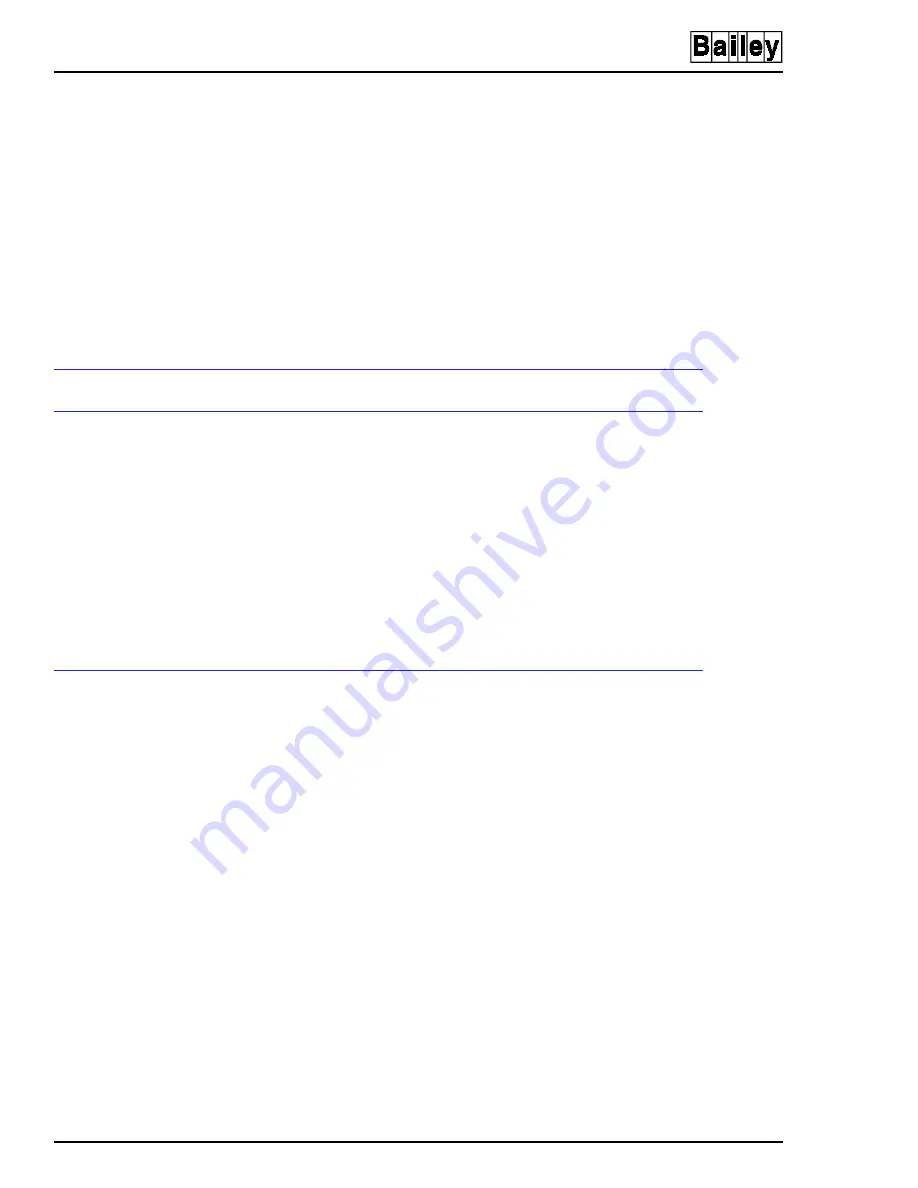
DESCRIPTION AND OPERATION
AUTOMATIC ADJUSTMENTS AND CORRECTIONS
2 - 6
I-E96-301B
®
IMASI03 module and the channel number on the slave module
connected to an analog input signal.
The type of the input, and the zero and span in engineering
units, must also be specified to ensure proper scaling and cor-
rections for calibration, cold junction compensation and non-
linearity correction.
Add function code 215 and 216 to the master MFP to configure
the IMASI03. Set function code 217 in the master MFP to cali-
brate the IMASI03 or to set the user gain and offset values.
Refer to the
Function Code Application Manual
I-E93-900-20
for more information.
AUTOMATIC ADJUSTMENTS AND CORRECTIONS
Input Processing
The IMASI03 slave scans all active inputs at a rate determined
by the requested input channel resolution. A preset conversion
time is determined for the A/D converter depending upon the
configured input resolution. Conversion time specifies the
length of time required for a single conversion. The input scans
from one active channel to the next, as fast as the conversion
time allows.
In addition to the active input channels, the built-in cold junc-
tion reference, and the reference values for drift correction are
digitized during normal input scanning.
Point Value Calculation
The slave maintains a set of adjustment values for each input
channel. These values correct for offset, gain and nonlinearity
errors in the input channel. The raw analog-to-digital converter
count value is first adjusted for any drift in the accuracy of the
input channel components. The resulting value is then con-
verted to an actual input signal value using the calibration
data which also adjusts for any nonlinearity in the input chan-
nel circuitry. The lead wire resistance is then taken into
account and the required adjustment is made.
For thermocouple inputs, an adjustment is made for the cold
junction temperature of the thermocouple. An additional,
user-specified adjustment is then applied, if one has been
defined with function code 217. The final corrected input read-
ing is then converted to engineering units using either thermo-
couple or RTD conversion tables, or the engineering unit zero
and span values specified for the input.
The following sections describe the various types of input value
adjustments.