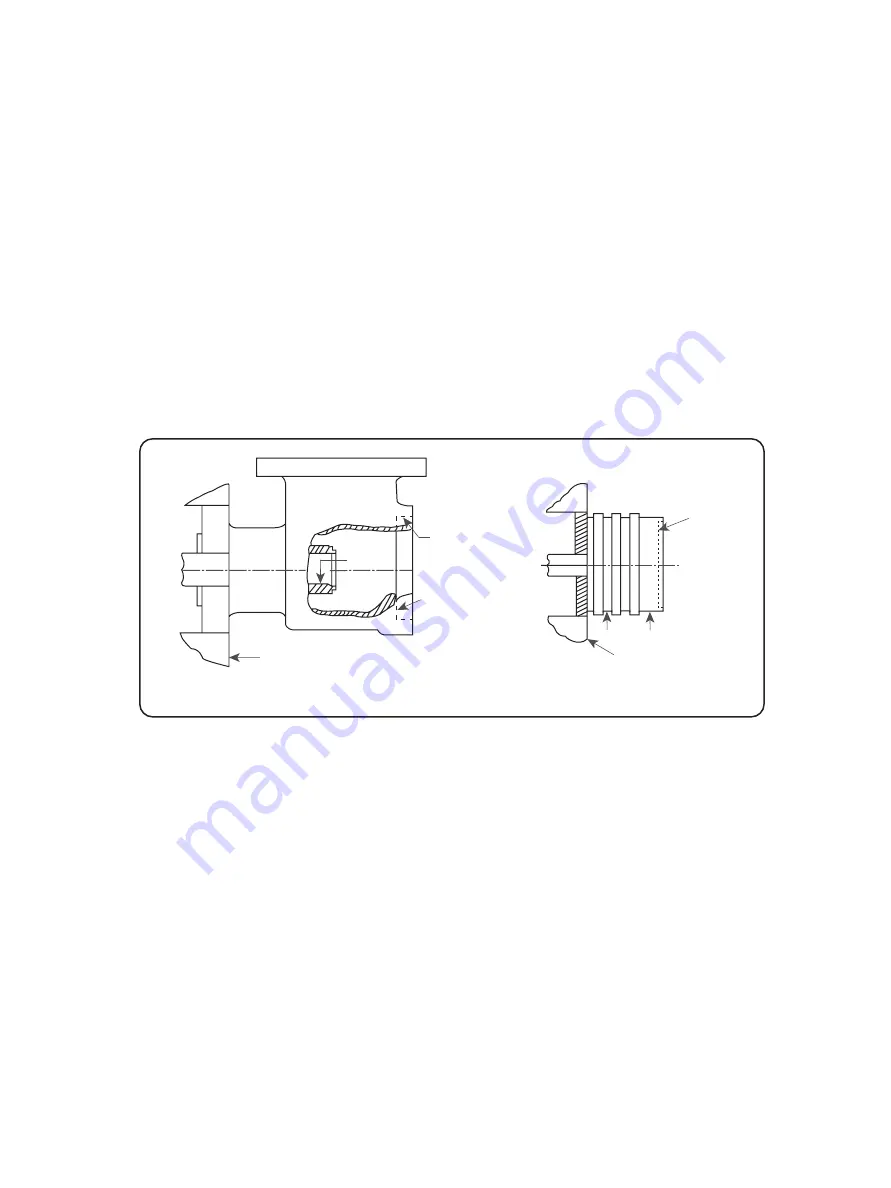
Consolidated 1511 Series Safety Valve Instruction Manual
| 15
© 2020 Baker Hughes Company. All rights reserved.
XI. Maintenance Instructions (Cont’d)
After the parts have been determined to be reusable,
proper machining technique must be employed in
reestablishing disc and seat bushing dimensions.
On 1511 Series safety valves, the seat bushing should
be machined in the valve base to ensure proper parts
alignment. When chucking the valve base or disc into
a lathe, alignment must be within .001” (0.03 mm) total
indicator runout at the points indicated in Figure 4 as “A”,
“B”, and “C”.
Figure 4
A
A
B
B
C
C
Chuck Jaws
Chuck Jaws
Note: See Section XII.B for rework dimensions for the Seat Bushing and Flat Solid Discs.
B. Machining
All of the above tools can be purchased from Baker
Hughes, with prices in effect at the time of delivery.
It may not be necessary to use all of the ring laps at
any one time, but having a sufficient supply on hand
will save reconditioning time during a boiler outage.
After the boiler is back in operation, the ring laps can
be reconditioned on the flat lapping plate. Lapping
compound, when used with ring laps, wears off the seat
surface on the disc or seat bushing, but it also wears off
the flat surface of the ring lap. A lap should not be used
on more than one valve without being reconditioned.
Lapping procedure for reconditioning the seating
surfaces of the disc and seat bushing is outlined in
Section XI.C.
C. Lapping Procedures
1. General:
While the finer points of lapping may be considered
a mechanical art, it is possible for the average
mechanic to produce satisfactory results with some
practice. No effort has been made in this manual
to establish an exact procedure to cover each and
every case because different people can achieve the
same results using their own techniques.
The following materials will be of assistance when
lapping bushing and/or disc seats:
a. Two ring laps per valve
b. 1-A Clover Grinding Compound
c. 1000 grit Kwik-Ak-Shun Grinding Compound
d. Lint free wipers for cleaning
2. Lapping the seat bushing or Disc Seat:
Before lapping the seat bushing and disc, use a
fine grade sandpaper to lightly break the inner
edge and outer edge of the bushing and disc seats.
This chamfer should not exceed .002” (0.05mm).
If the seating surfaces require extensive lapping or
reconditioning, machining should be considered prior
to lapping. See Inspection Section XII.B for criteria.
Cover one flat surface of a ring lap with a thin coating
of Clover 1-A Grinding Compound and gently set the
lap on the seat surface. Thick coatings tend to round
off edges of the seat.
Lap using a slight oscillating
motion in various directions. Control the motion of the
lap to prevent the inside edge or outside edge of the
lap from running off the seating surface, as this may
cause the seat to become scratched or uneven.