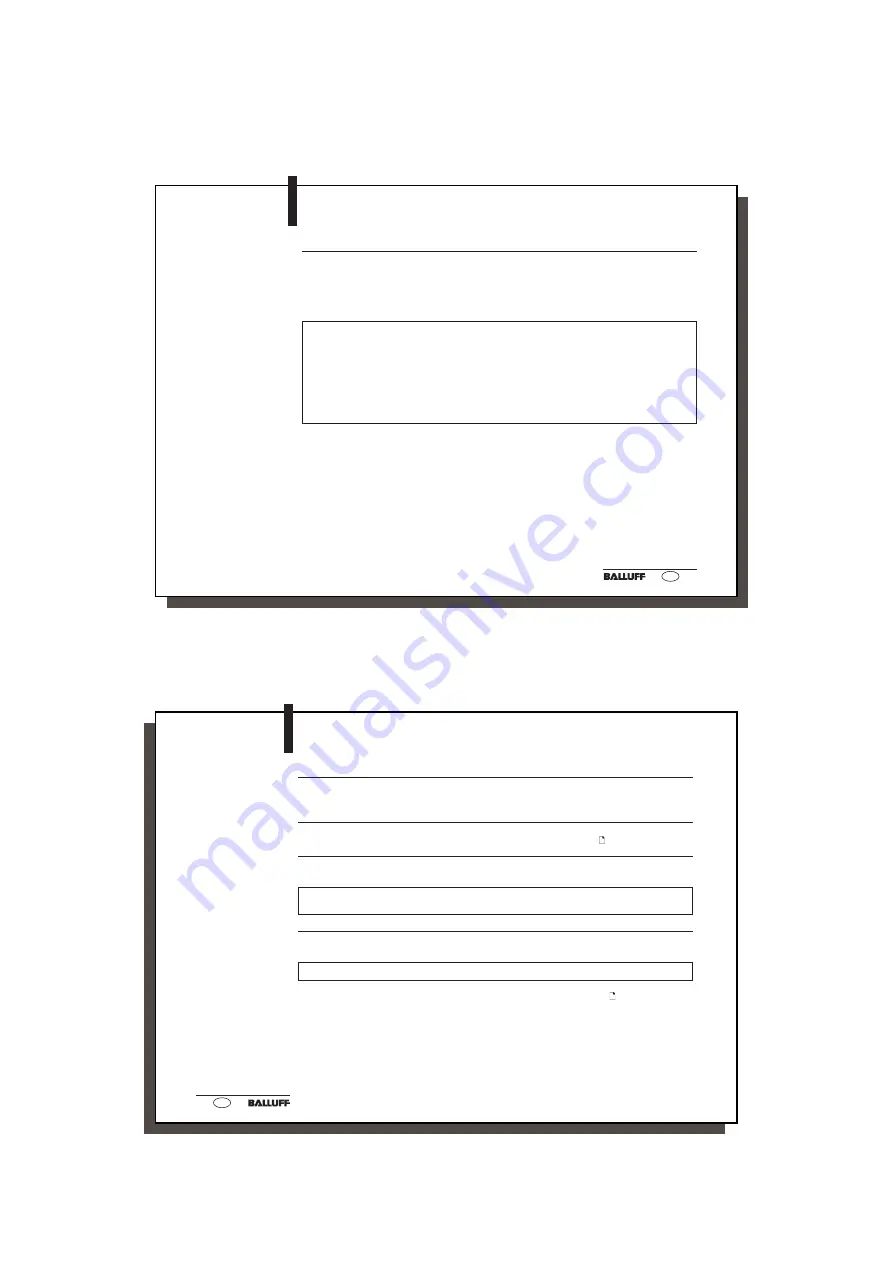
11
11
E
Communication between the BIS C-6_2 processor and the host system is via PROFIBUS-DP.
The PROFIBUS-DP system consists of 2 components:
– the bus master and
– the bus modules/slaves (here the BIS C-6_2 processor).
Important hints for use with PLC:
In some control systems the PROFIBUS-DP data area is not synchronously transmitted with the
updating of the input/output content. In such cases, either
– a PLC cycle must be programmed as waiting time between the evaluation of or reaction to
the bit header information and the processing of the data, or
– the function "2nd bit header" should be switched on while parametering. When the 1st and
the 2nd bit header are identical, then this indicates that the current data are valid .
Application
BIS C-6_2 Processor
PROFIBUS-DP
☞
C6_2-019_641365_0506-e.p65
12
12
E
Parametering
Station Address
For the correct parametering of the bus master as per type, a diskette, containing the unit’s
master data in the form of a GSD file is included with the BIS C-6_2 processor. The diskette
also contains type files for the Siemens bus master.
The Processor BIS C-6_2 is delivered with the station address 126. These has to be set
individually before using in a bus system. See informations on following .
An input buffer and an output buffer are used for the data exchange with the control system.
The size of these buffers has to be configured via the master.
The possible settings are entered in the GSD file (and Type file). A minimum of 6 and a maxi-
mum of 32 bytes can be accommodated. However, it must be an even number.
Besides, in the case of the BIS C-6_2 processor, there are 4 further bytes (User-Parameter-
Bytes) which have to be set while parametering.
The preset values are entered in the GSD file (and Type file).
The significance of the 4 bytes for parametering is described starting from 14.
Input/Output Buffer
Unit's Master Data
Parametering Bytes
User-Parameter-Bytes
☞
☞