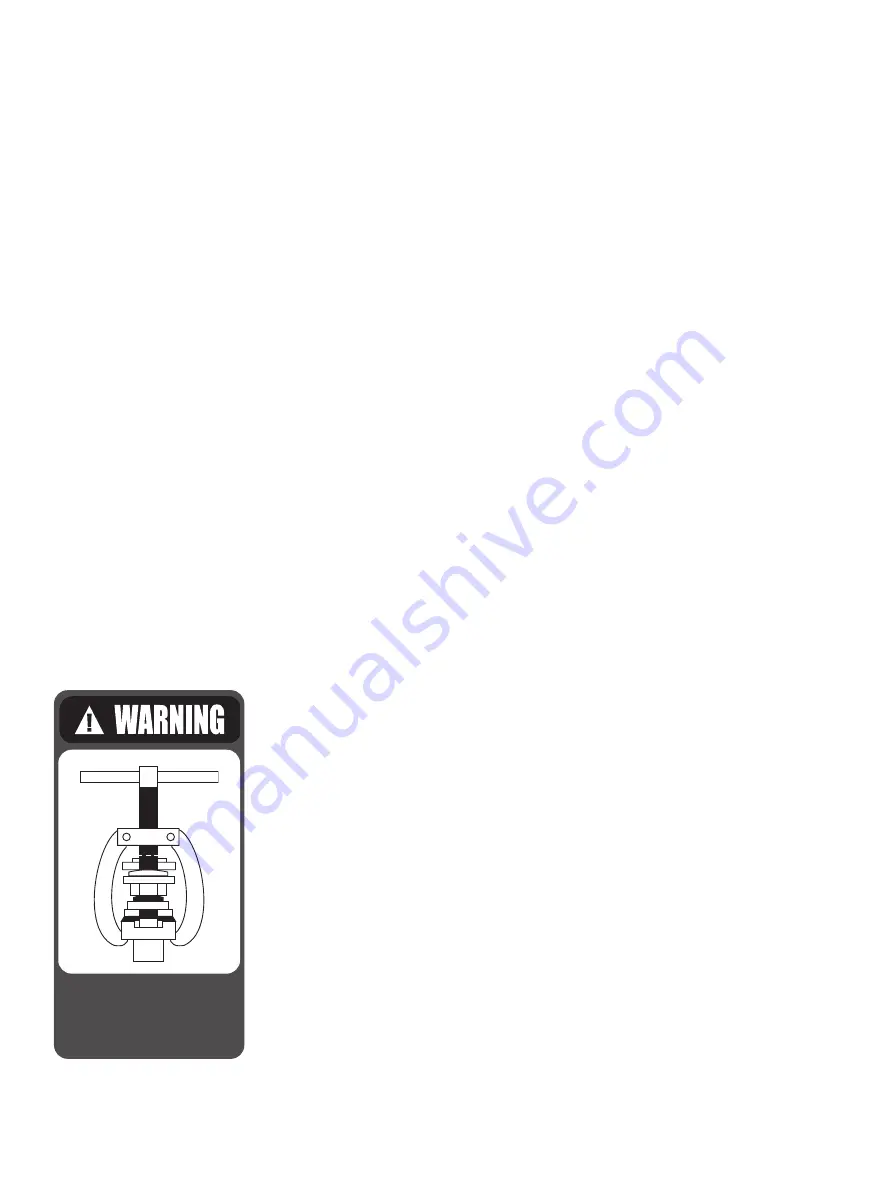
Consolidated 1511 Series Safety Valve Instruction Manual
| 23
© 2020 Baker Hughes Company. All rights reserved.
notch (as viewed through the ring pin hole, move
the adjusting ring from the right to the left to
lower the adjusting ring). Remove the gag, retest
and note the reseating pressure of the valve it
should close sharply at a higher pressure.
g. If the valve closes sharply but the reseating
pressure is too low in comparison to the standard
in Table 10, blowdown is excessive. Gag the
valve, remove the upper ring pin, raise the upper
adjusting ring 10 notches, replace the ring pin,
remove the gag and retest the valve. If the
reseating pressure has not risen enough to meet
the blowdown standard, repeat the procedure
until the blowdown standard is achieved.
Note: It may be possible that in raising the upper
adjusting ring to reduce the blowdown,
the valve may develop a hang up, correct
it as described in Step f. above, and
then continue if necessary to reduce the
blowdown.
h. If the blowdown is less than the standard
required, the reseating pressure can be lowered
by gagging the valve, removing the upper ring
pin and lowering the upper adjusting ring 10
notches (as viewed through the ring pin hole,
move the adjusting ring from the right to the
left.) Remove the gag, replace the adjusting
ring pin and retest the valve. If the reseating
pressure is not reduced enough to meet the
standard, repeat this procedure until the
standard is achieved. The upper adjusting
ring should be positioned to provide no more
blowdown than that indicated in Table 9.
8. Once the valve has tested in compliance with
the appropriate standard, conduct two more
verification tests. All external adjustments should
be sealed after completing final setting.
9. Proceed to the next valve to be tested.
XIV. Setting and Testing (Cont’d)
B. Hydrostatic Testing & Gagging
B.1 General Information
During any hydrostatic test all safety valves on the unit must be gagged. This
gagging procedure prevents the possibility of damage to the safety valve internals in
the event that the test pressure exceeds the safety valve set pressure.
When hydrostatic pressure will exceed the set pressure of the safety valve, it is
recommended the valve be replaced with a blind flange during hydrostatic testing.
Probably the most common source of safety valve trouble is overgagging. During
hydrostatic testing, and during safety valve setting, gags should be applied only
hand tight. During setting, overgagging could cause damage to the seating surface
and result in leakage. In applying gags, remember that the valve spring will hold the
valve closed against its set pressure. The additional gag load applied should be only
enough to ensure that the valves do not lift at the expected over-pressure.
Gags should never be applied when the boiler is cold. The spindle of the safety
valve expands considerably with the temperature increase as pressure is raised. If it
is not free to expand with this temperature change, the spindle may be damaged.
Boiler pressure should be increased to 80 percent of the pressure of the low set
valve before applying the gags.
Hand tighten the gags of drum and superheater valves with only a light force.
Gag safety valve during
ring adjustments to
avoid possible severe
personal injury or death.