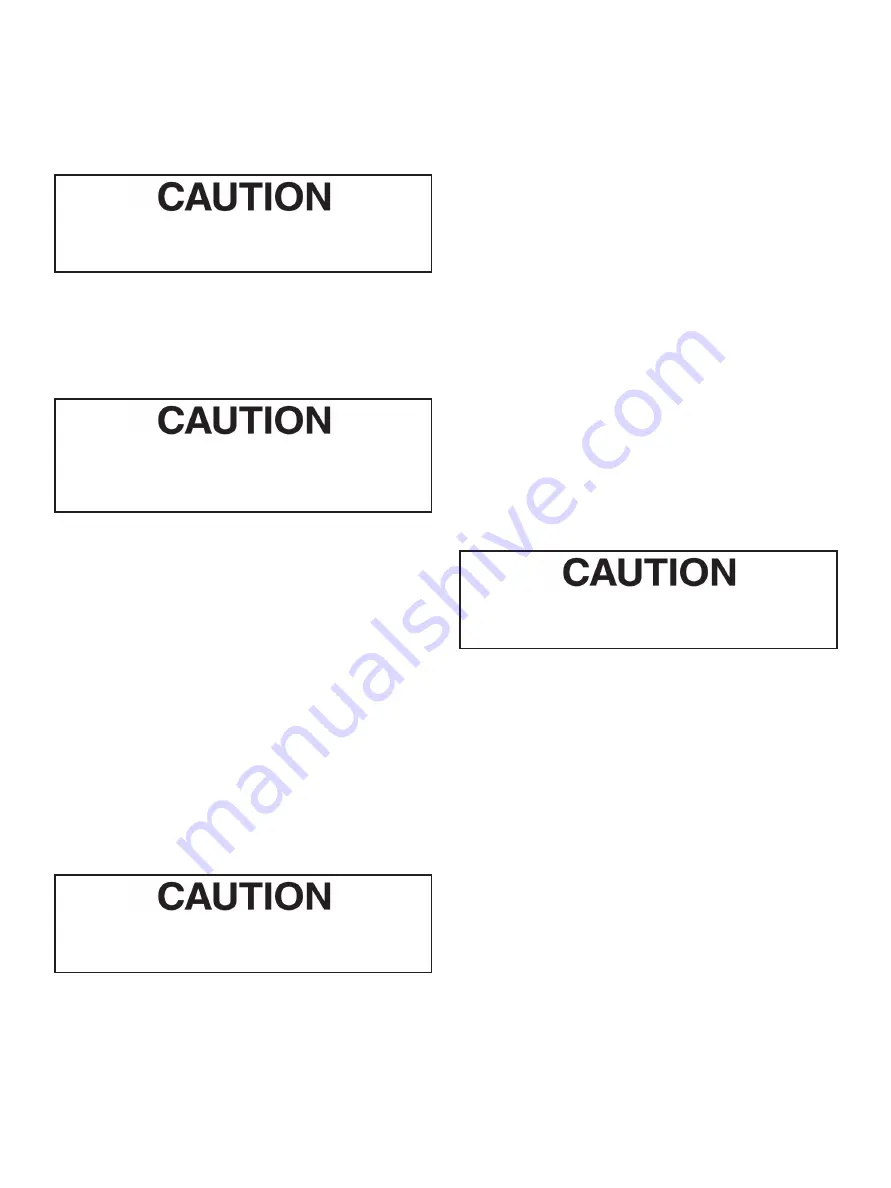
3 | Baker Hughes
Copyright 2021 Baker Hughes Company. All rights reserved.
5. Air Piping
The actuators are designed to accept 1/4” NPT air supply piping.
Use 1/4” OD tubing (4 x 6 mm) or equivalent for all air lines. If the
supply air line exceeds 25 feet in length (7 meters) or if the valve
is equipped with volume boosters, then 3/8” tubing (6 x 8 mm) is
preferred. AII connections must be free of leaks.
Do not exceed supply pressure indicated on serial
plate located on the yoke of the actuator.
6. Body Disassembly
Access to the internal components of the body should be
accomplished with the actuator removed. To remove the
actuator from the body, refer to the actuator instruction Ref.
GEA19530 for a type 87/88 multi-spring actuator.
Prior to performing maintenance on the valve, isolate
the valve and vent the process pressure. Shut off the
supply air line and the pneumatic or electric signal line.
6.1 Quick-Change Trim
After removing the actuator, disassemble the body using the
following procedure:
A.
If there is a leak detection connection on the lateral NPT
port of the bonnet, disconnect this piping as well.
B.
Remove body stud nuts (10).
C.
Remove bonnet (8), and plug stem (1) and plug (15) sub-
assembly together as one unit.
D.
Since the cage (12), seat ring (13) and seat ring gasket (14)
are held in place by the bonnet, they may now be removed
Note: Spiral wound gaskets (11 & 15) are standard in the
21009 Series design and it is imperative that new gaskets
be installed each time the valve is disassembled.
E.
Remove packing flange stud nuts (3), packing flange (4) and
packing follower (5).
F.
Remove plug (15) and plug stem (1) sub-assembly from the
bonnet (8).
Care must be taken to avoid damage to the plug and
plug guide.
G.
Remove old packing (6) [and optional lantern ring (7) if a leak
detection connection has been installed]. Refer to Figure 4.
H.
All components may now be inspected for wear and service
damage. After determining the maintenance required, proceed
to the appropriate Section of this instruction manual.
7. Maintenance and Repair
The purpose of this section is to provide recommended
maintenance and repair procedures. These procedures assume
the availability of standard shop tools and equipment.
7.1 Lapping Seat
Lapping is the process of working the valve plug against the
seat ring with an abrasive to produce a close fit . If valve
leakage is excessive, lapping becomes necessary. The plug and
seat ring seating surfaces should be free of large scratches or
other defects, and the contact surfaces of the seats should be
as narrow as possible. This may require dressing both parts in
a lathe. The seating surface angle of the plug is 28 degrees and
the seat ring is 30 degrees (relative to the centerline axis). A
good grade of fine grinding compound is required for the lapping
operation.
The compound should be mixed with a small quantity of
lubricant such as graphite. This will slow the cutting rate
and prevent tearing of the seating surfaces. The amount of
lapping required depends on the materials, condition of seating
surfaces, and accuracy of machining. lf a short period of lapping
does not visibly improve seating, there is usually no advantage
in continuing as excessive lapping may result in rough seats.
The only remedy is replacement or re-machining of one or both
parts. When lapping new plugs and seat rings, begin with a
medium fine (240 grit) and finish with a finer grade (600 grit).
Note: Lapping should produce a line contact area, not the
entire surface, due to the difference in seat angles.
Before lapping, the plug and stem sub-assembly must
be concentric. (See pinning operation, section 7.5)
7.1.1 Quick-Change Trim
1. CIean body gasket surface areas.
2. Install a new seat ring gasket (14) and insert seat ring (13) in
the body.
Note: Gasket (14) is temporarily placed to hold the seat ring
during lapping.
It is imperative to use a new gasket or a test part having the
same geometrical characteristics in order to ensure the
correct position of the seat ring during lapping.
This gasket (or similar part) can be kept after lapping for
future use.
The gasket used for lapping must not be reused for the
body reassembly.
3. Apply lapping compound at several spots equally spaced
around the seating area of the seat ring.
4. Insert the cage (12) into the body.
5. lnsert the stem and plug sub-assembly carefully into the
body until it is seated.
6. Place bonnet (8) on the body.