room has dispersed, and then recon-
nect the burner to the gas pipeline.
Subsequently, re-open the gas cut-
off cock.
2) Check that there is water in the boi
-
ler and that the system’s gate valves
are open.
3) Check, with absolute certainty that
the discharge of combustion pro-
ducts can take place freely (boiler
and chimney lock-gates should be
open).
4) Make sure that the voltage of the
electric line to which the burner is
to be connected,corresponds to that
required by the burner and that the
electrical connections (motor and
principle line) have been prepared
to match the voltage rating available.
Also check that all the electrical con
-
nections carried out on the spot are
in accordance with our electric wiring
diagram.
5) Make sure that the combustion head
is long enough to enter the furnace
to the extent specified by the boiler
STARTING UP AND REGU-
LATION WITH METHANE
manufacturer. Check that the device
which regulates the air on the com
-
bustion head is in the position consi-
dered necessary for the fuel delivery
required (air passage between the
disk and the head should be consi
-
derably reduced when the fuel deli
-
very is reduced; on the other hand,
when the fuel delivery is fairly high,
the air passage between the disk
and the head should be relatively
open). See Chapter “Air Regulation
on the Combustion Head”.
6) Apply a manometer with an adequa
-
te scale (if the entity of pressure fo
-
recast allows it is preferable to use a
column of water instrument, do not
use a pointer instrument for modera-
te pressure) to the pressure plug on
the gas pressure switch.
7) Now insert the main switch. The con
-
trol box receives voltage in this way
and the programmer turns on the
burner as described in Chapter “De-
scription of Operations”. To adjust
the burner see the “MPA 22” electro-
nic cam instructions in the attached
manual code 0006080905.
8) After adjusting the “minimum”, (P)
bring the burner towards maximum
via the controls on the MPA 22
keypad. (see MPA 22 electronic cam
instructions in the attached manual
code 0006080905).
9) We recommend that you carry the
out combustion tests with the appro
-
priate instrument at all intermediate
points in the modulation range (from
P1 to P9); also check the gas flow
delivery rate via the meter.
It is essential to check, with a suita
-
ble instrument, that the percentage
of carbon monoxide (CO) present
in the fumes does not exceed the
maximum permitted amount of 0.%
(000 p.p.m.).
10) Now check automatic mode
working of the modulation (see “MPA
22” electronic cam instructions in en-
closed manual code 0006080905).
In this mode the equipment receives
the signal from the electronic modu-
lation adjuster RWF 40, if the burner
is modulating version, or from the
thermostat or the pressure switch
second stage if the burner is pro-
gressive two stage.
11) The air pressure switch has the job
of bringing the control box to a safety
shut down if the air pressure is not
at the correct value. Therefore, the
air pressure switch must be regu
-
lated in such a way as to intervene
by closing the contact (foreseen to
by closed while working) when the
air pressure in the burner has rea-
ched a sufficient level. The pressure
switch is self-controlled and therefo
-
re it must close the contact (fan stops
and consequently there is an absen
-
ce of air pressure in the burner) if it
does not, the control box will be in
-
serted (the burner remains at a sta-
dstill).It must be specified that if the
contact is not closed during working
(insufficient air pressure), the control
box will carry out its cycle, but the
ignition transformer will not be inser
-
ted and the gas pilot valves will not
open. Consequently, the burner will
go to “shut down”. Check that the
air pressure switch functions proper
-
ly with burner at minimum delivery,
increase the regulating value until it
reaches intervention point and the
burner should go to shut down. To